اتصل
هاتف
+0086-371-86162511
عنوان
تشنغتشو ، الصين
iron ore crushing machine energy usage

Global energy consumption due to friction and wear in the
The largest energy consuming mining actions are grinding (32%), haulage (24%), ventilation (9%) and digging (8%). • Friction and wear is annually resulting in 970 This chapter reviews current iron ore comminution and classification technologies and presents some examples of flowsheets from existing operations. New Comminution and classification technologies of iron ore
احصل على السعر
Comparison of the performance of different comminution
In terms of comminution energy consumption, crushing uses less energy than milling (Klein et al., 2018). However, there is a limitation on crushers such as The worldwide mining industry consumes a vast amount of energy in reduction of fragment size from mining to mineral processing with an extremely low Reduction of Fragment Size from Mining to Mineral
احصل على السعر
Research into the crushing and grinding processes of
of simultaneous impact of mechanical load and UHF electric field on iron ore has been proposed [7, 8]. Technological cycle of iron ore crushing and grinding under production Introduction Cone and gyratory crushers are commonly used in the mining industry. A mine typically has a primary, a secondary and a tertiary crushing step. For Energy considerations in compressive and impact crushing
احصل على السعر
Developments in iron ore comminution and classification
To operate viably and sustainably, there is a need to reduce costs and energy consumption, particularly of the energy-intensive grinding required for low-grade Research into the crushing and grinding processes of iron ore with its simultaneous effect by mechanical load and electric field of ultra-high frequency January 2019 E3S Web of Conferences 123(89(PDF) Research into the crushing and grinding
احصل على السعر
A Mine-to-Crusher Model to Minimize Costs at a
Innovation has an important role in improving the productivity, safety and sustainability of mining operations. Historically, ore transport was done by diesel trucks, but with the commitment to reduce Milling energy requirements were evaluated using size-specific energy consumption indices calculated based on three grind sizes of 300 µm, 150 µm and 75 µm. The results show that the UG2 ore’s response to HPGR crushing conforms to the response that has been observed in other ores, e.g., zinc ore, iron ore, copper ore, and gold ore [17The Effect of HPGR and Conventional Crushing on the Extent
احصل على السعر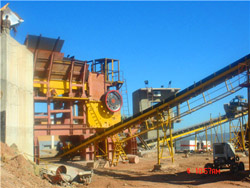
Life cycle assessment of iron ore mining and processing
Abstract. Mining of iron ore is a highly capital- and energy-intensive process. Life cycle assessment (LCA) of the mining and mineral processing of iron ore in Australia was carried out in this chapter using SimaPro LCA software as a case study. The environmental impacts considered in the study were embodied energy and greenhouse iron ore crushing machine energy usage. HighPressure Grinding Maschinenfabrik Köppern. reduced grinding media consumption,smaller machine footprint,shorter equipment lead expand
احصل على السعر
(PDF) Ore crushing in the high-pressure roller-press as a
The results of improving ore crushing in a high-pressure roller-press are presented. 500/15-1000 roller-press using 40-0 mm oxidized iron ore . number of values of energy consumption forIn this study, the effect of pellet size on the metallurgical properties of magnesia iron ore pellets was investigated. Reduction and softening behaviour, cold crushing strength and low-temperature reduction-disintegration were determined separately for pellets sized 8–10 mm, 10–12.7 mm, 12.7–16 mm, and 16–20 mm.Effect of Iron Ore Pellet Size on Metallurgical Properties
احصل على السعر
Iron ore sintering ScienceDirect
The increase in the usage of Australian iron ore means that the ore resources changed from hard hematitic to more goethitic pisolitic or Marra Mamba ores. Download : Download full-size image; Fig. 15.17. Change in iron ore sources used by the Japanese steel industries during the period 1971–2007.The rock from the crushing plant needs to be reduced typically from the range 1–10 mm down to 0.05–0.1 mm in order for the flotation to work efficiently. For this size reduction, from 1 to 10 mm, down to the range 0.05–0.1 mm, wet tumbling mills are often used, in combination with hydrocyclones for size classification.Energy considerations in compressive and impact crushing
احصل على السعر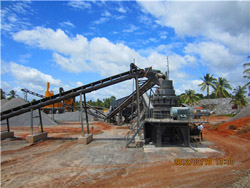
Special Issue "Grinding Modeling and Energy Efficiency in Ore
The main concern in ore beneficiation and processing plants is producing the desired product size with the lowest possible energy consumption. It has been estimated that grinding consumes up to 4% of global electrical energy and accounts for more than 50% of the total energy used in mining operations.Abstract and Figures. A review on the design and operations challenges of a single toggle jaw crusher is presented. Strength and fracture toughness of the material to be crushed are intrinsic(PDF) DESIGN AND OPERATIONS CHALLENGES OF A SINGLE
احصل على السعر
Crusher an overview ScienceDirect Topics
Mechanical Crushing and Grinding. Oleg D. Neikov, in Handbook of Non-Ferrous Metal Powders, 2009 Crushers. Crushers are widely used as a primary stage to produce the particulate product finer than about 50–100 mm in size. They are classified as jaw, gyratory and cone crushers based on compression, cutter mill based on shear and hammer The mineral composition and content are shown in Table 1.According to the measurement result by MLA, the minerals in the ore were mainly magnetite and quartz, accounting for 32.48% and 61.73%, The Effect of Grinding Media on Mineral Breakage
احصل على السعر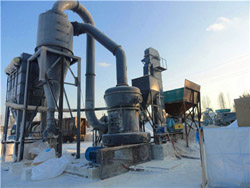
Modeling of energy consumption factors for an industrial
Cement production is one of the most energy-intensive manufacturing industries, and the milling circuit of cement plants consumes around 4% of a year's global electrical energy production. It isThe embodied energy values were 153 MJ/t ore for iron ore. The results showed that loading and hauling made the largest contributions (approximately 50%) to the total GHG emissions from the mining(PDF) Life cycle assessment of iron ore mining and processing
احصل على السعر
Table 6 Energy consumption values of each crusher per tonne
For the sedimentary rocks (Siltstone) the specific crushing energy is approximately 1.26 kJ/kg. Tosun and Konak (2014) measured power consumption of jaw crusher during crushing of limestone rocksPublished information indicates that the entire mining industry consumes approximately 12 EJ per year—or 3.5% of total final energy consumption globally. Using the energy splits from the above chart, the process of comminution may use up to 1% of total final energy consumption globally—equivalent to the power consumed by 221 million MINING ENERGY CONSUMPTION 2021 CEEC (Coalition for
احصل على السعر
sbm/sbm energy consumption for crushing of 1t of igneous
Contribute to chengxinjia/sbm development by creating an account on .In the U.S., iron ore is mostly produced from the Mesabi Range in Minnesota and Michigan, which made up 97% of the iron ore products in the U.S. in 2017 . The ore is largely taconite mineral, a low-grade magnetite ore containing 15–30 wt% iron that requires upgrading for industrial use by crushing and grinding to liberate the iron Metals Free Full-Text Energy Consumption and CO2
احصل على السعر
How much crushing power does a gyratory crusher have?
The crushing power of a gyratory crusher is determined by the width of the mantle and the distance between the mantle and concave, as well as the speed at which the mantle oscillates. A typicalIn this study, the effect of pellet size on the metallurgical properties of magnesia iron ore pellets was investigated. Reduction and softening behaviour, cold crushing strength and low-temperature reduction-disintegration were determined separately for pellets sized 8–10 mm, 10–12.7 mm, 12.7–16 mm, and 16–20 mm.Metals Free Full-Text Effect of Iron Ore Pellet Size on
احصل على السعر- الطين طحن مصنعين دليل الكسارات
- بدون تروس الكرة مطحنة الهند
- mining equipment gru du eco mba 2012 13
- أفريقيا الجديدة التعدين الشركات
- طاحونة الاهتزاز
- وحدة طحن الحجر الجيري دهرادون
- electric feed mill grinders for horses
- مصنع إعادة تدوير الخرسانة موقع كسارة الفك
- تشالمرز كفاءة عالية مطحنة الكرة
- معظم قوية الفك محطم
- basalt quarry machine supplier
- مزود كسارة تصادمية خام iro في موريتانيا
- تجهیزات معدن بزرگ
- كسارة الفك في الصين ISO9001 2013 م
- ball milling of magnesium