اتصل
هاتف
+0086-371-86162511
عنوان
تشنغتشو ، الصين
flotation of metallic copper sand

A Review of the Flotation of Copper Minerals
The recovery of these copper minerals by flotation or hydrometallurgy from ores, typically containing 0.5%TCu (open pit The metallic minerals account for 6.27% of the total ore mass, with 94.44% of total cobalt existing in carrollite and 94.27% of total copper existing in Minerals Free Full-Text Flotation and Tailing Discarding
احصل على السعر
Mineralogical and morphological factors affecting the separation
A comparative study of flash smelting furnace (FSF) slag and its flotation products (concentrate and tailing) reveals the factors affecting the separation of copper Abstract. The aim of this study is to apply process mineralogy as a practical tool for further understanding and predicting the flotation kinetics of the copper Process mineralogy as a key factor affecting the flotation
احصل على السعر
Flotation of mixed copper oxide and sulphide minerals
This investigation has shown that using n-octyl hydroxamates (AM28 made by Ausmelt Limited) in conjunction with traditional sulphide collectors can successfully Flotation is a common method widely used to recover copper sulfide and metallic copper from CSS because of its low cost, short process, and excellent Mineralogical characteristics of copper smelting slag affecting the
احصل على السعر
A study of the effect of grinding environment on the flotation of
In the present study, the effect of various grinding conditions such as wet or dry grinding and addition of lime to the mill compared to the flotation cell on the The nature of copper slag flotation is unique due to the high temperature in the flotation pulp and high metallic copper content in the feed. Despite its great potential for valorizing slag, copper slag flotation remains challenging due to the deactivation of traditional dithiocarbonate (DTC) collectors (e.g., butyl xanthate) under high temperatures.A study of the effect of grinding environment on the flotation of
احصل على السعر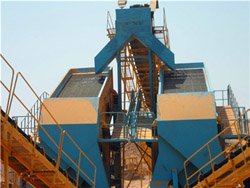
Copper recovery from copper slags through flotation
The ores are concentrated through froth flotation in the form of copper-sulfide or copper-iron-sulfide minerals (e.g. chalcopyrite, chalcocite and etc.), which are then melted in a high-temperature reheating furnace (± 1250 ℃). Under oxidation conditions, copper tends to form metallic copper and copper oxide [13].A Copper Flotation Flowsheet. Because the copper in this type of ore usually assays only plus or minus 1% copper, the porphyry copper operations must be relatively large in order to be commercial. Copper Flotation 911 Metallurgist
احصل على السعر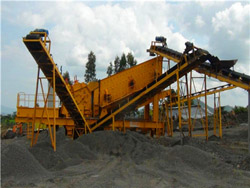
Mineralogy and Innovative Flash Flotation Separation of Cu-Pb
Pyrite in complex metallic ore is a widely distributed sulfide on earth, commonly associated with copper, lead, and zinc sulfides, as well as gold and silver [1,2].The production of separate concentrates from ores containing economic amounts of copper, lead, and zinc is complicated [], especially for ores with high pyrite content Today such ores (which would be regarded as relatively rich in copper) are scarce; the great majority of mines contain the metal in finely disseminated particles which aggregate anything from 2 percent down to 1 percent or even 0.8 percent of copper. Thus to obtain metallic copper, up to 99 percent of the material mined must be removed 60 Centuries of Copper: The Flotation Process
احصل على السعر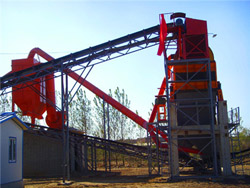
The recovery of copper, by flotation, from calcium-ferrite-based
The copper was present in the form of metallic copper, oxide copper and copper ferrite phases with the dominant phase in all slags being metallic copper. The slags were crushed, ground, wet screened at 210 or 75 μm to remove coarse metallic particles of copper, and floated at natural pH (about pH 11) using reagents and conditions Electrochemical control of metallic copper and chalcopyrite-xanthate flotation. Author links open overlay panel J.R. Roos, J.P. Celis, A.S. Sudarsono ∗1. Show more. Flotation tests carried out in a microflotation-electrochemical cell and in an electrochemical Denver cell demonstrated that maximum floatability is obtained whenElectrochemical control of metallic copper and chalcopyrite
احصل على السعر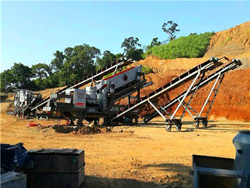
Flotation of gold and gold-bearing ores ScienceDirect
1. Background. The application of flotation on a reasonable scale within the gold-mining industry commenced in the early 1930s following the introduction of water-soluble flotation collectors (specifically xanthates and dithiophosphate collectors) that allowed differential flotation of sulfide minerals (Weinig and Carpenter, 1937; Rabone, It was found that controlled pulp potential (Eh) flotation is a prospective approach to promote the separation of arsenic-copper minerals from other copper sulphides due to the strong Eh dependence of arsenic minerals flotation (Menacho et al., 1993; Yen and Tajadod, 2000; Kantar, 2002; Guo and Yen, 2005; Senior et al., 2006; The flotation of metallic arsenic as a function of pH and pulp
احصل على السعر
1 Froth Flotation Fundamental Principles
After carrying out a froth flotation separation, the products are as shown in Table 1. Using this data, calculate: (a) Ratio of concentration (b) % Metal Recovery (c) % Metal Loss (d) % Weight Recovery, or % Yield (e) Enrichment Ratio Table 1: Grade/recovery performance of a hypothetical copper ore flotation process.This work proposes a process for copper recovery from PCBs by froth flotation and oxidation leaching. Copper grade is improved from 38.70% to 68.34% with the recovery of 88.76% by froth flotation, and froth flotation is significantly influenced by copper liberation and particles dispersion of PCB powders.Copper recovery from waste printed circuit boards by the flotation
احصل على السعر
(PDF) Flotation and Tailing Discarding of Copper Cobalt Sulfide
Flotation and Tailing Discarding of Copper Cobalt Sulfide Ores Based on the P rocess Mineralogy Characteristics Wentao Hu 1,2,3, *, Kai Tian 1,Zhengyang Zhang 4,Jiuchuan Guo 1,Xinwei Liu 5Introduction. Slags are a left-over of the pyrometallurgical stages of recovery of non-ferrous metals from sulfide materials. Production of 1 t of copper results on average in formation of 2.2 t of slag; the annual global output of copper-smelting slags is ~ 25 Mt (Gorai et al., 2003).Due to the absence of an accepted efficient technology for extraction Leaching of copper and zinc from copper converter slag flotation
احصل على السعر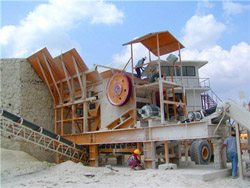
(PDF) Recovery of metal values from copper slags by flotation
The slags were crushed, ground, wet screened at 210 or 75 μm to remove coarse metallic particles of copper, and floated at natural pH (about pH 11) using reagents and conditions appropriate forFrequency changes of metallic minerals and Cu, Mo, and Fe grade in rougher flotation circuits of copper concentration plants Sungun complex. B) Cleaner flotation circuits: Based on the measured potential values for cleaner and re-cleaner circuits in phases 1 and 2 of the copper concentration plants, Eh values of cleaner cells of Oxidation-reduction effects in the flotation of copper sulfide
احصل على السعر
The Recovery of Copper from Smelting Slag by Flotation Process
Flotation Results. Figure 2 shows the effect of grinding fineness on recovery rate of copper. It is observed that a rise of the proportion of the grinding fineness of −0.074 mm from 60 to 80% obviously increased the copper recovery,then decreased when it exceeded 80%. This is because the initial appearance was dissociation fragmentationSulfide copper mineral, typically Chalcopyrite (CuFeS<sub>2</sub>), is one of the most common minerals for producing metallic copper via the pyrometallurgical process. Generally, flotation tailings are produced as a byproduct of flotation and still consist of un‒recovered copper. In addition, it is Development of copper recovery process from flotation tailings
احصل على السعر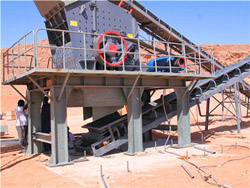
UTILIZATION OF FLOTATION IN COPPER EXTRACTION FROM
Natural copper is rare and represents about 1 % of all copper compounds. Copper may be present either in the form of sulphide ores, forming 90 % of copper compounds, or 9 % as oxidic ores [7]. The typical contents of copper in sulphide ores is 0.6 %, particularly primary sulphides (e.g. chalcopyrite and bornite) or secondaryIntroduction. Wet milling in ball mills followed by flotation is the general practice employed in the beneficiation of copper sulphide ores in which the major minerals of commercial significance typically are chalcopyrite (CuFeS 2), bornite (Cu 5 FeS 4), covellite (CuS) and chalcocite (Cu 2 S). The flotation response of ground minerals can A review of the effects of the grinding environment on the flotation
احصل على السعر
How to Recover Copper from Slag by Flotation 911 Metallurgist
Recovery of copper in concentrates from slags cooled in the induction furnace and ground for 30 minutes ranged from 87.1 to 96.2 percent with the best recovery obtained on the highest grade slag sample. Copper content of the flotation tailings, which is the most important indicator, ranged from 0.26 to 0.39 percent.
احصل على السعر- يطرح الكرة manufaturing نحاس macine
- مصنعي معدات التعدين السعودية
- والتعدين في الفلبين
- Concrete Block Making Machine Price List In Nigeria Price List
- محطم فحم الكوك تستخدم للبيع في الولايات المتحدة الأمريكية
- شركة الزاهد للتراكتورات والمعدات الثقيلة المحدودة لتوظيف
- كسارة حجر x في تركيا
- impact mill bahrain for sale
- منجم فحم بكس صور تحت الارض
- قطع غيار الكسارة للكسارة المتنقلة
- مطحنة الكرة سعة 15 رطل
- macam crusher plastil crusher for sale
- حجر المطحنة المحمولة
- متطلبات تصميم كسارة الصدم
- تاجر معدات تعدين الذهب في الإمارات العربية المتحدة