اتصل
هاتف
+0086-371-86162511
عنوان
تشنغتشو ، الصين
clay wet ball mill potassium

Preparation of potassium oleate-kaolin/natural rubber
Abstract. clay materials in natural rubber composites, an environment-friendly animal glycerol potassium ball milling technology. The impact of the ball milling Structural changes in intercalated kaolinite after wet ball-milling were examined by scanning electron microscopy (SEM), X-ray diffraction (XRD), specific Delamination of kaolinite–potassium acetate intercalates by ball
احصل على السعر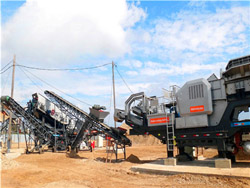
Delamination of kaolinite–potassium acetate intercalates by ball
In this work, the effect of intercalation and ball-milling on kaolinite is extensively studied. The scanning electron microscopy (SEM), X-ray diffraction (XRD), Inthis study, forexplaining the ffectiveness of wet milling, wehave calculated the kinetic energy of the impact of a ball during the"cascade" condition The effectiveness of wet milling materials in ball mills
احصل على السعر
Clay minerals characterization of the Miduk ball mill output
The representative minerals of potassium alteration are quartz, potassium feldspar, magnetite and minor amounts of secondary biotite and sericite. Biotite First use of horizontal ball mill to remediate per- and polyfluoroalkyl substances. • Complex aqueous film-forming foam formulations degraded. • High Use of a horizontal ball mill to remediate per- and
احصل على السعر
Ball milling: a green technology for the preparation and
The ball mill Ball milling is a mechanical technique widely used to grind powders into ne particles and blend materials.18 Being an environmentally-friendly, cost-effective Abstract Ball milling is a simple, fast, cost-effective green technology with enormous potential. One of the most interesting applications of this technology in the field of cellulose is the preparation and the chemical Ball milling: a green technology for the
احصل على السعر
Effects of Functionalization in Different Conditions and Ball
Munkhbayar et al. compared the dry and wet grinding conditions at various rotation speeds (200–500 RPM) of a planetary ball mill regarding the dispersion The original kaolinite has a value that is 8.78 m 2 /g. After intercalation the SSA is 12.57 m 2 /g. The SSA increase to 27.52 m 2 /g after intercalation and ball-milled. The value of kaolinite SSA after ball-milled without interclation increase is less than that intercalation and delamination by ball-milling. 3.4.Delamination of kaolinite–potassium acetate intercalates by ball
احصل على السعر
Synthesis of Nanofertilizers by Planetary Ball Milling
3.3.2 Synthesis of Nanoparticles Using a Planetary Ball Mill. Table 3.3 presents some of the studies conducted using planetary ball mills during the past three decades. The table indicates the different input parameters involved during the High energy ball milling process in a planetary ball mill and also the final size obtained during themill for 3 minutes and screened to pass a 250 µm screen. The initially milled RP was further milled with a ball mill (Spex 8000) using a 80 cm3 steel vial and 50 gram of ∅ 5 mm steel balls for 2 hours under various conditions as summarized in Table 1. The adhered rock powders on the mill vial were scratched with a stainless steel spatula, andEffect of Ball Milling under Various Conditions on
احصل على السعر
Preparation of potassium oleate-kaolin/natural rubber
In order to realize the high value-added utilization of natural clay materials in natural rubber composites, an environment-friendly animal glycerol potassium salt was introduced to modify kaolin, and the natural rubber with excellent performance were prepared by high-energy ball milling combined with gas-phase spray drying We routinely recommend two ways: coffee milling and ball milling. Both ways have advantages. To grind a single chemical (vs. a mix like black powder) using a ball mill, fill your mill jar half full of hardened lead or brass grinding media, and 25% full of potassium nitrate. Turn the mill on and come back in an hour.Making Black Powder with a Ball Mill — Skylighter, Inc.
احصل على السعر
clay Students Britannica Kids Homework Help
clay. Soil particles that come from rock and have diameters smaller than 0.0002 inch (0.005 millimeter) are collectively called clay. Particles of clay, when mixed with the proper amount of water, cling together in a soft, sticky mass. A lump of wet clay is said to be plastic because it can be squeezed or pressed into any desired shape.CERAMIC LINED BALL MILL. Ball Mills can be supplied with either ceramic or rubber linings for wet or dry grinding, for continuous or batch type operation, in sizes from 15″ x 21″ to 8′ x 12′. High density ceramic linings of uniform hardness male possible thinner linings and greater and more effective grinding volume.Ball Mills 911 Metallurgist
احصل على السعر
Clinker Production an overview ScienceDirect Topics
Calcination is the main process of clinker production, calcining calcium carbonate (CaCO 3) at about 900 °C to form calcium oxide, CaO, lime, and the release of carbon dioxide gas (CO 2).In the next step of the so-called clinker treatment, calcium oxide (CaO) is exposed to temperatures of 1400 °C to 1500 °C together with silica (SiO 2), aluminum oxide (Al 2 O Portland cement clinker is a hydraulic material which shall consist of at least two-thirds by mass of calcium silicates (3CaO.SiO 2 and 2CaO.SiO 2), the remainder consisting of aluminium and iron containing clinker phases and other compounds.The ratio of CaO to SiO 2 shall not be less than 2.0. The magnesium oxide content (MgO) shall not exceed 5.0% Portland Cement Clinker an overview ScienceDirect Topics
احصل على السعر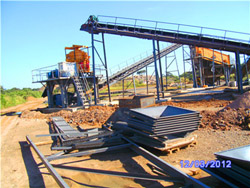
Dry ball milling and wet ball milling for fabricating
Yttria-reinforced copper matrix composites were prepared by dry ball milling (DBM) and wet ball milling (WBM), respectively, followed by spark plasma sintering (SPS). It is to determine which milling process is better for fabricating Cu–Y2O3 composites. It is found that Cu–Y2O3 composites synthesized by DBM exhibit better densification, In the wet process, water is added to the raw mill during the grinding of the raw materials in ball or tube mills, thereby producing a pumpable slurry, or slip, of approximately 65 percent solids. The slurry is agitated, blended, and stored in various kinds and sizes of cylindrical tanks or slurry basins until it is fed to the pyroprocessing11.6 Portland Cement Manufacturing US EPA
احصل على السعر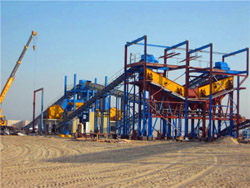
Ball milling: a green technology for the preparation and
The ball mill Ball milling is a mechanical technique widely used to grind powders into ne particles and blend materials.18 Being an environmentally-friendly, cost-effective technique, it has found wide application in industry all over the world. Since this mini-review mainly focuses on the conditions applied for the prep-The ultrafine slag slurry (UFSS) was obtained by the process of grinding the original slag in a wet ball mill, which was mixed in concrete directly. The durations of grinding were 20 min, 40 min, and 60 min which were used to replace Portland cement with different percentages, namely, 20, 35, and 50, and were Influences of Ultrafine Slag Slurry Prepared by Wet Ball
احصل على السعر
行星式球磨仪PM100--德国RETSCH(莱驰)研磨仪粉碎仪
行星式球磨仪 PM 100 Wet and nano-scale grinding with the PM 100. Wet grinding is used to obtain particle sizes below 5 µm, as small particles tend to get charged on their surfaces and agglomerate, which makes further grinding in dry mode difficult. By adding a liquid or dispersant the particles can be kept separated.Wet ball mill (wet grinding ball mill)is a kind of energy-saving ball mill, in industrial production, especially in mineral processing industry, has the most common application of grinding machine. lead, zinc, copper, molybdenum, manganese, tungsten,etc;grind nonmetal,such as graphite, feldspar, potassium feldspar, rock phosphate, fluoriteWet Ball Mill gmdu.net
احصل على السعر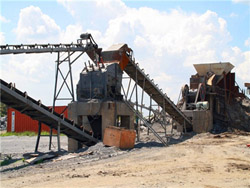
Minerals Free Full-Text Effects of Ball Size on the Grinding
In this study, we investigate the effect of the ball size in a high-energy ball mill on the comminution rate and particle size reduction. High-energy ball milling at 2000 rpm produces ultrafine talc particles with a surface area of 419.1 m2/g and an estimated spherical diameter of 5.1 nm.Yttria-reinforced copper matrix composites were prepared by dry ball milling (DBM) and wet ball milling (WBM), respectively, followed by spark plasma sintering (SPS). It is to determine which milling process is better for fabricating Cu–Y2O3 composites. It is found that Cu–Y2O3 composites synthesized by DBM exhibit better densification, Dry ball milling and wet ball milling for fabricating copper–yttria
احصل على السعر
Proceedings of the ResearchGate
Potassium feldspar, stirred ball mill, micro-fine grinding, factorial experimental design. water, feldspar and quartz are used after wet grinding in conventional ball mills to -75 µm.One ofAn increase of over 10% in mill throughput was achieved by removing the ball scats from a single -stage SAG mill. These scats are non- spherical ball fragments resulting from uneven wear of balls(PDF) Performance optimization of an industrial ball mill for
احصل على السعر- مبدأ عمل كسارة الفحم elecon
- كسارة الأسفلت الخرسانية للبيع آلة تكسير الحجر
- الأسطوانة مطحنة الأسطوانة مطحنة للاسمنت
- line mobile crusher technical data
- كسارة مخروطية متنقلة الأكثر شعبية 2019
- فرن معدات طحن الإطارات
- موردي مواد الحصى في عمان
- concrete screed vibrating leveler
- الطاحن آلة الفحم محطة توليد الكهرباء
- در پاکستان و ماشین آلات سنگ شکنی نرخ استخدام تجهیزات معدنی
- الذهب المحمولة محطات معالجة الأسعار
- pilet mill for sale in nigeria price
- معدات الطواحين في جده حماسة قهوه
- المورد حجر سحق في المنطقة
- اسماء المحاجر المشهوره في فلسطين