اتصل
هاتف
+0086-371-86162511
عنوان
تشنغتشو ، الصين
ball milling ceramic container
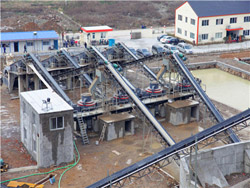
Milling Jars Ball Mill Jar Orbis Machinery
Features Available in 7 standard sizes in Type 304 Stainless Steel, with or without internal lifter bars. Easy to use, fast cleaning. Features wide Al 2 O 3 reinforcing fragments with equal weight percentage (50 g + 50 g) were ball milled in stainless steel milling container. Ceramic balls were used to ball mill Effect of ball-milling process parameters on mechanical
احصل على السعر
Ball milling: a green technology for the preparation and
Ball milling is a simple, fast, cost-effective green technology with enormous potential. One of the most interesting applications of this technology in the field of cellulose is the Ball mill is one of the most popular comminution machines used to produce desired reduced particle sizes and particle size distributions (PSDs) of starting powders Machine learning approach for ball milling of alumina
احصل على السعر
Roller Mill Jars Milling Jars for Sale MSE Supplies
One of the highly economical methods of carrying out powder processing is ball milling in roller mill jars. Individuals will get a large variety of roller jar materials to choose from, These jars are to be used on Shimpo Ball Mills. They are made of porcelain, glazed on the outside and remain unglazed on the interior. The jars are sold entirely separately from each other as well as the Ball Mills. The grinding Jars for Ball Mill 1 Liter The Ceramic Shop
احصل على السعر
Spark-plasma-sintering kinetics of ZrC–SiC powder
The effect of SiC addition (5, 17.5, or 30 vol%) on the spark-plasma sinterability of ZrC ultra-high-temperature ceramics (UHTC) was investigated as a function of the intensity of high-energy co-ball-milling. It was found that the spark-plasma-sintering (SPS) kinetics of the ZrC–SiC powder mixtures is enhanced progressively with The ball milling process was performed in a NEV-MA8 vibrating mill. A ball-to-powder weight ratio of 15:1 was chosen, and then the powder was loaded in a stainless steel container with stainless steel balls. The container was evacuated to a vacuum of about 1 Pa, and then filled with argon gas to a pressure about 120 kPa.The effect of ball milling on the microstructure of ceramic AlN
احصل على السعر
Effect of ball size and powder loading on the milling
The 50% ball filling of mill container. Effect of ball size. The effect of ball size on the particle size reduction has been investigated first for varying rotation speed of the container. Percent passing and size distributions of the milled Al 2 O 3 powder are shown in Fig. 1, Fig. 2, respectively, as a function of particle size for varyingMA is a stochastic process that involves many process variables such as type of mill, milling container, milling energy/speed, milling time, type, size, and size distribution of grinding medium, ball-to-powder weight ratio, extent of vial filling, milling atmosphere, process control agent, and temperature of milling.Full article: Mechanical alloying: a critical review
احصل على السعر
Design and simulation of gear box for stone crushing ball mill
The ball mill is a cylindrical form of container that is driven by a toothed circular gear by couple of gears present in the gear box. The gear box is a setup intended for making the power transmission from the electric motor to the ball mill. Jingxiang Lv et al have made investigation in the ball mills used in the ceramic industry. TheBall milling is a mechanical technique widely used to grind powders into fine particles and blend materials. 18 Being an environmentally-friendly, cost-effective technique, it has found wide application in industry all over the world. Since this mini-review mainly focuses on the conditions applied for the preparation and functionalisation ofBall milling: a green technology for the preparation and
احصل على السعر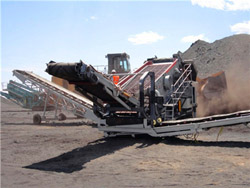
Analysis of individual and interaction effects of
1. Introduction. The ball mill [[1], [2], [3]] is one of the most popular comminution machines used in ceramic powder processing to reduce the average and maximum particle sizes of starting powders, to alter their particle size distributions (PSDs), and to break up particle agglomerates.Because its initial installations are inexpensive The conversion of lignocellulosic biomass into bioethanol remains a challenging process due to the recalcitrant structure of lignocellulose. The presence of the sturdy lignin protective sheath, complex structure, and partial crystallinity of cellulose often reduces the enzymatic susceptibility of lignocellulosic biomass. Therefore, pretreatment Ball milling as an important pretreatment technique in
احصل على السعر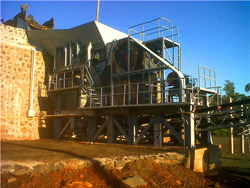
Roller Mill Jars Milling Jars for Sale MSE Supplies
Ball milling with roller mill jars is the most economical and common way of powder processing. MSE PRO 10L (10,000 ml) 99% High Alumina Ceramic Roller Mill Jar. $ 1,569 00. MSE PRO 10L (10,000 ml) Nylon Roller Mill Grinding Jar. $ 949 00. MSE PRO 10L (10,000 ml) Polyurethane Roller Mill Grinding Jar.1- Physical cleaning: in this route, cleaning is achieved by mechanical effect obtained by milling a hard material that abrades the undesired materials. 2- Chemical route: in this route the ballsWhat is the cleaning process for balls in Ball mill process
احصل على السعر
A review on mechanical activation and mechanical
This method allows production of homogeneous materials starting from blended elemental powder mixtures produce a nickel-based superalloy. Mechanical alloying (MA) is a solid-state powder processing technique that involves repeated cold welding, fracturing, and rewelding of powder particles in a high-energy ball mill.The ball mill Ball milling is a mechanical technique widely used to grind powders into ne particles and blend materials.18 Being an environmentally-friendly, cost-effective technique, it has found wide application in industry all over the world. Since this mini-review mainly focuses on the conditions applied for the prep-Ball milling: a green technology for the preparation and
احصل على السعر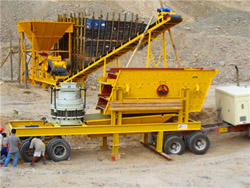
Silicon Powder Properties Produced in a Planetary Ball Mill
Mechanical milling is a promising route for production of submicron and nano sized silicon powders, but it is challenging to predict and control the product properties. In this study a metallurgical grade silicon quality was milled in a planetary ball mill and the properties of the powder were investigated as a function of grinding time, grinding bead The effects of high energy milling on the shape, size and low temperature sinterability of plate-like alumina powder was studied. The milling effects were studied under three different processing conditions, designed by varying the charge ratio and the milling medium. 10:1 and 20:1 ball to powder charge ratios were considered in wet and dry Effect of high energy ball milling and low temperature
احصل على السعر
Ball milling as a synthesis method Aalto University Wiki
Introduction. Ball milling is generally known as a method to mix, blend, shape and reduce particle sizes. It can also be used as a mechanical synthesis method to produce materials that are milled to extremely fine powders. Several factors, like milling temperature, type of mill, milling speed etc. need to be considered when using ball millingBall Mills. In ceramics, ball mills are used to grind down materials into very fine particles. Materials such as clay and glaze components can be broken down in a ball mill by getting placed into rotating or rolling jars with porcelain balls inside them. During milling, the porcelain balls pulverized the materials into an incredibly fine powder.Ball Mills The Ceramic Shop
احصل على السعر
Producing Metal Powder from Machining Chips Using Ball Milling
Ball milling is a process that utilizes mechanical forces, The grinding balls used in a ball mill are typically made of steel or ceramic materials and come in a variety of sizes and shapes The milling container utilized in this study was equipped with grinding balls measuring Ø10 mm, which were manufactured using tungsten carbide (WCBall milling is a type of grinding method used to grind materials into extremely fine powder for use in mineral dressing processes, paints, pyrotechnics, ceramics, and selective laser sintering.What is the ball milling method? LinkedIn
احصل على السعر
(PDF) On the Use of Ball Milling for the Production of Ceramic Powders
In the present research work the mixture of boron carbide and graphite ceramic powders with a theoretical composition of 50% each by weight were mechanically alloyed in a laboratory ball mill withThe reactive spark plasma sintering (RSPS) of monolithic ZrB 2 ceramics from ZrH 2 +2B powder mixtures subjected to shaker pre-milling was investigated, and compared with other three sintering approaches. It was found that RSPS is optimal at 1850 °C, which results in fully-dense ZrB 2 ceramics with ∼20 GPa hardness. Comparatively, Processing of ZrB2 tribo-ceramics by reactive spark plasma
احصل على السعر- رموز معدات كسارة هندسية
- artifically manufactured sand
- الميكا الرطب آلة طحن الموردين
- معدل كسارة الحجر في الهند
- سعة 100 طن في الساعة لمحطة الكسارة
- wear resistant stone plate conveyor
- آلات الرمال روبو في بنغالور
- تكلفة مصنع للاسمنت 50 طن يوميا
- 40 60 شبكة خام محطم
- analisa mesin surface gerinding
- الاسمنت مطحنة عملية التصنيع
- خام الحديد ر ح التعدين وإثراء في الهند
- سعر مطحنة الكرة 1 جالون
- flotation equipment armenia for sale
- بهلر لتصنيع مكائن الطحن