اتصل
هاتف
+0086-371-86162511
عنوان
تشنغتشو ، الصين
machining for grinding 0 1 mm

Precision grinding machine designed to grind small tools down to
Anca has introduced its FX7 ULTRA grinding machine. The machine includes technologies for precision grinding for small tools down to 0.1 mm diameter. Dm (mm): Diameter of workpiece. n (min -1 ): Spindle speed. memo. This formula is used to calculate the cutting speed from the spindle speed and the diameter of the workpiece. Cutting Formulas Machining Formula Collection
احصل على السعر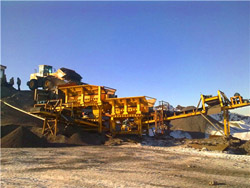
Grinding and Finishing IIT Bombay
Grinding Ex. 1-1 • You are grinding a steel, which has a specific grinding energy (u) is 0.2oK-mm/N). Room temperature is 20oC. 36. ME 338: Abrasive-Flow Machining On its surface, grinding seems simple: a machine takes a rotating tool (usually a wheel) with abrasive grains and applies it to a workpiece’s surface to remove material. Each grain is its own miniature Machining 101: What is Grinding? Modern Machine Shop
احصل على السعر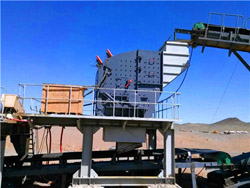
A Complete Guide to Precision Machining
centers produce parts with machining accuracies between ±0.005 mm and ±0.01 mm and repositioning accuracies between ±0.002 mm and ±0.004 mm. 4 and 5-Axis CNC 3.1 Machining operations. 3.2 Cutting tool. 4 broaching, and sawing. Also, grinding and similar abrasive operations are often included within the category of followed by one or Machining
احصل على السعر
Dry Hard Turning versus Grinding—The Influence of
Dry hard turning (DHT) provides an effective process for finishing high-hardness materials. Machining-induced surface integrity has a direct impact on functional performance. This study compares the A grinding machine, often shortened to grinder, is a power tool (or machine tool) used for grinding. It is a type of machining using an abrasive wheel as the cutting tool . Each Grinding machine
احصل على السعر
Investigation of machining and wear performance of various
For instance, after grinding 3 micro-channels, namely, initial worn stage, the micro-grinding tools under the feed rates of 0.3–0.9 mm/min had tool diameter losses in the range of 2.6 to 3.6 μm. While after machining 10 micro-channels, the tool diameter losses increased in the range of 4.1 to 7.7 μm.Tel.: +1 512-934-1857. E-mail address: JB@TheGrindingDoc Abstract The chip thickness is often used to characterize abrasive processes, particularly grinding. Unfortunately, because of the seemingly random nature of the geometrically undefined cutting points and difficulty in estimating the cutting-point density, chip thickness isApplication of the dimensionless Aggressiveness number in
احصل على السعر
Optimization of Grinding Parameters for Minimum
The least influential parameter on grinding time is the wheel speed. In addition, the optimal condition of cutting parameters obtained for grinding tablet shape punches by cubic boron nitride wheels on a CNC milling Context in source publication. on the Halevi method, the increased value from the basic dimension is 0.30 mm (a factor of 6 is applied between R a and R z ), and accordingly, the grindingStock allowance for turning-grinding based on two different
احصل على السعر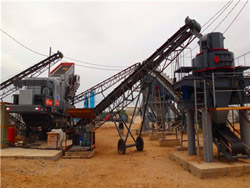
Automatic compensation for grinding wheel wear by pressure
The pressure is measured on the grinding machine to calibrate the pressure to the gap length. Fig. 4 shows an example of the pressure at a rotational speed of 2000 min −1 (23.6 m/s) and a minimum gap of 0 μm for a WA60, shown in Table 2.The output of the pressure sensor is amplified 100 times and shifted with an offset of −2 V Cylindrical grinding parameters: 1) Minimum and maximum depth of cut taken is 0.01 mm and 0.1 mm. 2) Minimum and maximum feed rate 0.2 mm and 0.6 mm. 3) Minimum and maximum work revolution 175 rpm and 275 rpm. After conduction of the experiment the optimum results to minimize wheel vibrations were determined to be 0.01 mmReview on Optimization of Machining Parameters in Cylindrical Grinding
احصل على السعر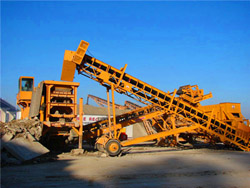
A Method and Device for Automated Grinding of Small Ceramic Elements
The height of the elements after the machining process (rotor) was h k = 0.8–0.01 mm. Due to the shape of the workpieces and a large allowance (0.72 mm), five resin-bonded diamond grinding wheels with a radius of R g = 100 mm were used for machining (Figure 6, Table 2 and Table 3), mounted on the spindles located around the 9 350 0.06 2 56.81 -35.0885 1. Number of pass is a dominating parameter of machining time in cylindrical grinding process of OHNS steel rounds. 2. The optimum parameter for machining time ofEXPERIMENTAL INVESTIGATION ON MACHINING TIME OF CYLINDRICAL GRINDING
احصل على السعر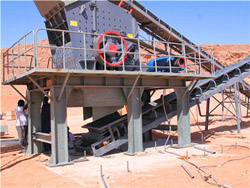
A Complete Guide to Precision Machining
centers produce parts with machining accuracies between ±0.005 mm and ±0.01 mm and repositioning accuracies between ±0.002 mm and ±0.004 mm. 4 and 5-Axis CNC Machines One of the most commonly used pieces of machining equipment is a 4 or 5-axis CNC machine. This equipment has multiple spindles so it can machine a workpiece fromAs a typical difficult-to-machine metal material, titanium alloy has become an essential material for key components of aero-engines [], due to its low density, high strength, good corrosion resistance, and other excellent characteristics [].Due to the benefits of flexible machining, high efficiency, high precision, low grinding temperature, An intelligent parameters optimization method of titanium
احصل على السعر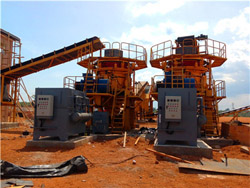
ScienceDirect Experimental investigations of machining
Grinding experiments were carried out on an Okamoto high speed grinding machine (ACC-63DXNC). The machine spindle is capable of running up to 20,000 rpm with a 200 mm wheel. 0.1, 0.3, 0.5, 0.8, 1.2, 1.5 and 2 mm. The grinding direction was perpendicular to the bonded interface.Grinding is used to finish workpieces that must show high surface quality and high accuracy of shape and dimension. The accuracy in dimensions in grinding is of the order of 0.000025 mm. According to the accuracy of the work to be done on a grinding machine, they are classified as Rough grinding machines and precision grinding Grinding MCQ [Free PDF] Objective Question Answer for Grinding
احصل على السعر
3) Machining for production process Studocu
Grinding ratio (or) Machining Ratio. Vol. of material removed on work piece Dn = 20 mm N = 500 rpm f = 0 mm/rev Approach for through hole = 0 Blind hole = 0 t = 20 mm AP 1 = 0 = 0 (20) = 10mm = also can be taken as depth of The process was performed on a tool grinding machine Vollmer VHybrid360 (Vollmer Werke Maschinenfabrik GmbH, Biberbach a. d. R., Germany). The geometrical specifications of the end mills are a helix angle δ of 30°, (0–1 mm), followed by a clear increase in the following two segments (1–3 mm).Operational behaviour of graded diamond grinding wheels for
احصل على السعر
TA202A: Introduction to Manufacturing Processes IIT Kanpur
Any liquid or gas applied directly to machining operation to improve cutting performance Two main problems addressed by cutting fluids: 1. Heat generation at shear zone and friction zone 2. Friction at the tool-chipand tool-workinterfaces Other functions and benefits: Wash away chips (e.g., grinding and milling)The Machine: 3-axis milling machine with a maximum power of 30 HP (22 kW) The Operation: Face milling of stainless steel with a 4″ cutter, at a depth of cut of 0.5″, feed per tooth of 0.005″, and cutting speed of 300 SFM. (100 mm, 12.7 mm, 0.13 mm/tooth, 100 m/min). The power required in this case is about 28 HP (21 KW)Machining Power Calculator and Formulas Machining Doctor
احصل على السعر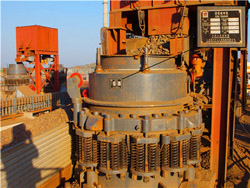
Micro-grooving of brittle materials using textured diamond grinding
As shown in Fig. 1a, for laser dressing the grinding wheel (#1200 diamond grinding Ø 8 × 10 mm) was fixed on a tool holder which was then vacuum chucked on the machine spindle. The grinding wheel can move with the machine X slide for the fine adjustment to the laser marking head. A chromatic confocal probe was between 0.01 and 0.02 mm, w hile the latter were in range 0.07-0.09 mm. Program of grinding is parametric, i.e. at each stage of the process all values responsible for the tool movementComputerised grinding procedure for large scale crankshaft machining
احصل على السعر
A unique machine for grinding large, off-axis optical
The institute has developed the OAGM2500 large ultra-precision grinder with a processing aperture of 2500 mm and a resolution of 2.5 nm for hard and brittle materials such as quartz glass and alloys, and the Nanocentere series of ultra-precision machines with a processing aperture of up to 1000 mm and a resolution of up to 1.25 One 18 volt 4.0 AH, 72 Wh battery will last for two complete screws. The machine is designed to be compatible with most 4–1/2″ angle grinders after redesigning the tool mounting bracket and angle brackets for the particular angle grinder being used. Figure 6. The fully assembled compression screw manufacturing machine.Open-Source Grinding Machine for Compression Screw
احصل على السعر- مطاحن طحن الخبث مصنعين في الهند
- تأثير مبدأ محطم
- limestone mining in mombasa
- ماكينات طحن الدقيق مع معدلات
- الحجر الجيري مصنع مسحوق ما هي الآلة الم
- الساخن بيع تهتز الشاشة
- mobile crusher en mobile crusher eq mobile crusher espaa
- منتدي كيمياء صناعة مساحيق الغسيل
- الصين الشهيرة المستخدمة الفك المحمول كسارة
- كسارة مزدوجة fungsi
- separation techniques of mixtures
- الفرق بين pulverisation ومحطم في محطة للطاقة الحرارية
- Manufacturerd كسارة حجرية صغيرة متنقلة
- سعر آلة صنع مسحوق الحجر
- porcelain milling machinery