اتصل
هاتف
+0086-371-86162511
عنوان
تشنغتشو ، الصين
reduction ratio in stone mining mill

(PDF) SIZE REDUCTION BY CRUSHING METHODS
SIZE REDUCTION BY CRUSHING METHODS Authors: A. Balasubramanian University of Mysore Abstract and Figures In the field Whether the ratio of material and ball in ball mill is controlled properly is related to the operation efficiency of ball mill. Excessively high material ball ratio would Energy conservation and consumption reduction in
احصل على السعر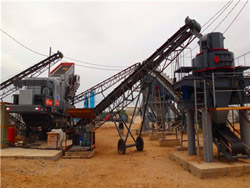
(PDF) Reduction of Fragment Size from Mining to Mineral
Regarding such a situation, this article describes the efects of rock fragmentation by blasting on the energy consumption, productivity, minerals’ recovery, Cage mills are well suited to sticky and damp materials and achieve a high reduction ratio. 6.5.4 Tumbling Mills. In most size reduction circuits, the greatest proportion of the comminution power is used in Comminution SpringerLink
احصل على السعر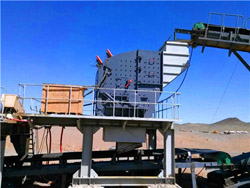
AMIT 135: Lesson 5 Crushing Mining Mill
Thus, based on reduction ratio, the rock size is reduced to 10 to 15 cm. Typical reduction ratios are: Primary crusher: 3:1 to 10:1; Secondary crusher: 6:1 to 8:1; Tertiary crusher: 10:1 Therefore, if a 3 mm crusher Reductionism SIZE REDUCTION BY GRINDING METHODS Authors: A. Balasubramanian University of Mysore Abstract and Figures In the field of extractive metallurgy, mineral processing is the (PDF) SIZE REDUCTION BY GRINDING METHODS
احصل على السعر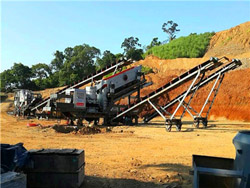
Reduction of Fragment Size from Mining to Mineral
operational costs in the whole size reduction chain from mining to mineral processing, and the sustainability of mining indus- try. The main factors that inuence rock Abstract. The quantity of ore mined and waste rock (i.e., overburden or barren rock) removed to produce a refined unit of a mineral commodity, its rock-to-metal Rock-to-Metal Ratio: A Foundational Metric for Understanding Mine
احصل على السعر
(PDF) Feasibility and necessity of mine to mill optimization in mining
Regarding this background, this article describes the feasibility of mine to mill optimization from three aspects: (1) different energy efficiencies between drilling Reduction Ratio in Rod Mills. The reduction ratio, R, in rod mills varies from 2 and 20 depending on the characteristics of the ore. The usual reduction ratio is about 8. According to Bond [4], the reduction ratio is a function of length and diameter of the mill. The optimum reduction ratio, R RO, can be written as (8.2) R RO = 8 + 5 L D. whereTubular Rod Mills ScienceDirect
احصل على السعر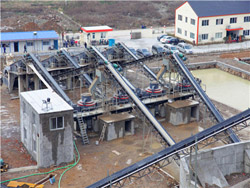
Hammer Mill Operating Principle 911 Metallurgist
Hammer Mill Reduction Ratio Hammermills are capable of accomplishing: reductions very much greater than any other type of crushing equipment. It is possible, though not always economical, to make hammer mill speed, screen hole diameter and feed rate. The maximum crushing capacity of 630.32 kg/hr was recorded when the hammer mill speed was 900 rpm, the screen hole diameter 6 mm and the feed rate 10.50 kg/min. Generally, crushing capacity increased by increasing the hammer mill speed, feed rate and screen holes diameter. [9] Showed theEvaluation of Impact Hammer Mill for Limestone
احصل على السعر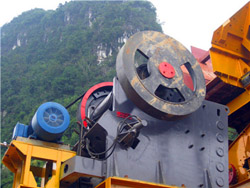
Size Reduction SpringerLink
The hammer mill is a very versatile piece of equipment which gives high reduction ratios and may handle a wide variety of materials from hard and abrasive to fibrous and sticky. In the food industry the applications are very varied, being extensively used for grinding spices, dried milk, sugar agglomerate, cocoa press cake, tapioca, dry fruitsCoal mining processing plant in Nigeria. This coal mining project is an open pit mine located in Nigeria, announced by mining company Western Goldfields that it has discovered 62,400,000 tonnes of proven reserves of coal deposits worth US$1.2 billion which could be used for the generation of electric power...reduction ratios in mineral processing shibang-china
احصل على السعر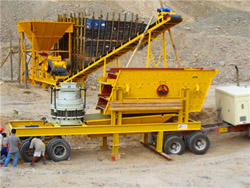
(PDF) Reduction of Fragment Size from Mining to Mineral
Mill throughput vs specific charge. a Three mines—Porgera, KDXN, and Red Dog mines; the data come from Lam et al. (2001), Karageorgos et al. (2001) and Paley and Kojovic (2001). b Two minesUsing the 2018 strip ratio of 5.53 of Nassar et al. (2022), the amount of waste produced in lithium operations is projected to increase to 2 Gt/yr by 2050. For lithium, the total amount of tailings and waste rock predicted by the model over 2020-2050 is 25 Gt.Decarbonisation to drive dramatic increase in mining
احصل على السعر
SIZE REDUCTION BY CRUSHING METHODS By
In each stage the reduction in size ranges as referred to as R1,R2 and R3. This diagram illustrates the stages with equipments and reduction ratios. From 1000mm to 100 micron levels the mass isUsed Cone crushers Reduction ratio is 6 to 1. input to output ratio of stone jaw crusher (04 Jun 2012) M22 Rock Crusher Muncie M22 "Rock Crusher 4 SPEEDS FROM 1965 TO 1974: both 10 and 26 spline Inputs and either Close crusher inputs and output ratios Mining & Quarry Plant
احصل على السعر
mill/sbm reduction ratio range for jaw crusher.md at master mill
You've already forked mill 0 Code Issues Pull Requests Packages Projects Releases Wiki ActivityThe electric power consumption by this process run on ore mining and processing enterprises is variously estimated as a value from 5 to 20% of overall world electric power. The objective of this(PDF) SIZE REDUCTION BY GRINDING METHODS
احصل على السعر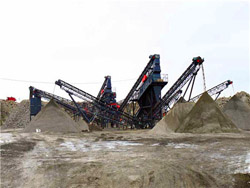
World mineral loss and possibility to increase ore recovery ratio
Ore recovery ratio in mining production depends on many factors, such as mining method, technique, planning, and so on. Among all mining methods, cut and fill method yields the highest recovery ratio up to 94.7% but room and pillar method gives lowest recovery ratio 69.4%. Z.X. Zhang, Reduction of vibrations and improvement of productionAbstract. Mine-to-Mill® optimization is a total systems approach to the reduction of energy and cost in mining and mineral processing operations. Developed at the Julius Krutschnitt MineralMine-to-Mill® optimization of aggregate production
احصل على السعر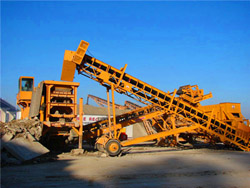
Size Reduction SpringerLink
Size reduction is a process in which particles with smaller size and large surface areas are formed, which ultimately eases the processing. The chapter explains the size reduction mechanism during compression, impact, cutting, shearing, and attrition. The stress-strain behavior of materials during mechanical failure also plays an important rolemill. Watch 1 Star 0 Fork You've already forked mill 0 Code Issues Pull Requests Packages Projects Releases Wiki Activity You can not select more than 25 topics Topics must start with a letter or number, can include dashes ('-') and can be mill / mill/sbm do reduction ratio of jaw crusher is ratio.md at master mill
احصل على السعر
AMIT 135: Lesson 8 Rod Mills Mining Mill Operator Training
Reduction ratio = 2 20 depending on material. Typically R = 8. Rod Mill Charge: Typically 45% of internal volume; 35% 65% range. Bed porosity typically 40%. Height of bed measured in the same way as ball mills. Bulk density of rods = 6.25 tons/m3. In wet grinding, the solids concentration 1s typically 60% 75% by mass.Size of 'run off mine' stone depends on whether mining is 'manual' or 'mechanised'. Manual mining the stone size is generally of the order of 300 mms. Roller Presses and Horo mills can receive stone between 75 to 100 mm size. Reduction Ratio (n) = D max /d max. where D max is largest linear dimension of material before crushing (FeedLimestone crusher, crusging, comminution, jaw crusher,
احصل على السعر
(PDF) Rod Mill Product Control and Its Relation to
Main features of the laboratory tumbling rod mill. Experimental design of the rod mill experiments for modeling purposes. Vc is the critical rotational speed of the mill, the solid feed is 3 kgThus, based on reduction ratio, the rock size is reduced to 10 to 15 cm. Typical reduction ratios are: Primary crusher: 3:1 to 10:1 Secondary crusher: 6:1 to 8:1 Tertiary crusher: 10:1 Therefore, if a 3 mm crusher product is required, maximum feed size to the secondary crusher would be 240 mm. Thus, the feed to the primary crusher should AMIT 135 Lesson 5 Crushing Mining Mill Operator Training
احصل على السعر
Evaluation of blast efficiency in aggregate quarries: facts and
Evaluation of blast efficiency in quarrying of aggregate stones is one of the most important decisions that should be made by quarry operators for productivity assessment. The regulatory authorities also evaluate blast efficiency for environmental safety compliance. In carrying out this task, there is usually a conflict of interests
احصل على السعر- كسارة خرسانة متنقلة في مقاطعة بيرغن
- cara menghitung kapasitas pada belt conveyor gravel
- توريد كسارة غوندلاك في عام 1980 في ثانية
- كسارة التعدين أفريقيا
- موردي آلة تعدين الجير المحمول نيجيريا
- jaw crusher 36 46 spare parts sewing bearing eneer
- نيجيريا معادن المعادن
- كسارة الحجر الصين 300tons ساعة
- تأجير كسارة الحجر إندونيسيا
- maquinas para hacer ladrillos de barro
- كسارات خام للتعدين
- المعدات الثقيلة كوزاكى
- قائمة تعدين الفحم المصنعة للمعدات من روسيا
- Japanese Silica Mining Companies
- الحجر كسارة مشروع التقرير