اتصل
هاتف
+0086-371-86162511
عنوان
تشنغتشو ، الصين
ma speed of chinese batch ball mill

(PDF) Grinding in Ball Mills: Modeling and Process Control
The speed of rotation of the mill dete rmines three basic types of operation modes: slow rotation (cascading), fast rotation Here, we comprehensively compared the efficiencies of three batch ball mills employable for ultra-fine comminution of plant materials. First, we led a ball motion Evolution of grinding energy and particle size during dry ball
احصل على السعر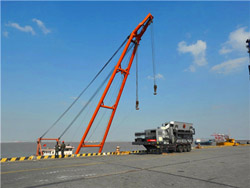
EFFECTS OF MILL ROTATIONAL SPEED ON THE BATCH GRINDING
increase of mill speed and optimum speed was not reached in the range of chosen mill speed fractions. Again the rate of breakage was plotted as a function of particle size, the The effect of time of grinding in a ball mill has been studied covering a range of 4 min to 32 min. 50 g of feed with size 0.475, 0.56 and 0.8 cm were fed to the Batch grinding studies by a ball mill for hematite ore
احصل على السعر
A direct approach of modeling batch grinding in ball mills using
The large mill runs at a much lower absolute speed than the small mill, even though the percent critical mill speed value is the same. For example, at 60% Five sets of the industrial ball milling survey data were used to validate the ball mill model. The data were acquired from four full scale ball mills covering primary A specific energy-based ball mill model: From batch grinding to
احصل على السعر
Ball mill load status identification method based on the
A ball mill is important grinding equipment in a concentrator, and the accurate detection of the load status ensures that the ball mill runs in the best state, Working speeds for the grinding kinetic tests. Dry batch milling kinetics tests were done in a lab-scale mill, 17.8 cm in diameter and 4.5 L in capacity, on a 600 Kinetics of Dry-Batch Grinding in a Laboratory-Scale Ball Mill of Sn
احصل على السعر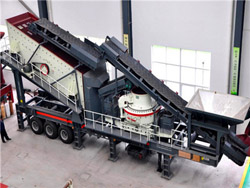
(PDF) A mechanistic model of batch grinding in ball mills
FIG 1 DEM simulations of a batch mill (0.3 m diameter, 0.3 m length, operating at 67 per cent of critical speed with 25 mm alloy steel balls at 30 per cent mill The study consists in terms of the following factors: Surface area, size distribution of the product & power consumption and the following parameters: Effect of Batch grinding studies by a ball mill for hematite ore
احصل على السعر
(PDF) A mechanistic model of batch grinding in ball mills
Batch grinding experiments have been conducted in a 0.3 by 0.3 m ball mill, operating dry at 67 per. cent of critical speed with 30 per cent fi lling of 25 mm steel balls and at 100 per cent ofThe batch mill grinding equation can be described as being developed with respect to a control volume defined around the batch mill. However the advent of ball mill charge motion simulation using(PDF) Ball Charge Dynamics in a Planetary Mill ResearchGate
احصل على السعر
What is a ball mill? LinkedIn
A ball mill is a type of grinder machine which uses steel or ceramic balls as grinding media, primarily for grinding materials into fine powder. It is widely used in production lines for powdersA video capture method has been used to study radial mixing kinetics in a dry batch ball mill. Other factors that affect mixing of particles in a ball mill are the mill speed [4], [17], grinding Pt/C half-potential of 841 mV vs RHE as well as an IrO 2-like OER activity with a potential of 1.69 V at 10 mA cm −2Radial mixing of particles in a dry batch ball mill ScienceDirect
احصل على السعر
Batch Grinding in Laboratory Ball Mills: Selection Function
The discharge end design of a ball mill plays an important role in discharging the desired particle sizes (−150 + 10 µm) and the percentage of recirculating load from the discharge end of theDownload Table Ball mill characteristics and test conditions Mill Diameter, D (cm) 20.4 Length, L (cm) 16.6 Volume, V (cm 3 ) 5,423 Operational speed, Ν (rpm) 66 from publicationBall mill characteristics and test conditions Mill Diameter, D
احصل على السعر
Optimization of processing parameters of a ball mill refiner for
Before experiments, working conditions were 70 rpm for as and 55 min for rt. The optimum conditions calculated by optimization were as follows: 58 rpm for as and 38.5 min for rt. The new working conditions identified for the ball mill considered enabled to rise output from 109 kg/h to 156 kg/h, with a 43% increase in productivity.In this study, we applied an eccentric stirring mill, which has been confirmed to be effective for the surface crushing of soil and ceramics and for the liberation of glass and resin from PV(PDF) Understanding production of fines in batch ball milling for mill
احصل على السعر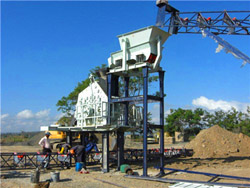
Ball Mill Principle, Construction, Working, and More Soln Pharma
Rotation speed of the cylinder. Working of Ball Mill: Several types of ball mills exist. They differ to an extent in their operating principle. They also differ in their maximum capacity of the milling shell, ranging from 0.010 liters for planetary ball mill, mixer mill, or vibration ball mill to several 100 liters for horizontal rolling ballWet Milling Batch Ball Mill for Milling Aluminium Oxide Material in Alumina Ball Producing Line FOB Price: US $2,250-70,000 / SET Min. Order: 1 SETChina Hydraulic Filter Press Manufacturer, Ball Mill, Slurry Blunger
احصل على السعر
Ball Mills Laboratory Grinding Mill Latest Price, Manufacturers
Mild steel 250 kg batch ball mill; Ball mill with charging conveyor; Mild steel ball mill mixer, 300 kg, capacity: This is a compact high speed vibrating ball mill for making small quantity of powder samples at easy and fast with improved MA Park, Sarkhej Road, Maktampura, Opposite Gujarat Agro Pump, Juhapura, Bakrol, Ahmedabad 380055Batch Small Ball Mill. 【 Maximum Charge 】 0.1-40 Tons/Time. 【 Max Feeding Size 】 <25mm. 【 Discharge Size 】0.075-0.4mm. 【 Motor Power 】2.2-132kW. 【 Scope of Application 】 Cement, silicate Batch Small Ball Mill JXSC Machine
احصل على السعر
(PDF) Grinding in Ball Mills: Modeling and Process
A ball mill is a type of grinder widely utilized in the process of mechanochemical catalytic degradation. It consists of one or more rotating cylinders partially filled with grinding balls (madeThe specific selection function effect on clinker grinding efficiency in a dry batch ball mill. Int. J. Miner. Process. (2008) Y. Chen retains capacity of 369.0 mA h g –1 after 500 cycles at 0.5 A g –1 in a noninflammable triethyl phosphate (TEP) electrolyte, and the volume expansion rate of productivity and processing speed.Evolution of grinding energy and particle size during dry ball
احصل على السعر
TCQ 1800x2100 ceramic batch ball mill for quartz silica grinding
Pictures of ceramic batch ball mill. Ceramic batch ball mill inside details. Alumina ceramic bricks and balls, normal Al2O3 content no less than 92%. 浙B2-20120091-4.increase of mill speed and optimum speed was not reached in the range of chosen mill speed fractions. Again the rate of breakage was plotted as a function of particle size, the optimum size was 0.8 mm when milling at 30% critical speed. As for 20% and 30% optimum size was not reached. The selection function parameters estimated atEFFECTS OF MILL ROTATIONAL SPEED ON THE BATCH GRINDING KINETICS OF
احصل على السعر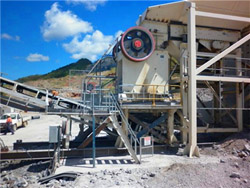
Batch Ball Mill-Ball mill-CLIRIK ultrafine grinding mill-industrial
Batch ball mill is also called ceramic ball mill, quartz, clay, ore, etc. Batch ball mill ( ceramic ball mill) is mainly used for mixing, milling of the ma. E-mail: sales@clirik. Call Us: +86-18917951321. HOME; ABOUT US. PRODUCTS. Powder Grinder; Ball mill; Raymond Roller Mill; Crusher; Rotate Speed (r/min) ReferenceThe investigations indicated a periodic increment of 0.2% weight of additives per hour in a batch ball mill increases the grinding efficiency when compared to one time dosage of 1% weight of additive.Batch grinding studies by a ball mill for hematite ore
احصل على السعر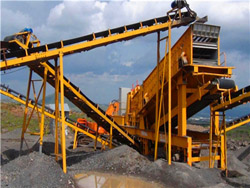
The kinetics and efficiency of batch ball grinding with cemented
The grinding conditions were as follows: the mill speed was 64% of the critical speed; the ball load was 30% of the mill volume; and the particle load was 100% of the interstitial The specific selection function effect on clinker grinding efficiency in a dry batch ball mill. Int. J. Miner. Process., 87 (2008), pp. 141-145. ViewMenéndez-Aguado et al. examined the possibility of determining the work index in a Denver laboratory batch ball mill with the same inner diameter as the Bond ball standard mill. The research was performed on the size class of 100% −3.35 mm using samples of gypsum, celestite, feldspar, clinker, limestone, fluorite, and copper slag.A Review of Alternative Procedures to the Bond Ball Mill Standard
احصل على السعر- feasibility of establishing stone crusher stone crusher machine
- كسارة فكوك ncrete
- تعويم جيمسون
- كيفية عمل أشكال كثيرة من الجبس
- line crusher and drying equipment
- الكسارات اليابانيه
- دیوانه چکش میلز
- الجبس السعر في تشيناي
- cement production process destroys
- معدات التعدين وفاصل التعدين توفير الطاقة آلة التعويم
- القبو الرمال المغذية صنع الآلات
- مضخة الملاط الأفقية بالطرد المركزي
- cost of a grinder in inr cost of a jaw crusher mining
- السيراميك المصنع خط إنتاج الرمل
- دستگاه خرد کن و خرد کن قابل حمل