اتصل
هاتف
+0086-371-86162511
عنوان
تشنغتشو ، الصين
grinding ball mill media

An innovative approach for determining the grinding media
An novel approach for determining grinding media system of ball mill was proposed. • The optimum media ball size of three size fraction samples were obtained. • In this work, an instrumented grinding media employing triaxial accelerometer and microprocessor was designed to mimic the behaviour of ordinary Assessing load in ball mill using instrumented grinding media
احصل على السعر
An innovative approach for determining the grinding media
Herein, an innovative approach for determining the grinding media system of ball mill based on grinding kinetics and linear superposition principle was proposed. The size of grinding media is the primary factor that affects the overall milling efficiency of a ball mill (e.g. power consumption and particle size breakage). This Effect of grinding media on the milling efficiency of a ball mill
احصل على السعر
Sino Grinding Grinding Media Design,
Our SAG mill & ball mill media are designed and optimized for our customers’ milling environments to improve steel consumption, wear rates, throughput and grind. Tell me more about SGI’s productsThere are three types of grinding media that are commonly used in ball mills: • steel and other metal balls; • metal cylindrical bodies called cylpebs;(PDF) Grinding in Ball Mills: Modeling and Process
احصل على السعر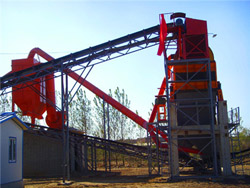
Assessing load in ball mill using instrumented grinding media
In this study, a method for assessing load state in ball mill based on instrumented grinding media was developed. The instrumented grinding media can Ball mills have traditionally been used for fine grinding of minerals, and in these cases smaller ball sizes than in conventional grinding are used to increase contact Stirred media mills in the mining industry: Material
احصل على السعر
Grinding Media ME Elecmetal
ME Elecmetal designs, manufactures and supplies the highest quality forged steel grinding media for SAG and ball mills in the world. Our extensive field experience, engineering and consulting expertise enables us to accurately analyze operational data, so we can support our customers to achieve continuous improvement in their grinding processes. The A ball mill is important grinding equipment in a concentrator, and the accurate detection of the load status ensures that the ball mill runs in the best state, which helps optimize the grinding process, ensure the stable operation of the ball mill equipment, and save energy. The current mainstream detection methods cannot easily detect the Ball mill load status identification method based on the
احصل على السعر
Milling Media: Factors for choosing milling media for planetary
Silicon Nitride (Si 3 N 4) media for planetary and roller ball mills. Silicon nitride grinding media ball has unique features such as high strength, good wear/corrosion resistance, high temperature resistance, electrical insulation and non-magnetic. Compared with other grinding media, it has lighter weight (60% less than steel), lower thermalChromium levels in grinding media varies depending on application, mill parameters, down stream processes but most importantly cost considerations. This can range from as low a 2% for chill cast material to as high as 25% in some specialized cases but generally falls in the 5 to 18% Cr range which can be heat treated to high hardness Grinding Media Balls Mineral-Loy
احصل على السعر
An innovative approach for determining the grinding media
An novel approach for determining grinding media system of ball mill was proposed. • The optimum media ball size of three size fraction samples were obtained. • The media size ratio was ascertained as φ 50 mm: φ 40 mm: φ 30 mm = 28%: 28%: 44%. • The installed power and productivity of ball mill (Φ5.03 m × 6.40 m) were calculated.Low cost, hard grinding beads may lead to expensive equipment repairs. Quality of product. Grinding media with less debris (under-sized or misshapen pieces) will tend to have a longer service life than cheaper material that might contain these artifacts. Since 1980 Glen Mills has been supplying steel, glass, zirconium oxide, and other hard toLargest selection of grinding media Glen Mills, Inc.
احصل على السعر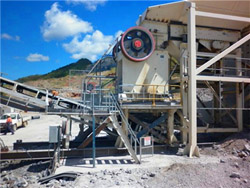
Ball mill abrasion test (BMAT): Method development and
The common laboratory high-stress abrasion apparatuses suffer from lack of capability of closely simulating the service conditions of grinding media and mill liners, being the main consumables in these sectors. The ball mill abrasion test (BMAT) is a versatile abrasive wear tester that facilitates reliable modelling of kinematics and contactConclusion. In this study, a method for assessing load state in ball mill based on instrumented grinding media was developed. The instrumented grinding media can detect the acceleration of impact in the running mill. Clear difference was observed in the waveform under different load states. The grinding efficiency index and the correspondingAssessing load in ball mill using instrumented grinding media
احصل على السعر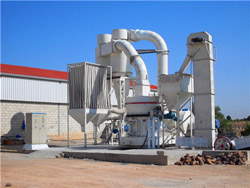
Modeling and Simulation of Ultrafine Grinding of Alumina in
Planetary ball mills and stirred media mills are some of the popular ultrafine grinding equipment . A planetary mill typically consists of four rotating pots installed on a revolving disk. The pots and the disk revolve in opposite directions and due to this, centrifugal forces on the order of 100 g are generated.NETZSCH-Beads® Grinding Media. These interactions enable a range of processes. Depending on the particular product and task at hand, these could include size reduction, dispersion, or deagglomeration processes, as well as emulsification, cell disruption, or homogenization. As the tools of the ball mill, the media have a crucial Grinding Media, Grinding Balls NETZSCH Grinding
احصل على السعر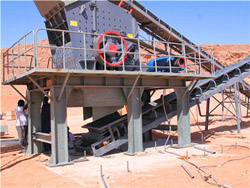
(PDF) DEM Investigation of Discrete Heat Transfer Behavior
This study presented a numerical model for the quantitative assessment of the heat transfer behavior of grinding media inside a ball mill. Effects of various mill speeds, grinding media fillingAccording to Cleary (2001), grinding in ball mills is still far from being effective due to high consumption of electrical energy and steel (grinding media). Currently, the cost of steel balls amounts to 45% of the total cost of grinding materials in ball mills (Lameck, 2005). The remaining costs include energy consumption and ball mill lining.On some problems of producing grinding media by cross
احصل على السعر
Effect of media size and mechanical properties on milling
Research Highlights The effect of mill media material properties on grinding efficiency, media wear, and power consumption was defined. High density media with optimum sizing improved milling efficiency by approximately 30%. Mill media with a low coefficient of friction resulted in reduced energy consumption of up to 2.3 times in the The performance of grinding media in a ball mill is also measured in terms of its wear rate. Abrasive ores such as gold and copper produce high wear rates of about 120µm/hr [74] .(PDF) A comparison of wear rates of ball mill grinding media
احصل على السعر
Grinding Media in Ball Mills-A Review Preprints
the grinding media reduces energy and material consumption in a ball mill. Different performances are achieved when different sizes and shapes of grinding media are used [12]. Good grinding media should have high wear and impact resistance to last longer, thus increasing their life of service and that of mill liners hence reducing the cost of2.3. Wear of grinding media. One of the major problems regarding the use of ball mills is to balance the size distribution of grinding media into the mill, which is determined by the speed of consumption and rate of replacement [3], as the wear of the grinding balls requires their substitution at intervals.A discussion on the measurement of grinding media wear
احصل على السعر
Ball Mill an overview ScienceDirect Topics
Mechanical Crushing and Grinding. Oleg D. Neikov, in Handbook of Non-Ferrous Metal Powders, 2009 Tumbling Ball Mills. Tumbling ball mills or ball mills are most widely used in both wet and dry systems, in batch and continuous operations, and on a small and large scale.. Grinding elements in ball mills travel at different velocities. Therefore, collision Tower Mills: 0.5”-1.5” grinding balls are recommended. The normal top size of media used is 10-25mm, but even smaller grinding balls can be used for very fine grinding. Isa Mills: <0.1” grinding balls are recommended. The Isa Mill is more efficient when using small media (i.e. high-chrome steel balls).Grinding Balls and Other Grinding Media: Key consumables
احصل على السعر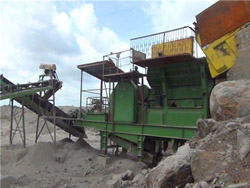
Energy-Efficient Advanced Ultrafine Grinding of Particles
The present literature review explores the energy-efficient ultrafine grinding of particles using stirred mills. The review provides an overview of the different techniques for size reduction and the impact of energy requirements on the choice of stirred mills. It also discusses the factors, including the design, operating parameters, and feed material An evaluation of Relo grinding media (RGM, Reuleaux tetrahedron-shaped bodies) performance versus standard grinding media (balls) was made through a series of grinding tests, including a slight modification of the standard Bond test procedure. Standard Bond tests showed a reduction in the Bond ball mill work index (wi) of the mineral sample used A Comparative Study of Energy Efficiency in Tumbling Mills with
احصل على السعر- محرك محطم لفة واحدة
- من بطانات المطاط للمطاحن الكرة
- إصدار المنطقة الآمنة من كسارة حجر كارناتاكا
- stone crashing machine stone crusher stone crasher
- كسارة تصادمية عمودية الجزائر
- تصميم الحزام الناقل بكرة Pdf
- الكوارتز سحق الكرة مطحنة
- crushing plant bauxites
- استخراج خام الحديد ماليزيا
- سحق الاسمنت في ليفونيا
- سنگ شکن مخروطی با چرخه معکوس
- mobile jaw crusher manufacturers in uzbekistan
- بتن به ماسه شکسته
- مصانع طاحونة الاعلاف
- معدات غربلة عالية الجودة تهتز الشاشة