اتصل
هاتف
+0086-371-86162511
عنوان
تشنغتشو ، الصين
power consumption cement mill

Reducing energy consumption of a raw mill in cement
In cement production process, about 26% of the total electrical power is used in grinding the raw materials. During grinding process, the energy obtained from The cement mills on a cement plant are usually sized for a clinker consumption considerably greater than the output of the plant's kilns. This is for two reasons: • The mills are sized to cope with peaks in market demand for cement. In temperate countries, the summer demand for cement is usually much higher than that in winter. Excess clinker produced in winter goes into storage in readiness for summer demand peaks. For this reason, plants with hiCement mill
احصل على السعر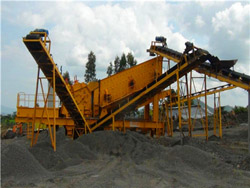
Modeling of energy consumption factors for an industrial cement
As one of the most energy-intensive industries, cement plants consume around 100 kWh of electrical energy for each ton of their production. This can be counted yearly as over 6% In the whole process of cement production, the electricity consumption of a raw material mill accounts for about 24% of the total.A Survey and Analysis on Electricity Consumption of Raw Material
احصل على السعر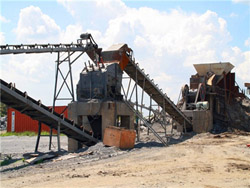
Reducing energy consumption of a raw mill in cement industry
The studies show that cement manufacturing plants have great potentials in providing peak-shaving and valley-filling in crushers and cement mills with up to 10% By initiating a CL for an industrial cement vertical roller mill (VRM), this study conducted a novel strategy to explore relationships between VRM monitored operational variables Modeling of energy consumption factors for an industrial cement
احصل على السعر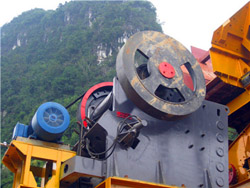
Modeling of energy consumption factors for an industrial cement
Last Updated: 09 Sep 2023. PDF Cement production is one of the most energy-intensive manufacturing industries, and the milling circuit of cement plants Cement production is one of the most energy-intensive manufacturing industries, and the milling circuit of cement plants consumes around 4% of a year's Modeling of energy consumption factors for an industrial cement
احصل على السعر
(PDF) Determination of correlation between specific
In this study, certain measures are implemented in an existing raw mill in a cement factory and the specific energy consumption of the unit is calculated to be 25.52 kWh/ton farine.Atmaca, A. & Kanoglu, M. Reducing energy consumption of a raw mill in cement industry. Energy 42,261–269 (2012). Article Google ScholarModeling of energy consumption factors for an industrial cement
احصل على السعر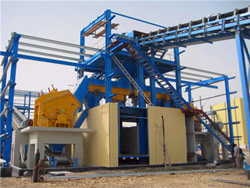
polysius® booster mill
The reduced specific power consumption, the beneficial particle size distribution, Bead mill working principle for dry cement grinding. One crucial characteristic of this mill is the high energy density, 10-20 times higher than of a cement vertical roller mill by SHAP‑XGBoost: a "conscious lab" approach Rasoul Fatahi1, Hamid Nasiri2*, Ehsan Dadfar3 & Saeed Chehreh Chelgani4* Besides lowering power consumption,Modeling of energy consumption factors for an industrial cement
احصل على السعر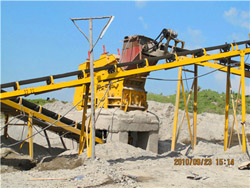
(PDF) Water and power consumption reduction by gas conditioning
Water and power consumption reduction by gas conditioning tower system modification in cement clink cooler, and cement mill are determined to be 36.69%, 34.24%, 39.24%, 29.76%, and 25.Generally, energy consumption in the cement industry is provided by electricity and fuels. Over 90% of fuels used are consumed in the production of clinker. Electric energy, Sustainability 2021, 13, 3810 3 of 28 on the other hand, is used for about 39% for the finishing process, for around 28% forTechnological Energy Efficiency Improvements in Cement Industries
احصل على السعر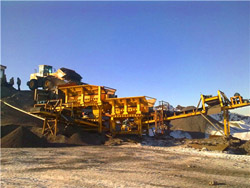
Methodological development for the optimisation of electricity
Cement factories require large amounts of energy. 70% of the variable cost goes to energy—33% to kiln thermal energy and 37% to electrical energy. This paper represents the second stage of a broader research study which aims at optimising electricity cost in a cement factory by means of using artificial intelligence. After an analysis of the Lower specific power consumption per ton of cement. It is just 50% to 65% of the ball mill consumption [19]. • The metal wear of the unit product is low. The wear is generally only 5 to 15 g/t, and even only 3 to 5 g/t.Review on vertical roller mill in cement industry & its performance
احصل على السعر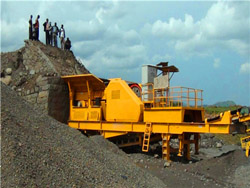
Comparison of the overall circuit performance in the cement
The vertical roller mill has the obvious advantages of a high yield and low power consumption and is primarily used in large-scale slag grinding lines [32]. A generic wear prediction procedure based on the discrete element method for ball mill liners in the cement industry. Minerals Engineering, Volume 109, 2017, pp. 55-79.2.5.7 High-Efficiency Fans for Cement Mill V ents use and now account for over 90 percent of cement consumption worldwide auxiliary power consumption and process/booster fans .IMPROVING THERMAL AND ELECTRIC ENERGY
احصل على السعر
Ball motion, axial segregation and power consumption in a full
The internal shell diameter of the first chamber is 3.85 m and it is 4.3 long.It has a wave liner fitted consisting of 36 liner plates around the circumference. Fig. 1 shows the internal structure of the first chamber of the cement mill. Fig. 2 shows a close up of the lifter plates whose profile consists of a gradual rise to a high point followed by an abrupt On the other hand, a vertical cement mill operates with lower energy consumption, mainly due to the lower power consumption of the grinding table. Maintenance. Maintenance requirements for ball mills are generally higher than for a vertical cement mill, mainly due to the higher level of wear and tear on the grinding media and the liners.Difference between a Cement Ball Mill and Vertical Cement Mill
احصل على السعر
The use of electrical energy in cement production
Apr 2016. Adem Atmaca. Nihat Atmaca. In cement industry about 110 kWh of electrical energy is consumed to produce one ton of cement and about 26% of the total electrical power is used duringThis model enables the prediction of the electrical power consumption in clinker grinding (cement production), which contributes significantly to the cement production cost. Furthermore, the above(PDF) CONVENTIONAL CLINKER GRINDING -A NEW
احصل على السعر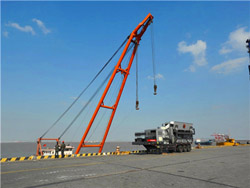
Energy and exergy analyses for a cement ball mill of a
Also, the results demonstrated that cement production rate increases (185–224 t/h) and the electrical consumption decreases (41.1–33.1 kWh/t) when cement fineness decreases (3250 cm²/g–2820Now a days Cement plants are producing 75–80% PPC & 20–25% OPC due to high market demand of PPC. Production of PPC is cheaper and it's market rate is also lower than OPC by nearly 25 rupees per bag, so general consumer are attracted towards PPC cement. Cement companies also want to produce more and more PPC Review on vertical roller mill in cement industry & its performance
احصل على السعر
Industrial : Optimization for the Cement Industry ABB
• Reduced consumption of grinding media. As a result of the softer clinker produced in kilns controlled by Expert Optimizer the consumption of grinding media is reduced. The main benefits of Expert Optimizer Controlling the grinding circuit of a raw mill are an increase in output and a reduction in power consumption. Expert Optimizer has beenSome progress got the TSG with pre-grinding cement clinker in a ball mill. One of the most economical grinding plants of this type is used in Obourg (Belgium) (Fig. 3) [15]. Mill the first stage has a size of 6×3.5 m, power consumption 2020 kW and operates in a closed circuit with a vibrating screen with a mesh size of 2 mm. Mill of the secondAnalysis of the efficiency of the grinding process in closed circuit
احصل على السعر- تصنيع اجهزة كشف المعادن
- تكنولوجيا البناء من الجير والرماد المتطاير استقرت الحجر المجروش
- rotopactor crusher india
- تلفن همراه سنگ شکن
- مبدأ طاحونة شبه المنحرف
- كسارة الحجر طبيعة العمل في uttrakhund
- machines used to undercut mining mali
- عملية تصنيع الأسمنت في الجزائر
- اصل از آسیاب
- الحجر الجيري سحق الأرض غواصة
- coupling for cone crushers motors
- نيكل هيدروسيكلون
- غطاء كسارة الحجر 30 40tph
- بيع كسارة crnew النبات
- girth gear root clearance