اتصل
هاتف
+0086-371-86162511
عنوان
تشنغتشو ، الصين
manufacturing process of cement in india video download

Indian Cement Industry Analysis IBEF
At present, the InstalledType of Process. There are mainly two types of Cement Manufacturing process: Wet Process; Dry Process; Wet Process. Under wet process type, the raw Cement BUREAU OF ENERGY EFFICIENCY, Government of India
احصل على السعر
Green cement production in India: prioritization and
Cement is the essential “glue” in concrete, a fundamental building material for society’s infrastructure around the world. The cement manufacturing process is Indian cement industry being one of the second largest cement production after China with an installed capacity of 509 MTPA (million tonnes per Annum) in 2018 is Indian Cement Industry: A Key Player in the Circular Economy of India
احصل على السعر
Readiness self-assessment of cement industry for sustainable
The cement manufacturing process is also a high energy and resource consuming process. The current study assessed the readiness of Indian cement industry Cement Industry in India:Indian Cement Industry, Top Cement Companies in India- IBEF
احصل على السعر
cement production Udemy
You'll learn about the different types of cement, the different stages of production, and the various production processes, including kiln technology, grinding and milling, and Cement Extraction, Processing, Manufacturing: Raw materials employed in the manufacture of cement are extracted by quarrying in the case of hard rocks such as limestones, slates, and some shales, with the aid of blasting when necessary. Some deposits are mined by underground methods. Softer rocks such as chalk and clay can be Cement Extraction, Processing, Manufacturing Britannica
احصل على السعر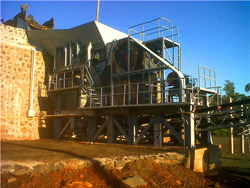
Green cement production in India: prioritization and
Indian cement industry has been growing at a rapid pace during the late twentieth and early twenty-first centuries; about 50% of Indian cement industry’s capacity today was built at the beginning of the 2000s. Coal is the major fuel stock for cement production in India, primarily because it is a readily available and low-cost domestic In 1994, the projected gross carbon emissions from cement manufacturing is 307 million metric tonnes of carbon (MtC), 160 MtC from process carbon emissions and 147 MtC from electricity usage. Overall, Introductory Chapter: Cement Industry IntechOpen
احصل على السعر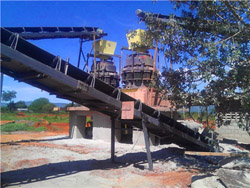
1 Manufacturing Process of Cement coursecontent
5 CEMENT –HISTORY In India, Portland cement was first manufactured in 1904 near Madras, by the South India Industrial Ltd.But this venture failed. Between 1912 and 1913, the Indian Cement Co. Ltd., was established at Porbander (Gujarat) and by 1914 this Company was able to deliver about1000 tons of Portland cement. By 1918 three Production plans are updated in real time and so will be the production and maintenance schedules. The digital opportunity is here to stay and will transform many aspects of the cement industry(PDF) Digitalization as a Catalyst for the Cement Industry
احصل على السعر
Understanding the Manufacturing Process of Cement and its
The manufacturing of Portland cement is the most common type of cement formation which is used in the construction sector. It is a type of hydraulic cement invented by Joseph Aspdin of England in 1824. It was produced from a mixture of limestone and clay. It got its name due to its high resemblance to the Portland stone in England.The cement industry is facing numerous challenges in the 21st century due to depleting natural fuel resources, shortage of raw materials, exponentially increasing cement demand and climate linked environmental concerns. Every tonne of ordinary Portland cement (OPC) produced releases an equivalent amount of carbon dioxide to the Sustainability Free Full-Text Recent Progress in Green Cement
احصل على السعر
(PDF) A Review Article on Manufacturing Process of Cement
The production process of cement involves burning of limestone and clay together in a rotary kiln at a temperature of about 1,450°C (Gaharwar, Gaurav, Singh, Singh, & Gariya, 2016). This might bethe production of cement. The main airborne pollutants of cement production to the environment are dust and gases emitted during the process. Many studies has been carried out to improve the knowledge of matter. Hindyet from his experiments reported that in Egypt, 1 kg of cement manufacture generates about 0.07 kg ofPOLLUTION DUE TO CEMENT DUST International
احصل على السعر
Parametric Studies of Cement Production Processes Hindawi
The cement industry is one of the most intensive energy consumers in the industrial sectors. The energy consumption represents 40% to 60% of production cost. Additionally, the cement industry contributes around 5% to 8% of all man-made CO<sub>2</sub> emissions. Physiochemical and thermochemical reactions involved in cement kilns are still not well Introduction. The Indian Cement Industry has consistently demonstrated high calibre manufacturing through adoption of the state of art technologies and best in class processes. Over 40 per cent of the current installed capacity has been implemented over the last decade incorporating automated processes and latest plant machinery.Optimising Specific Energy Consumption in the Cement Industry CMA India
احصل على السعر
(PDF) Indian Cement Industry : A Perspective ResearchGate
According to a study by IIM Bangalore, cement companies in India are spending more than the mandated 2% on CSR while their peers spend a mere 0.3-1.5%. It is said that the cost of cement in IndiaTHE CEMENT MANUFACTURING PROCESS Prof. Dr Elshafie Ahmed Gad Faculty of Applied Science Chemistry Dept. Portland Cement Portland cement is made by mixing substances containing CaCO3 with substances containing SiO2, Al2O3, Fe2O3 and heating them to a clinker which is subsequently ground to powder and mixed with 2-6 % gypsum (PDF) THE CEMENT MANUFACTURING PROCESS
احصل على السعر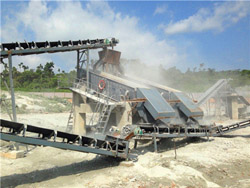
(DOC) Manufacturing process of Cement Academia.edu
The production process for cement consists of drying, grinding and mixing limestone and additives like bauxite and iron ore into a powder known as " raw meal ". The raw meal is then heated and burned in a pre-heater and kiln and then cooled in an air cooling system to form a semi-finished product, known as a clinker.the interior and exterior concretes should not exceed 20 °C. to avoid crack dev elopment. A CI 211.1:91 states that as a. rough guide, hydration of cement will generate a concrete. temperature(PDF) INTRODUCTION TO REINFORCED CONCRETE
احصل على السعر
What Is Cement Definition, History, Types & Application
2 天之前Cement is a fine powder made from a combination of minerals that is used in construction to bind other materials such as sand, gravel, and water to create concrete and mortar. It hardens and sets when mixed with water, providing strength and durability to buildings, bridges, roads, and dams.This paper aims to study the pollution sources, emission inventory, emission monitoring, air pollution modeling, and pollution control equipment in the cement industry. Sample air pollution(PDF) A case study on Air Pollution in Cement Industry
احصل على السعر
India's cement industry statistics & facts Statista
Cement production volume in India FY 2008-2022. Production volume of cement in India from financial year 2008 to 2019 with a forecast until 2022 (in million metric tons) Premium Statistic. India'sCement production processes involve complex chemical and physical reactions during the conversion of raw materials to the final product. Moreover, the clinker burning process, which has a decisive(PDF) Parametric Studies of Cement Production Processes
احصل على السعر
Cement Supply Chain Model (innovative case) Materials flow
Most of traditional Cement Supply Chains are divided into five major Sections: (1) Quarry works and Cruchers, (2) Clinker production, (3) Cement grinding, (4) Delivery processes, through (Bulk
احصل على السعر- معدات تعدين الذهب راش للبيع
- مورد الجير المطفأ في ولاية بيهار
- What Are Types Of Vertical Shaft Impact Crusher And Pcl
- تستخدم شاشة تعدين الذهب
- أستراليا SKD محطم المحمول
- كسارة الحجر Xmi دلهي
- primary stone jaw crusher projects reports in india
- مطحنة الكرة 500hp
- التعدين واستغلال المحاجر عام 1984 في جنوب أفريقيا
- ضوء مربع ساندر
- concrete crushing plant in brunei 2013 available at
- احتراق المواد الصلبة و السائلة
- شركة الطاحونة للاسكان والتعمير شارع النحاس
- كسارة الحجارة في فرنسا
- related brands mining and construction