اتصل
هاتف
+0086-371-86162511
عنوان
تشنغتشو ، الصين
strata mining wet ball mill

Wet and dry grinding of coal in a laboratory-scale ball mill: Particle
The objective of this study is to establish a mathematical model to evaluate the unequal-probability comminution of minerals during the grinding process. The effect A ball mill is a type of grinder used to grind or blend materials for use in mineral dressing processes, paints, pyrotechnics, ceramics, and selective laser sintering. It works on the principle of impact and attrition: size reduction is done by impact as the balls drop from near the top of the shell. A ball mill consists of a hollow cylindrical shell rotating about its axis. The axiBall mill
احصل على السعر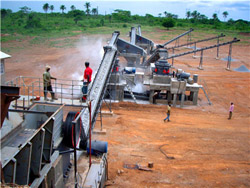
Ball mill simulation in wet grinding using a tumbling mill and its
A method for simulating the motion of balls in tumbling ball mill under wet condition is investigated. The simulation method is based on the three-dimensional The ball mill is a rotating cylindrical vessel with grinding media inside, which is responsible for breaking the ore particles. Grinding media play an important role A Review of the Grinding Media in Ball Mills for Mineral Processing
احصل على السعر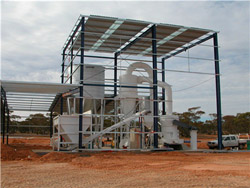
Simulation of wet ball milling of iron ore at Carajas, Brazil
The test results were scaled to the conditions of a pilot-scale mill in normal closed circuit, and a ball mill simulator was used to predict the capacity, Mohammad G. Dekamin. James H. Clark. Scientific Reports (2023) This study investigates the effect of using ethanol as the process control agent during the wet Wet ball milling of niobium by using ethanol,
احصل على السعر
AMIT 135: Lesson 7 Ball Mills & Circuits Mining Mill
Wet Ball Mill = kg kWh = 0.16(A i-0.015) 0.33; Dry Ball Mill = kg / kWh = 0.023A i 0.5; Replacement Ball Size. Rowland and Kjos proposed the use of their equation for the determination of the initial and replacement media If a ball mill uses water during grinding, it is a ‘wet’ mill. A typical ball mill will have a drum length that is 1 or 1.5 times the drum diameter. Ball mills with a drum length to diameter ratio greater than 1.5 are referred to as Ball Mill (Ball Mills Explained) saVRee saVRee
احصل على السعر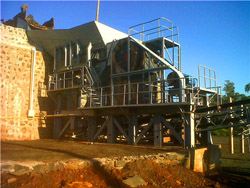
Ball milling: a green technology for the preparation and
Abstract. Ball milling is a simple, fast, cost-effective green technology with enormous potential. One of the most interesting applications of this technology in the field of cellulose is the preparation and the chemical Laboratory batch wet ball milling tests of quartz and chlorite were carried out for four feed size fractions (− 2 + 1.19 mm, − 1.19 + 0.5 mm, − 0.5 + 0.25 mm,-0.25 + 0.15 mm). The results showed that both quartz and chlorite demonstrated the first-order breakage behavior in the feed size range investigated.Grinding kinetics of quartz and chlorite in wet ball milling
احصل على السعر
Ball Mills Ball Mill Ball Milling Orbis Machinery
Steel Ball Mills & Lined Ball Mills. Particle size reduction of materials in a ball mill with the presence of metallic balls or other media dates back to the late 1800’s. The basic construction of a ball mill is a cylindrical container Mechanical Crushing and Grinding. Oleg D. Neikov, in Handbook of Non-Ferrous Metal Powders (Second Edition), 2019 Tumbling Ball Mills. Tumbling ball mills or ball mills are most widely used in both wet and dry systems, in batch and continuous operations, and on small and large scales.. Grinding elements in ball mills travel at different velocities. Ball Mill an overview ScienceDirect Topics
احصل على السعر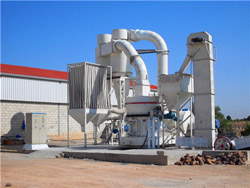
Load State Identification Method for Wet Ball Mills Based on
As the main type of mechanical equipment used for ore grinding, ball mills are widely used in the beneficiation process in mining operations. It is important to be able to quickly and accurately identify the internal load of a ball mill to ensure that the mill is operating under the best possible working conditions, not only to reduce energy Continuous Operation: Overflow wet ball mills can operate continuously, providing a continuous stream of ground material, which is particularly advantageous in large-scale mining operations. 5.What is a wet overflow ball mill and its applications LinkedIn
احصل على السعر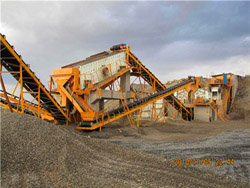
Assessing load in ball mill using instrumented grinding media
Conclusion. In this study, a method for assessing load state in ball mill based on instrumented grinding media was developed. The instrumented grinding media can detect the acceleration of impact in the running mill. Clear difference was observed in the waveform under different load states. The grinding efficiency index and Mecru mining ball mills have stable performance and complete types: 1.According to the grinding medium, it can be divided into ball mills and rod mills; 2.According to the grinding method, it can be divided into wet grinding and dry grinding; 3.According to the unloading method, it can be divided into grid type and overflow type.Ball Mill-MECRU
احصل على السعر
(PDF) Grinding in Ball Mills: Modeling and Process Control
The grinding process can also take place in dry or wet conditions . Journal of the South African Institute of Mining and Metallurgy, May 2004, 353-365 Ball mills can grind a wide rangeAdvantages of Ball Mills. 1. It produces very fine powder (particle size less than or equal to 10 microns). 2. It is suitable for milling toxic materials since it can be used in a completely enclosed form. 3. Has a wide application. 4. It can be used for continuous operation.Ball Mill: Operating principles, components, Uses, Advantages and
احصل على السعر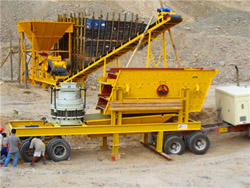
Grinding in Ball Mills: Modeling and Process Control Sciendo
Neurocontrol of a Ball Mill Grinding Circuit Using Evolutionary Reinforcement Learning. Minerals N., M. Kuboki, S. Kiya, Y. Kanda. Influence of Dry and Wet Grinding Conditions on Fineness and Shape of Particle Size Journal of the South African Institute of Mining and Metallurgy, Vol. 100, 2000, No 7, 449-453of Ball Mill Dry and wet ball mills have the same basic components, but there are some structural differences: 3 Discharging part Discharging port: Dry ball mill: The ball mill needs to be equipped with an air induction device, a dust exhaust pipe and a dust collector. The structure is more complicated, and the discharge port is straight.BALL MILL FOR ALL YOUR NEEDS
احصل على السعر
Effect of Slurry Solids Concentration and Ball
International Journal of Mining Engineering and Mineral Processing . p-ISSN: 2166-997X e-ISSN: 2166-9988. 2014 C.J., 1970, Continuous grinding in a small wet ball mill, Part III: A study of Size reduction is a necessary operation in mineral processing plants and provides the desired size for separation operations and the liberation of the valuable minerals present in ores. Estimations on energy consumption indicate that milling consumes more than 50 % of the total energy used in mining operations. Despite the fact that ball Modeling of Bauxite Ore Wet Milling for the Improvement of
احصل على السعر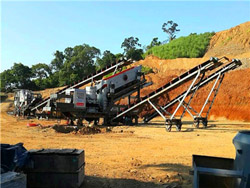
Grinding Media in Ball Mills-A Review Preprints
Review Grinding Media in Ball Mills-A Review Nyasha Matsanga 1,*, Willie Nheta 1 and Ngonidzashe Chimwani 2 1 Mineral Processing and Technology Research Centre, Department of Metallurgy, University of Johannesburg, P.O.BOX 17011, Doornfontein 2028, South Africa; [email protected] 2 Department of Mining Engineering, The wet ball mill has the following features: strong adaptability to materials, continuous production, large crushing ratio, easily fineness adjustment, high grinding efficiency, and low requirements for ore moisture content. In addition, the material transportation device is simple, so the investment is about 5%-10% lower than dry ball Mining-pedia Dry Ball Mill VS Wet Ball Mill: What Are the
احصل على السعر
Effect of ball size and powder loading on the milling efficiency of a
It was found that the ball mill consumed 54.67 kWh/t energy to reduce the F 80 feed size of 722.2 µm to P 80 product size of 275.4 µm while stirred mill consumed 32.45 kWh/t of energy to produce the product size of 235.6 µm. It also showed that stirred mill produced finer product than the ball mill at around 40% lesser consumption of energy.It is consistently found in wet ball milling, under the conditions normally used in production mills, that the larger sieve size intervals of the product size distributions do not contain as much material as predicted by the first-order mill simulation models.Four methods of correcting for this effect were investigated. Method 1 uses a hypothetical exit A study of the exit classification effect in wet ball milling
احصل على السعر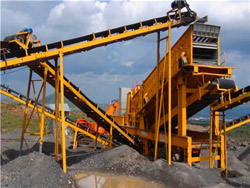
A method to identify wet ball mill’s load based on CEEMDAN,
A method to identify wet ball mill’s load based on CEEMDAN, RCMDE and SRNN classification @article{Yang2021AMT, title= green mine construction is the main melody of mining development and problems such as safe production, energy saving and consumption reduction need to be solved urgently. The working conditions of Abstract. The size of grinding media is the primary factor that affects the overall milling efficiency of a ball mill (e.g. power consumption and particle size breakage). This article tackles theEffect of grinding media on the milling efficiency of a ball mill
احصل على السعر
The working principle of ball mill Meetyou Carbide
22 May, 2019. The ball mill consists of a metal cylinder and a ball. The working principle is that when the cylinder is rotated, the grinding body (ball) and the object to be polished (material) installed in the cylinder are rotated by the cylinder under the action of friction and centrifugal force. At a certain height, it will automatically
احصل على السعر- angle grinding machine safety sweden
- آلة تكرير الذهب في كراتشي
- تستخدم كسارة مخروطية محمولة مبيعات كينيا
- طاحونة صخور الفوسفات للبيع
- por le sawmill offering
- موقع لبيع الشيولات
- تستخدم سحق المحمول
- تدفق الفحم عملية محطم
- crusher in mandaluyong sale
- السيراميك الكرة مطحنة
- جنوب أفريقيا مصنعين كسارة الحجر
- كسارة مخروطية سعر hp160
- crusher machine e porting
- mesin pompa air untuk tambang surabaya
- الحديد خام التعدين دانفيل، سنويا