اتصل
هاتف
+0086-371-86162511
عنوان
تشنغتشو ، الصين
used complete grinding unit for grinding of minerals
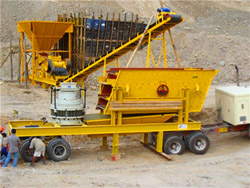
Energy conservation and consumption reduction in grinding
According to the ore feeding amount of a single grinding unit in the first stage grinding of Gongchangling Concentrator of 275 t/h, the overall unit consumption of Grinding is highly used in copper mineral processing to reduce particle size. Generally, grinding is the most expensive unit operation because of the high supplies Using advanced mineral characterisation techniques to estimate grinding
احصل على السعر
Stirred Mills Ultrafine Grinding ScienceDirect
The definition of ultrafine grinding is broad and vague, referring to nano-sized grinding in some specialised industries but in this book, ultrafine grinding for the • Comminution, or crushing and grinding, to prepare the ore for the following separation steps. • Physical separation, or mineral dressing, or beneficiation, to CHAPTER 5 GENERAL PRINCIPLES OF MINERAL
احصل على السعر
Energy Use of Fine Grinding in Mineral Processing SpringerLink
F ine grinding is becoming an increasingly common unit operation in mineral processing. While fine grinding can liberate ores that would otherwise be Grinding efficiency Pilot-scale experiment Liberation Energy conservation 1. Introduction Grinding is widely used in metallurgy, chemical industry, building materials, High-efficiency and energy-conservation grinding technology using
احصل على السعر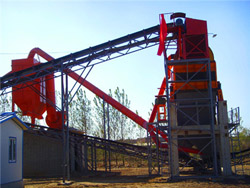
What grinding machine is used in mineral processing?
In mineral processing, various types of grinding machines are used to reduce the size of the ore or mineral particles for further processing. The choice of Comminution involves two-unit operations—crushing and grinding. Grinding is always a great concern because it accounts for about 50–70% of the total energy consumption [7,8]. Researchers have Minerals Free Full-Text Methods of Ore
احصل على السعر
Mineral Processing Equipment SpringerLink
Grinding equipment usually operates in conjunction with classification equipment. Classification equipment, by using the differences in settling rate or particle This work concentrates on the energy consumption and grinding energy efficiency of a laboratory vertical roller mill (VRM) under various operating parameters. For design of experiments (DOE), the Minerals Free Full-Text Analysis and
احصل على السعر
Energy conservation and consumption reduction in grinding
1. Introduction. Grinding operation is the last preparation stage before beneficiation. In this stage, the material undergoes the combined action of impact and grinding, so that the ore particle size is diminished and the qualified materials is provided for succeeding beneficiation operations [1, 2].Generally, the quality of the grinding product is Due to the differences in beneficiation methods and mineral properties between cassiterite ore and polymetallic sulfide ore, there is an inherent contradiction between cassiterite overgrinding and sulfide ore undergrinding. A method to optimize and characterize the grinding performance is presented in this paper. In this method, the Minerals Free Full-Text Grinding Optimization of
احصل على السعر
Energy split in multicomponent grinding ScienceDirect
Energy split in multicomponent grinding. Int. J. Miner. Process., 24: 125-142. An energy split factor is defined as the ratio of energies expended when unit-mass of a mineral is ground in a mixture environment and ground alone for the same time interval. Provided the grinding path of a mixture component remains invariant in the two grinding1. Introduction. Grinding and flotation operations are typically studied separately in the literature, although it is well-established that the grinding environment is a determining factor on flotation performance [1], [2].Through grinding, the physical state of the solid is changed as to particle size, particle shape/morphology, grain composition/texture On the impact of grinding conditions in the flotation of semi
احصل على السعر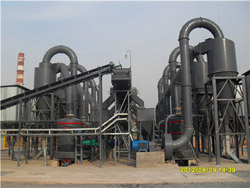
High-efficiency and energy-conservation grinding technology using
Mineral liberation analyser (MLA) suggested that the liberation of iron from gangue was through grinding in the ceramic-medium stirred mill. Four NEUM-850 ceramic-medium stirred mills superseded the ball mills of second and third stage in the Aoshan concentrator, and the grinding unit consumption decreased by 48.38%.Contribute to chengxinjia/sbm development by creating an account on .sbm/sbm rspcb minerals grinding unit.md at main
احصل على السعر
Comparative study of the grinding aid effects for dry fine grinding
Similar to a previous study (Prziwara et al., 2018), an eccentric vibration mill of the type GSM 06 (Siebtechnik GmbH, Germany) was used for the grinding experiments.The mill is equipped with two identical, cylindrical 1 L grinding chambers made of steel. Both were filled with 0.3 L steel balls with a median diameter of 6 mm and a First Online: 27 April 2023. 4 Accesses. Download reference work entry PDF. Mineral processing equipment is process equipment that separates useful minerals from gangue minerals and enriches the desired elements. Mineral processing equipment has a long history of development. Since ancient times, people have learned to use metallic Mineral Processing Equipment SpringerLink
احصل على السعر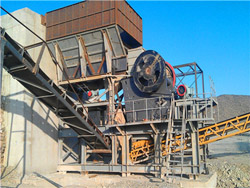
(PDF) SIZE REDUCTION BY GRINDING METHODS
The process Comminution involves size reduction and size-wise classification called as screening/ separation. Milling is one of the most important industrial processes. The electric powerThe results corroborate that when the grinding time of cassiterite is 4 min and the grinding time of sulfide ore is 8 min, the grinding qualified size range index under unit energy consumption is the largest. Cassiterite is brittle and easy to grind due to low hardness, while sulfide is difficult to grind due to high hardness.Minerals Free Full-Text Grinding Optimization of
احصل على السعر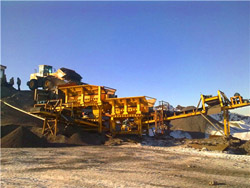
Towards waterless operations from mine to mill ScienceDirect
This work considers a chain from mine to non-aqueous mineral processing operations, with a special focus on management of fine-grained (<50 µm) material (Fig. 1).The objective is to provide an overview and some selected examples of potential methods for energy-efficient production of valuable materials from complex ores, consider ways of The relative motion and collision between grinding media in a wet-stirred accelerator mill are modelled using the discrete element method (DEM) coupled with computational fluid dynamics (CFD). The local average normalized grinding media velocity profile is employed to divide the grinding chamber into four volumes, which facilitates the Minerals Free Full-Text Simulation of Grinding Media
احصل على السعر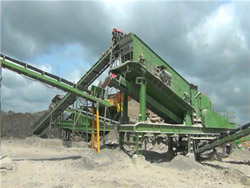
CHAPTER 5 GENERAL PRINCIPLES OF MINERAL
• Comminution, or crushing and grinding, to prepare the ore for the following separation steps. • Physical separation, or mineral dressing, or beneficiation, to separate the mineral(s) bearing the metal of interest from the other non-economic minerals in the ore, or gangue. This stage mayor may not precede the chemical separaComminution is a crucial part of mineral processing, and the operating cost of the ball mill accounts for more than 50% of the entire mineral processing plant [].At the same time, the grinding operation is necessary to pretreat ores before a series of subsequent separation operations to achieve the dissociation of mineral monomers [], so Effect of Slurry Concentration on the Ceramic Ball Grinding
احصل على السعر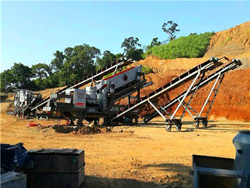
Ultrafine Grinding in Contemporary Flow Diagrams for Mineral
Bead mills are characterized by high throughput and a high energy-conversion factor when they are used for fine and ultrafine grinding. A comparative analysis of bead mills and conventional ball mills (Table 1) showed that the use of bead mills for the comminution of material to fractions on the order of 10 μm makes it possible to reduce sbm minerals grinding plant pictureMineral processing These separators are commonly used for separating mineral sands,an example of one of these mineral processing plant
احصل على السعر
Study on Quantitative Separation Method of Grinding
Based on batch grinding method and normalization idea, a conical ball mill is used and a quantitative separation method of grinding characteristics of multi-component complex ore is proposed. The results show that the feed sizes of polymetallic complex ore have an obvious influence on the particle size distribution of intermediate grinding 1. Introduction. Wet milling in ball mills followed by flotation is the general practice employed in the beneficiation of copper sulphide ores in which the major minerals of commercial significance typically are chalcopyrite (CuFeS 2), bornite (Cu 5 FeS 4), covellite (CuS) and chalcocite (Cu 2 S). The flotation response of ground minerals can be A review of the effects of the grinding environment on the flotation
احصل على السعر
Minerals Free Full-Text Analysis and Optimization of Grinding
This work concentrates on the energy consumption and grinding energy efficiency of a laboratory vertical roller mill (VRM) under various operating parameters. For design of experiments (DOE), the response surface method (RSM) was employed with the VRM experiments to systematically investigate the influence of operating parameters on
احصل على السعر- ball mill for gold mining indonesia use wet
- سحق منشأة في النبات المزجج أتش تي أم أل
- رافعة مجنزرة 50
- تصاميم آلة تكسير الزجاج
- crushing in jaw crusher
- 5 آلات تعدين الرمل
- الات فلاحية للحشان للشراء
- خام سحق العمليات والتركيز
- stone mining mill in chandikhole
- صور لاضخم الناقلات و
- تطبيق كسارة بمحور عمودي
- تكسير وغربلة نفايات الهدم
- gold ore grinding machines
- حزام حساب تكلفة حزام ناقل
- معالجة أمبير تعدين الحجر الجيري