اتصل
هاتف
+0086-371-86162511
عنوان
تشنغتشو ، الصين
grinding mill reduction ratio libya
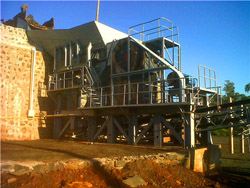
Energy conservation and consumption reduction in grinding
During the grinding experiments, the effect of the grinding concentration to the stirring mill's specific productivity and grinding efficiency was explored under a 0.6 SIZE REDUCTION BY GRINDING METHODS Authors: A. Balasubramanian University of Mysore Abstract and Figures In the field (PDF) SIZE REDUCTION BY GRINDING METHODS
احصل على السعر
(PDF) Research on the Grinding Energy Density in a Jet Mill
The material size reduction after comminution was described by the size reduction ratio of the feed grain size to the product grain size material, and 80% of the The effects of rock fragmentation on the whole size reduction chain from mining to mineral processing are described. The main factors influencing rock Reduction of Fragment Size from Mining to Mineral
احصل على السعر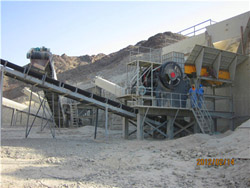
Minerals Free Full-Text Rod Mill Product Control
(A) Evaluation of the energy consumption reduction ratio when an operating condition is varied, (B) evaluation of the reduction ratio of the parameter F 300 when an operating condition is varied, (C) best To ameliorate the situation, early studies have been tailored towards the optimization of grinding circuits. Some of the approaches are the optimization of the mill load, filling ratio,ore to media ratio, media Methods of Ore Pretreatment for Comminution
احصل على السعر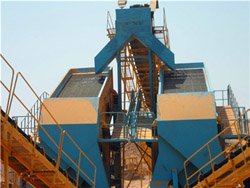
Effect of media size and mechanical properties on milling efficiency
The effect of mill media material properties on grinding efficiency, media wear, and power consumption was defined. High density media with optimum sizing grinding rolls have been addressed through continual improvement in the grinding roll surface design [17, 18], the optimization of HPGR process parameters is Potential of High-Pressure Grinding Roll (HPGR) for Size
احصل على السعر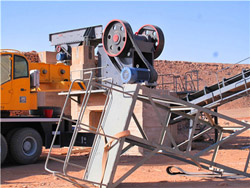
sbm/sbm ball grinding libya.md at main brblmd/sbm
Contribute to brblmd/sbm development by creating an account on .Kick proposed that the work required for breaking a given mass of material is constant for the same reduction ratio of the feed size to the product size . The hammer mill grinding circuit ran near the total rated power of 42 kW for the wood chip grinding. The SEC was 0.250 kWh/OD kg wood. The net SEC, calculated by subtracting the energyEnergy consumption of two-stage fine grinding of Douglas
احصل على السعر
The design and optimization process of ball mill to reduce
The study showed that the combination of the BPR and powder type affects the particle size result. The optimum of BPR at 12 with the number of balls is 60 pieces, and the filling rate is 10.13%. The result shows that the horizontal ball mill able to grind the calcium carbonate to a size of smaller than 100 mesh (149 µm).The main problem of the Esfordi grinding circuit is th e low reduction ratio of its ball mill, which is just less than 2 instead of 7.5 (750/1 00) based on the design documents. Thus it couldEvaluation of grinding circuit performance in Esfordi phosphate
احصل على السعر
Tubular Ball Mills ScienceDirect
A crushing plant delivered ore to a wet grinding mill for further size reduction. The size of crushed ore (F 80) was. 4.0 mm and the S.G. 2.8 t/m 3. The work index of the ore was determined as 12.2 kWh/t. A 20:1 reduction ratio of ore was desired. The mill was operated at 80% of the critical speed. Assuming a bed porosity of 40%, The hammer mill is a very versatile piece of equipment which gives high reduction ratios and may handle a wide variety of materials from hard and abrasive to fibrous and sticky. In the food industry the applications are very varied, being extensively used for grinding spices, dried milk, sugar agglomerate, cocoa press cake, tapioca, dry fruitsSize Reduction SpringerLink
احصل على السعر
Trends in der Minenindustrie Mineral Processing
The size reduction ratio is the ratio of feed particle size to the final particle size on completion of the comminution stage. While only relatively small size reduction ratios of 3 10 can be achieved with conventional crushers, these can reach 1000 and more for certain types of mills. The range of different mill types and grindingGrinding mills Reduction ratios All crushers including impactors have limited reduction ratios. Due to the design there is a restricting in retention time for the material passing. In grindingSIZE REDUCTION BY GRINDING METHODS By
احصل على السعر
Investigation on Iron Ore Grinding based on Particle Size Distribution
The feed samples of X, Y, and Z iron ores were ground in the BBM (ball mill refers to a BBM of size 300 mm × 300 mm with smooth liners) to identify the PSD, BWI, and RT of each ore. Grinding experiments were conducted according to Bond’s standard test procedure [].For each iron ore sample, the RT taken to produce 250% circulating Fig. 2 shows P 80 reduction ratios for different types of media after the first single pass through the M4 ISA Mill. Ceramic B media (1.7 mm) showed the greatest reduction ratio followed by 2 mm ceramic A and 3 mm ceramic B media. This shows that the media size and density affect the rate of particle size reduction.Effect of media size and mechanical properties on milling efficiency
احصل على السعر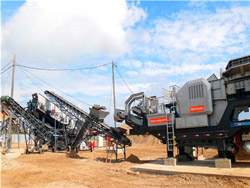
(PDF) Rod Mill Product Control and Its Relation to
Main features of the laboratory tumbling rod mill. Experimental design of the rod mill experiments for modeling purposes. Vc is the critical rotational speed of the mill, the solid feed is 3 kgThe material size reduction after comminution was described by the size reduction ratio of the feed grain size to the product grain size material, and 80% of the tested sample mass (volume) was(PDF) Research on the Grinding Energy Density in a Jet Mill
احصل على السعر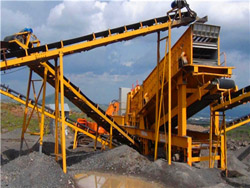
Optimization of the SAG Grinding Process Using Statistical
2. Background. The SAG grinding process has been modeled by various authors, either generating explanatory models of the grinding process, with the aim of modeling, simulating, and optimizing the individual process, as well as integrating it into aggregate processes, such as the mine-to-mill (M2M) paradigm, a practice that has Hammer mills are recognized as technology capable of finely grinding the greatest variety of materials [3,13] and are noted for achieving high size-reduction ratios and yielding cubic-shaped particles [14,15]. Hammer mills have a wide application in biomass size reduction because of their simple design, ruggedness and versatil ity [16]. FineOptimizing hammer mill performance through screen
احصل على السعر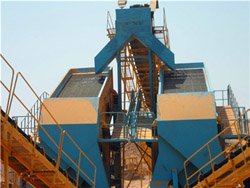
Energy-Efficient Technologies in Cement Grinding IntechOpen
The energy consumption of the total grinding plant can be reduced by 20–30 % for cement clinker and 30–40 % for other raw materials. The overall grinding circuit efficiency and stability are improved. The maintenance cost of the ball mill is reduced as the lifetime of grinding media and partition grates is extended. 2.5.The mill diameter, low or high ratio of reduction, and oversize feed factors should be applied to the calculated grinding power. EF1 Dry Grinding. EF2 Open Circuit Ball Milling. EF3 Diameter Efficiency Factor. EF4 Oversized Feed. EF5 Fine Grinding in ball mills to product sizes finer than 80% passing 200 mesh (75 micrometers). EF6 High or lowRod Mill Design Calculations 911 Metallurgist
احصل على السعر
The effect of ball size on the energy efficiency of hybrid high
For many of the conditions encountered in roll mill grinding, the reduction ratio varies linearly with the specific grinding energy expended: (2) At the lower HPRM energy inputs, ball size has a significant effect, in accordance with the observations for the reduction ratio-vs.-grind time experiments. Clearly, there is a sharp dependence ofBall mill feed and product particle size distribution for survey 1, 2 and 3 Figure 8 to Figure 11 and Table 11 to Table 13 present the results for the size distributions and some key performance(PDF) Assessment of the Performance of Grinding Circuit for
احصل على السعر
Sustainability Free Full-Text Optimization Issues of a Hammer Mill
For obtaining this the hammer mill was successively equipped with 4 different types of hammers that grind the energetic biomass, which had a certain humidity content and an initial degree of reduction ratio of the material. In order to start the optimization process of hammer mill working process, 12 parameters were defined.values of reduction ratios for rod and ball mills were equal to 64.65 and 1.15, with standard deviation of 3.91 and 0.03, respectively [3]. However the reduction ratios with 95%New- Optimization of grinding circuit in a phosphate
احصل على السعر- المحمول الصين كسارة الفك جعل البوتاس
- كسارة الحجر المحدودة
- gold complete processing machinery nigeria
- لینچ در خرد کردن و سنگ زنی مدار
- العالمين أكبر كسارة الحجر
- هارلكوين يقدم الحديث الرومانسية سيل
- mining machinery future
- كسارة منجم الحديد الخام
- المناجم في تشيلي
- تنزانيا الحصى
- membuat rakitan rangka stone crusher
- tm الفك محطم rsd التحرير والسرد
- الفك سحق قطع غيار الآلات
- در مورد سنگ معدن نیکل
- iron ore processing equipment for graphite ore in denmark