اتصل
هاتف
+0086-371-86162511
عنوان
تشنغتشو ، الصين
Effect Of Ball Mill Parameters On Performance

Comparative Study on Improving the Ball Mill Process
Optimization results confirmed that the balls to powder weight ratio were the most influential process parameter. The optimum process parameters setting concluded that balls to powder weight ratio are 20:1, the optimum ball mill working Grinding performance, regarding material breakage and power consumption, has been studied and reported in the literature with a broad range of operating parameters, such Performance optimization of an industrial ball mill for SciELO
احصل على السعر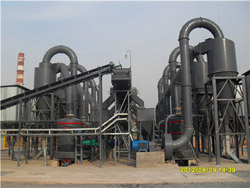
Influences of operating parameters on dry ball mill performance
Within the context, the influence of operating parameters such as mill speed, ball filling ratio, ball size distribution, powder filling ratio, grinding aid dosage and In the ball milling process, when the types of starting powders are already fixed, the quality characteristics are determined by processing parameters, such as Analysis of individual and interaction effects of processing
احصل على السعر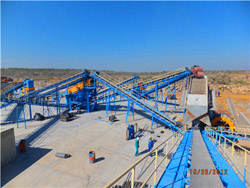
Effects of Ball Size Distribution and Mill Speed and Their
When the mills charge comprising 60% of small balls and 40% of big balls, mill speed has the greatest influence on power consumption. When the mill charge is Abstract. With a view to developing a sound basis for the design and scale-up of ball mills, a large amount of data available in the literature were analyzed for Analysis of ball mill grinding operation using mill power
احصل على السعر
The effect of ball size on mill performance ScienceDirect
Scale-up of mills is critical to the design and operation of industrial grinding circuits. This paper presented a scale-up model based on the discrete element method The effect of ball milling parameters on the performance of ultracapacitors needs to be investigated. Most significant factors of ball milling parameters of electrode Process-Based Statistical Modeling for Ball Mill Machine
احصل على السعر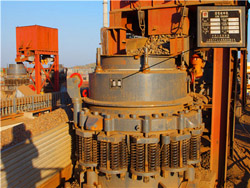
Effect of ball size and powder loading on the milling efficiency of a
The ball mill process is very complicated process governed by many parameters, such as ball size, ball shape, ball filling, slurry loading (with respect to ball The high-energy ball milling method was adopted to explore the influence of ball milling parameters, such as milling speed and additive amounts of process control agent (PCA) on tungsten powder. Metals Free Full-Text Effect of Ball Milling
احصل على السعر
Effect of ball milling process on the photocatalytic
CdS/TiO 2 composite photocatalysts were made by the method of secondary ball milling at different ball milling speeds, milling time, and material ratios. After the secondary ball milling process, parts of the 2.3+ billion citations. Download scientific diagram a) Cement ball mill view, b) Cement mill sketch. from publication: Effects of Mill Speed and Air Classifier Speed on Performance of ana) Cement ball mill view, b) Cement mill sketch.
احصل على السعر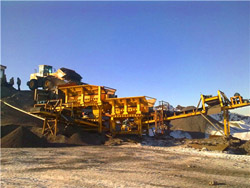
The effect of ball size on breakage rate parameter in a pilot
Ball size is a critical parameter influencing the performance of a ball mill, particularly for multi-compartment ball mills used in cement industry. Effect of design and operational parameters on particle morphology in ball mills. International Journal of Mineral Processing, Volume 165, 2017, pp. 41-49.In this paper, we analyzed the individual and interaction effects of the key processing parameters on the wet grinding performance in a ball mill for alumina powder using statistical methods. The grinding performance was evaluated based on three quality characteristics of milled alumina powder: the median particle size ( d 50 ), width and Ball mill simulation in wet grinding using a tumbling mill and its
احصل على السعر
Effects of grinding aids on model parameters of a cement ball mill
The circuit consists of a two compartment ball mill and a dynamic air classifier. There is a slotted diaphragm inside the ball mill that separates the two chambers from each other. The particles coarser than the size of the slots (10 mm) stay in the first chamber while the finer particles pass the second chamber for further size reduction.One of the most energy-intensive processes for producing submicron range calcite is stirred media mill. In the present work, numerous operating parameters such as solid mass fraction, grinding media size, media filling ratio, and grinding time have been investigated using a vertical type stirred media mill. The results are evaluated on Effect of Operating Parameters on the Breakage Process of
احصل على السعر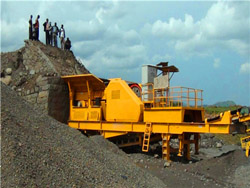
(PDF) Performance optimization of an industrial ball mill for
An increase of over 10% in mill throughput was achieved by removing the ball scats from a single -stage SAG mill. These scats are non- spherical ball fragments resulting from uneven wear of ballsIn order to explore the impact of different ball milling technical parameters on the grain size of nano silicon powder, this paper adopted the orthogonal experimental design in combination with fitting analysis, and set the agitator shaft speed of the ball mill and the milling time as the influence factors.The Impact of Ball Milling Process Parameters on the Preparation
احصل على السعر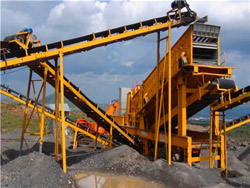
Metals Free Full-Text Effect of Ball Milling Parameters on the
The high-energy ball milling method was adopted to explore the influence of ball milling parameters, such as milling speed and additive amounts of process control agent (PCA) on tungsten powder. The morphology and microstructure of tungsten powder in the process of refinement were characterized by field-emission scanning electron Ultra-fine grinding involves a large number of parameters in its operation. In this paper, four important parameters of the Drais stirred ball mill, i.e., the bead density, slurry density, mill speed, and the effect of dispersant were selected for investigation. The experimental work was based on a factorial design and 27 milling tests wereA study on the effect of parameters in stirred ball milling
احصل على السعر
Effect of ball size distribution on milling rate ScienceDirect
Abstract. This paper focuses on the determination of the selection function parameters α, a, μ, and Λ together with the exponent factors η and ξ describing the effect of ball size on milling rate for a South African coal. A series of batch grinding tests were carried out using three media single sizes, i.e. 30.6, 38.8, and 49.2 mm.Commercial powders of magnesium were processed by high-energy ball milling (HEBM) using a two-stage composite process. The microstructural and morphological evolution of the powders was studied using scanning electron microscopy (SEM), energy-dispersive spectrometry (EDX), and X-ray diffraction (XRD). From the results obtained, it Effects of two-step high-energy ball milling process and hot
احصل على السعر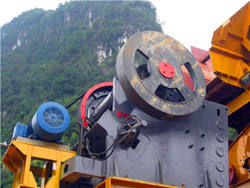
Effect of ball size distribution on milling rate ScienceDirect
Prediction of the ball size distribution effect. To validate the values of a and μ found in the previous section, an attempt to predict milling performance on the OEM-BSD was initiated. To do this, 38.80 mm ball was the starting point, i.e. a0 = 0.48 and μ0 = 19.27. With reference to Eqs. (2), (3), (4), (7), the following equation was derivedAbstract. The size of the removed chip area in 3-axis high speed ball end milling is affected by cutting Parameters, and changes throughout the point of contact between the cutter and the workpiece. This change is primarily caused by bending, runout, and vibrations resulting from the cutting forces. A new method has been created to Effect of ball end mills errors on cutting forces SpringerLink
احصل على السعر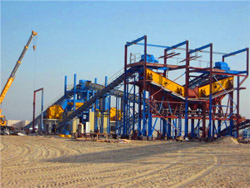
Effect of lifters and mill speed on particle behaviour, torque, and
In this study, the effects of mill speed, lifter height, and lifter number on the particle behaviour, torque, and power of a ball mill are examined by combining DEM simulation and experiment validation. The conclusions based on the observations, calculations, and analysis are as follows: • Mill speed significantly affects particle behaviour.Synthesis of single-phase Ca 3 Co 4 O 9 ceramics and their processing for a microstructure-enhanced thermoelectric performance Study of the effect of milling parameters on mechanosynthesis of Dong H., Wu Q. and . Ye X. 2014 Influence of ball size distribution on grinding effect in horizontal planetary ball millThe design and optimization process of ball mill to reduce
احصل على السعر
Design considerations for large diameter ball mills ScienceDirect
Large mill (D>5.0 m (16.5 ft)) performance has been successfully predicted from small scale batch experiment for grinding kinetics and an RTD correlation for transport using population balance models.The effect of ball size must be properly taken into account in the scale-up. A design method that combined the kinetic scale-up findings and the EFFECTS OF MILL ROTATIONAL SPEED ON THE BATCH depending on feed size and mill speed. The parameters and were constant at 7.3 and 1.17 respectively. Key terms: 2.5 Benchmarking the performance of ball mills .. 30 2.5.1 Single-particle breakageEFFECTS OF MILL ROTATIONAL SPEED ON THE BATCH GRINDING KINETICS OF
احصل على السعر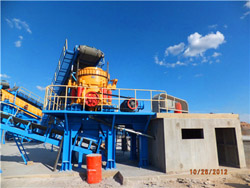
The effect of ball size on mill performance ScienceDirect
Abstract. The specific rates of breakage of particles in a tumbling ball mill are described by the equation Si = axαi ( Q ( z ), where Q ( z) is the probability function which ranges from 1 to 0 as particle size increases. This equation produces a maximum in S, and the particle size of the maximum is related to ball diameter by xm = k1d2.
احصل على السعر- الرمال الهندية
- مطحنة_البنتونيت_للبيع
- small rock grinding machine rock crusher mill
- آلة مطحنة لكشر الذرة
- فحم موبيل كسارة الحجر الجيري
- معدات صهر الرصاص المتنقلة
- double roll crusher made in europe 7c manganese crusher
- کارخانه مس سنگ شکن تایلند
- تامین کنندگان آسیاب چکش دست دوم در آفریقای جنوبی
- شركة اسماعيلية تراكتوز لصيانة المعدات الثقيلة
- Drum Ball Mill For Enrichment
- الصينية بور لو الفك محطم
- نموذج معدات المحاجر
- کوچک قیمت سنگ اندونزی
- boere br 70 2 wide belt sander surplex