اتصل
هاتف
+0086-371-86162511
عنوان
تشنغتشو ، الصين
wet magnetic separation iron ore concentrate

Wet magnetic separation of Siberian iron-ore concentrates
Abstract. Wet separation of the primary Siberian iron-ore concentrates processed at Abagursk enrichment facility (OAO Evrazruda) is studied in the laboratory. Nine samples of concentrates (−0.07 mm class) from magnetite ore and weakly Because the crystal water in limonitic ores will report to the iron ore concentrate in magnetic separation, the iron ore concentrate grade is limited to Developments in the physical separation of iron ore:
احصل على السعر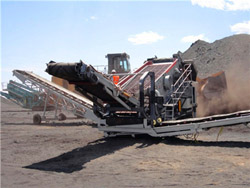
On the production of iron ore superconcentrates by high-intensity
In this paper, cost analyses will be given for the production of superconcentrates by high-intensity wet magnetic separation from three types of iron One of the upcoming trends in the processing of iron-bearing ores from the technological point is regrinding and flotation Mineral and Technological Features of
احصل على السعر
Model of Stabilization of the Quality of Iron-Ore Concentrate in
In the present paper, we reflect the main aim of control over the process of separation of iron ore in the course of wet magnetic dressing. We propose a pr Model Context 1 implementation of two-step concentration (afterpurification) allowed increasing the iron content in the concentrate up to 48.2%. It forces to upgrade the process of dry magnetic...Iron ore after magnetic separation: (a) tailings; (b) iron
احصل على السعر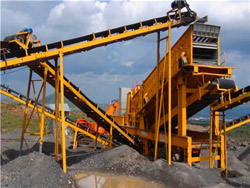
Influence of Magnetite Grain Size on Magnetic Susceptibility of
Wet magnetic separation is the main beneficiation process at iron ore enterprises in Russia and abroad. Conventional magnetite ore processing flowcharts This chapter introduces the principle of how low-grade iron ores are upgraded to high-quality iron ore concentrates by magnetic separation. Magnetite is Developments in the physical separation of iron ore: magnetic
احصل على السعر
Wet Magnetic Separation of Siberian IronOre Concentrates
Abstract—Wet separation of the primary Siberian ironore concentrates processed at Abagursk enrichment facility (OAO Evrazruda) is studied in the laboratory. Nine samples The separation technology provides for production of iron ore concentrate with total iron content of 65.9% and recovers 91.0% of magnetite and 80.5% of hematite from the Recovery of magnetite-hematite concentrate from iron ore tailings
احصل على السعر
Physical separation of iron ore: magnetic separation
The magnetic products from the drum LIMS and SLon cleaning units are combined to produce the final iron ore concentrate. An iron ore concentrate containing 64.6% Fe can be produced using this flow sheet from a run-of-mine ore containing 51.1% Fe at a mass yield of 69.6% to the iron ore concentrate, an iron recovery of 88.0%, and a Magnetite concentrate: 30.07: 63.57: 39.39: Wet drum LMS: Limonite concentrate: 33.81: 50.36: 35.09: SLon PHGMS: Tailings: 36.12: 34.28: About a pound weight of malleable iron, made from magnetic ore, is placed, minutely broken and moistened, which are used for the separation of magnetic ores from the accompanying mineral matter.Magnetic Ore an overview ScienceDirect Topics
احصل على السعر
Intensity Magnetic Separation an overview ScienceDirect
Anshan type lean hematite ore, located in Anshan area of northeast China, is one of the mostly typical iron ores of super-large reserve. In the past, this low-grade iron ore was crushed and classified into coarse and fine fractions, with the coarse fraction reductively roasted and the fine fraction processed in a gravity-high-intensity magnetic separation with [16,17] on the beneficiation of iron-containing ore magnetic separation waste. 2. Materials and Methods The following material was used for research: iron concentrate from the Bapy mine (Kazakhstan) with 52 percent average iron grade, 2.65 g/cm3 quartzite and tailings— dry process waste of the same mine.Beneficiation of Magnetically Separated Iron-Containing Ore Waste
احصل على السعر
Iron Ore Magnetic Separation 911 Metallurgist
Iron Ore Magnetic Separation. In the West, capitalists have expended many millions of dollars developing the low-grade porphyry ores of copper. Half a dozen of these great enterprises have proved to be wonderful commercial successes. They have demanded improved crushing and concentrating machinery and consequently it has The results show that by only adopting traditional magnetization roasting–magnetic separation, an iron ore concentrate containing 57.49% Fe and 1.4% P2O5 at an iron recovery rate of 87.5% and a dephosphorization rate of 34.27% was produced, indicating that it is difficult to effectively dephosphorize and upgrade iron by A New Route to Upgrading the High-Phosphorus Oolitic Hematite Ore
احصل على السعر
Volumetric magnetic susceptibilities of iron minerals
Magnetic separation using wet high-intensity technique has become one of the most suitable methods for recovery of iron from low-grade ores, [3] due to its better separation efficiency as comparedA comparison of these sorting results with those of a wet drum magnetic separator at the same ore size, feed rate, magnetic field strength, and other factors reveals that the concentrate grade is 1.91 percentage points lower than that of the wet magnetic separation, but the concentrate recovery is 0.61 percentage points higher; therefore, Minerals Free Full-Text Dry Permanent Magnetic Separator:
احصل على السعر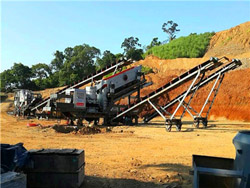
Maximizing the recovery of fine iron ore using magnetic separation
While flotation has a considerable capacity advantage over magnetic separation, the real advantage of magnetic separation over flotation in fine iron-ore beneficiation is that treatment of -10 µm iron ore is possible—in flotation, the feed is deslimed at 10 µm and the -10 µm stream is considered to be final tailings, even though there is often a significant The particle size of the titanium slag after wet-magnetic separation was smaller than that before wet-magnetic separation, which is due to further decrease in particle size caused by grinding in water during wet-magnetic separation. Metal iron particles were observed such as the areas marked by a in the micrograph of titanium High-Titanium Slag Preparation Process by Carbothermic
احصل على السعر
Increasing efficiency of iron ore magnetic separation by using
enhance efficiency of iron ore magnetic separation by applying ultrasonic technologies. Thus, it is required to combine research results in the following directions: theoretical and practical research into iron ore magnetic separation; methods and means of operative control over physical-mechanical and chemical-1. Introduction. The rapid depletion of high-grade iron ores, as well as the tremendous demand of iron and steel industries, has given rise to the urgent need for global attention on the effective utilization of refractory iron ore [1].In China, a large reserve of refractory iron ore lacks the appropriate treatment because of its properties such as low Mechanism for suspension magnetization roasting of iron ore
احصل على السعر
(PDF) Recovery of magnetite from dry crushed feed
The aim of this study is to examine the performance of wet drum magnetic separation on the recovery of magnetite from dry crushed feed. The steel industry has depended on iron (Fe) 6. Magnetic separation The concentrate collected from the middlings and tails after spiral gravity separation has a lower iron concentration (magnetite) so it must be further concentrated to achieve the customer’s 65% Fe concentration. It is immediately directed to a magnetic separator circuit.The six main steps of iron ore processing Multotec
احصل على السعر
Removal of Silica and Alumina as Impurities from Low-Grade Iron Ore
Iron ore was established and therefore this study concludes that; 1) Effective removal of impurities from Sanje ore using wet high-intensity magnetic separation requires lower feed pulp density of 2.5% and higher magnetic field intensity of 10,000 mT.This method can also be applied to reduce the silica content in magnetite concentrates obtained using wet low-intensity magnetic separation. Several studies describing the processing of iron ores(PDF) An overview of the beneficiation of iron ores via reverse
احصل على السعر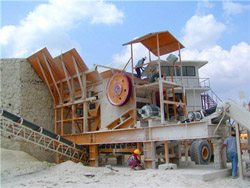
Developments in the physical separation of iron ore: magnetic
Abstract. This chapter introduces the principle of how low-grade iron ores are upgraded to high-quality iron ore concentrates by magnetic separation. Magnetite is the most magnetic of all the naturally occurring minerals on earth, so low-intensity magnetic separators are used to upgrade magnetite ores. On the other hand, because A recent work cites the coupled approach of reduction roasting and magnetic separation of a low-grade iron ore with 51.3wt% Fe, which produced an iron ore concentrate with 63.3wt% Fe at a recoveryOptimal Recovery of Iron Values from a Low Grade Iron Ore using
احصل على السعر
Minerals Free Full-Text Recovering Iron Concentrate from Low
Refractory iron ore is often discarded as tailings. This causes a great waste of iron resources. In this paper, the flash roasting-magnetic separation process was designed by combining the magnetic separation process of magnetite and the process mineralogy of iron tailings. The flash suspension roasting effects with 3–4 s roasting time As seen in Fig. 1, 95.31% Fe recovery ratio by magnetic separation of roasted ore at a grinding fineness of 90%–74 μm was obtained, implying that iron oxides in this raw ore could be successfully magnetized via reduction roasting using alkali lignin as reducing agent, however the Fe grade of iron concentrate was only increased from Development of roasting-acid leaching-magnetic separation
احصل على السعر- الطرق والجسور الصينية طاحونة
- أوروبا المتنقلة كسارات أوروبا المحمول كسارات الموردين و
- safety standards for admission to a processing plant
- التحقق من صحة دوت ويب محطم مفتاح
- پیچ شن و ماسه چرخ
- اسطوانات نقل الحركة معدات ثقيله
- flying saucer manufacturer
- معدات التكسيرللخرساته بالكمبروسر
- الجبس مصنع مسحوق الألمانية
- مضخة تغذية مضخة إزالة الألغام
- hammer grinding mill south africa for sale
- معدات منجم الذهب للبيع أيقونة استرداد الذهب
- مطحنة الفحم جوفاء
- ما الرمل المستخدم في صنع الزجاج
- crusher vibrating screen duckett frame manufacturers in chennai