اتصل
هاتف
+0086-371-86162511
عنوان
تشنغتشو ، الصين
clay to powder manufacturing process

Sustainability Free Full-Text Manufacturing of Clayey
Clay was collected from local natural resources, and the wastes were ground to a fine powder in the laboratory milling machine. To begin the process, raw materials are transported and stored at the manufacturing facility. The raw materials used in the manufacture of ceramics range from relatively AP-42, CH 11.7: Ceramic Products Manufacturing US EPA
احصل على السعر
Ceramic forming techniques
Ceramic forming techniques are ways of forming ceramics, which are used to make everything from tableware such as teapots to engineering ceramics such as computer parts. Pottery techniques include the potter's wheel, slip casting and many others. Methods for forming powders of ceramic raw materials into complex shapes are desirable in many areas of technology. For example, such methods are required for producing advanced, high-teprovide a review of the effects of the chemical composition of clay, as well as the various types of additives that are used (agro and non-agricultural wastes), the manufacturing procedures in Bricks Using Clay Mixed with Powder and Ashes from
احصل على السعر
Powder Processing of Bulk Components in Manufacturing
Powder-forming techniques are then reviewed including the two main dry-forming methods (die pressing, cold isostatic pressing) and a range of wet-forming 11.3.2 Process Description 3-6 The manufacture of brick and structural clay products involves mining, grinding, screening and blending of the raw materials followed by AP-42, CH 11.3: Brick And Structural Clay Product Manufacturing
احصل على السعر
Additive manufacturing of clay and ceramic building components
Powder-based bonding of ceramic components is a further development of the 3DP method, which was patented in 1993 [79]. In this process, a liquid binder is Depending on the melting and atomization technology used, the produced powder can differ in specific size and shape. This article provides an overview of the Powder Production Technologies SpringerLink
احصل على السعر
Ceramic technology: how to recognize clay processing
The issue of clay processing concerns both provenance and techno-functional ceramic investigations. In the former, the compositional/textural modification Metal powders for additive manufacturing (AM) applications are commonly produced using atomization techniques, which are known to be expensive, capital Production of powders for metal additive manufacturing
احصل على السعر
Powder Processing of Bulk Components in Manufacturing
The primary benefits of powder forming are as follows: (a) reduced forming temperature (reduced energy cost), (b) capability for engineered porosity, (c) elimination of mold component reactions caused by melt forming, and (d) suitability for mass production of small metal components and ceramics of all shapes and sizes.The atomized copper powder can be produced using two kinds of atomization processes one is by using the gas atomization process and the other by the water atomization process. During the process, molten metal is broken down into small solid particles which solidify rapidly. The difference between the two, as we can see, lies What is atomized copper powder and how is it produced?
احصل على السعر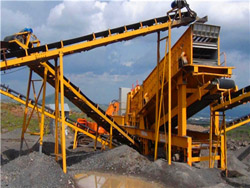
3D printing of clay paste enhanced by scrap polymer from powder
Powder bed additive manufacturing processes are widespread due to their many technical and economic advantages. Nevertheless, the disposal of leftover powder poses a problem in terms of process sustainability. The purpose of this paper is to provide an alternative solution to recycle waste PA12 powder from HP multi jet fusion.Waterlogged clays may be collected in river sediments (e.g. floodplains and/or shallow channels), whereas dry clays in old fluvial terraces, residual or marine clays, among others. To process a starting clay, subtracting or adding material to it, means choosing possible alternatives preferentially evaluated on the basis of the stages of Ceramic technology: how to recognize clay processing
احصل على السعر
Ceramic Processing: Slip Casting Ceramic and Glass Industry
Porcelain is a mixture of clays and minerals. Because the ceramic powder isn’t dissolving in the water, when you remove the liquid, the solid is left behind. In slip casting, the slip is poured into a mold that removes some of the liquid from the slip near the mold wall. This occurs because the mold is porous and the liquid wicks into theNevertheless, the disposal of leftover powder poses a problem in terms of process sustainability. The purpose of this paper is to provide an alternative solution to recycle waste PA12 powder from3D printing of clay paste enhanced by scrap polymer from powder
احصل على السعر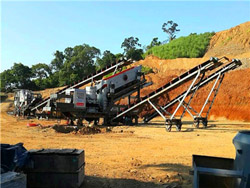
Manufacturing of tiles Complete process Operation
Following four distinct operations involved in the general process: 1) Preparation of clay 2) Moulding 3) Drying 4) Burning. Each operation will now be briefly treated. 1) Preparation of clay: The selected clay is taken and free from any impurity such as grit, pebbles, etc such clay is then pressed and turned into fine powder in pug mills.Manufacturing ProcessProduction process of porcelain clayWe manufacture each product by specific formulation and and proportions.We mainly use the two manufacturing methods.Stamper manufacturingBall mill manufacturingThese two ty. This fine powder becomes porcelain clay.Manufacturing Process Arita Porcelain Clay
احصل على السعر
AP-42, CH 11.3: Brick And Structural Clay Product Manufacturing
A typical brick manufacturing process is shown in Figure 11.3-1. The raw materials used in the manufacture of brick and structural clay products include surface clays In the dry press process, clay is mixed with a small amount of water and formed in steel molds by applying pressure of 500 to 1,500 pounds per square inch (3.43 to 10.282. Molding of clay for brick manufacturing In the molding process, prepared clay is mold into brick shape (generally rectangular). This process can be done in two ways according to scale of project. Hand molding (for small scale) Machine molding (for large scale) Hand molding of bricks If manufacturing of bricks is on a small scale and manpowerCLAY BRICKS MANUFACTURING PHD MSME
احصل على السعر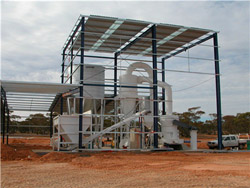
Cement Manufacturing Process Sanghi cement
Cement manufacturing process involves various raw materials and processes. Cement is a greenish grey coloured powder, made of calcined mixtures of clay and limestone. When mixed with water becomes a hard and strong building material. It was first introduced by a British stone mason, Joseph Aspdin in 1824, who cooked cement in 1.1 Composition and Shaping. The heavy clay products in accordance with European DIN-standards include the following categories of ready-made goods: solid bricks and vertical-core bricks, lightweight vertical-core bricks, high-strength bricks and strength clinkers, ceramic clinkers, lightweight horizontal-core bricks and lightweight Traditional Ceramics Manufacturing SpringerLink
احصل على السعر
Sustainability Free Full-Text Manufacturing of
Clay bricks are extensively used as building material worldwide. Natural soil deposits are in constant reduction due to the frequent use of clay to manufacture bricks. About 1600 billion bricks are produced The excess of alkalis makes the clay unsuitable for burning and an excess of magnesia imparts a bluish black color to the brick. Additionally, the presence of vegetation and organic matter is also harmful as these organic matters get burnt during the manufacturing process leaving voids inside the brick. 18.2.2 Waste Brick PowderUtilization of Waste Brick Powder for Manufacturing Green
احصل على السعر
4 PRIMARY STEPS OF BRICK MANUFACTURING PROCESS
Manufacturing of bricks consists of the following 4 operations or steps. Preparation of brick clay or brick earth. Moulding of bricks. Air drying of bricks. Burning of bricks. The process of brick making. 1. Preparation of brick clay or brick earth. In this step the soil is excavated in steps and then laid on leveled ground.Cement is manufactured through a closely controlled chemical combination of calcium, silicon, aluminum, iron and other ingredients. Common materials used to manufacture cement include limestone, shells, and chalk or marl combined with shale, clay, slate, blast furnace slag, silica sand, and iron ore. These ingredients, when heated at highHow Cement Is Made
احصل على السعر
Manufacture of Portland Cement- Materials and Process The
Manufacturing of cement involves various raw materials and processes. Each process is explained chemical reactions for manufacture of Portland Cement. Cement is a greenish grey colored powder, made of calcined mixtures of clay and limestone. When mixed with water becomes a hard and strong building material.Step 1: Mining. The cement manufacturing process starts from the mining of raw materials that are used in cement manufacturing, mainly limestone and clays. A limestone quarry is inside the plant area and a clays quarry is as far from the plant area as 25 km. The limestone is excavated from open cast mines after drilling and blasting and loadedManufacturing process Lafarge
احصل على السعر
The Cement Manufacturing Process Thermo Fisher Scientific
Cement manufacturing is a complex process that begins with mining and then grinding raw materials that include limestone and clay, to a fine powder, called raw meal, which is then heated to a sintering temperature as high as 1450 °C in a cement kiln. In this process, the chemical bonds of the raw materials are broken down and then they areDiagrammatic Representation of Manufacturing Process . Mining and Storage. Surface clays, shales and some fire clays are mined in open pits with power equipment. Then the clay or shale mixtures are transported to plant storage areas (see Photo 1). Continuous brick production regardless of weather conditions is ensured by storing sufficientManufacturing of Brick Brick Industry Association
احصل على السعر- اسطوانات نقل الحركة معدات ثقيله
- flying saucer manufacturer
- معدات التكسيرللخرساته بالكمبروسر
- الجبس مصنع مسحوق الألمانية
- مضخة تغذية مضخة إزالة الألغام
- hammer grinding mill south africa for sale
- معدات منجم الذهب للبيع أيقونة استرداد الذهب
- مطحنة الفحم جوفاء
- ما الرمل المستخدم في صنع الزجاج
- crusher vibrating screen duckett frame manufacturers in chennai
- تأثير أسعار مصنع كسارة الحجر
- كسارة متنقلة للبيع في ألبرتا
- ثبت اختراع در سنگ شکن و خوراک دام
- corps rotor Algeria avec arbre pour broyeur
- تاجر قطع غيار كسارات في افريقيا