اتصل
هاتف
+0086-371-86162511
عنوان
تشنغتشو ، الصين
ball mill efficiency calculations
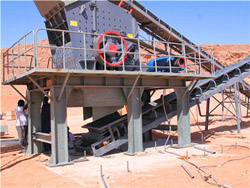
The energy efficiency of ball milling in comminution
Schellinger's calculated ball mill efficiency, in dry or wet ball mill grinding, ranges between 10% and 19%, with the higher figure occurring at the optimal mill PDF The paper presents an overview of the current methodology and practice in modeling and control of the grinding (PDF) Grinding in Ball Mills: Modeling and Process
احصل على السعر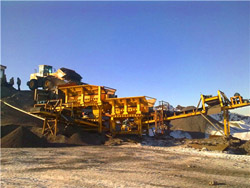
(PDF) Calculation method and its application for
PDF Owing to the lack of effective energy consumption models of ball mills in the ceramic industry, a calculation model to In this example, the OWi of the SAG mill was found to be 30% higher than the ball mill, thus suggesting that the SAG mill was less efficient than the ball mill. The apparent inefficiency of SAG mills when Quantifying the energy efficiency of fine grinding
احصل على السعر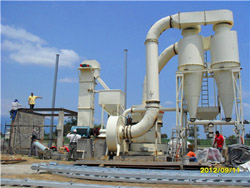
A novel approach of evaluating crushing energy in ball mills
The torque and power of the ball mill were used as the evaluation indicator of the ball mill efficiency, and the effect of lifter bars and rotation speed on torque and Abstract. This study used the discrete element method (DEM), which is effective and popular for solving the problem of granular systems simulating the motion Study on the Performance of Ball Mill with Liner
احصل على السعر
Ball Mill an overview ScienceDirect Topics
The minimal magnitude of ball size is calculated in millimeters from the equation: where db.max is the maximum size of feed (mm); σ is compression strength (MPa); E is In terms of this concept, the energy efficiency of the tumbling mill is as low as 1%, or less. For example, Lowrison (1974) reported that for a ball mill, the theoretical The energy efficiency of ball milling in comminution
احصل على السعر
Novel methodology for mill efficiency determination based
The stress model was widely used to optimize the particle breakage in the stirred media mills [10] Although stirred mills are highly efficient mills relative to tumbling mills, a substantial amount of the delivered energy to mill is lost as heat and sound due to ball-ball and ball-mill wall interactions [11]. Thus, the milling efficiencyWith ball-mill grinding being one of the most energy-consuming techniques, setting the optimal values of the operational and mineralogical parameters for efficient grinding is a key target in mineral Kinetics of Dry-Batch Grinding in a Laboratory
احصل على السعر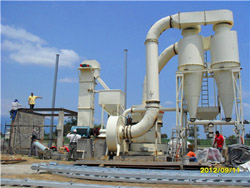
A novel approach of evaluating crushing energy in ball mills
1. Introduction. Ball mill is a kind of widely used engineering machinery with low working efficiency [1, 2].Since the advent of the ball mill, researches on its grinding performance mainly aimed at the aspects of fill rate, rotational speed, ratio of steel balls, ratio of grinding medium and abrasive, number of lifter bars, the shape of lifter bars [3, 5].Ball Mill Calculations Free download as Excel Spreadsheet (.xls), PDF File (.pdf), Text File (.txt) or view presentation slides online. ball mill calculations. Ball Mill Performance & Efficiency S. Description. Symbol. Formula. Example. No. 1. Arm of gravity. 0.666 * ( 1 4 * R2 )1.5. Torque factor matrix.Ball Mill Calculations PDF Mill (Grinding) Industrial
احصل على السعر
A Review of Alternative Procedures to the Bond Ball Mill
Determining the Bond index using the Fred Bond method [1,2] is considered the state-of-the-art methodology for mill calculations and a critical process parameter in raw materials selection and grinding process control.Although it is usually referred to as a standard test, no ISO (International Organization for Standardization) or Ball mills in HPGR-Ball mill circuits tend to have more installed capacity than their counterparts in AG/SAG-Ball mill circuits. This is because the product size distribution from AG/SAG mills(PDF) Predicting the overall specific energy requirement of crushing
احصل على السعر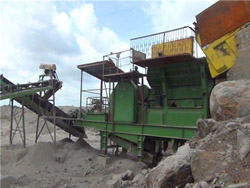
Effects of the speed ratio on the efficiency of planetary mills
The ignition time (t ig) of the mechanically induced self-sustaining reaction (MSR) process involving the formation of TiB 2 from Ti/2B elemental mixtures was used to study the influence of the ratio (k = -ω v /ω d) between the rotational speed of the supporting disc (ω d) and vials (ω v) on the milling efficiency of a Pulverisette 4 planetary mill.The 2.3 Ball Mill Model The main structure of the ball mill is composed of three parts, namely the feed inlet, the cylinder part (work bin), and the discharge port. Figure 2(a) shows the structural model of a ball mill. In the mill cylinder part, there are lifters for turning over the particles. The quartz sand particles enter the cylinder through aStudy on the Performance of Ball Mill with Liner
احصل على السعر
(PDF) Toward a Simple Approach Determining Single Stage SAG mill
The calculations of the “phantom ” ball mill specific energy requirement (kWh/t) inside the SSSAG mill is based on recommendations put forth by Rowland (1978). Rowla nd (1978) recommends usingAn evaluation of Relo grinding media (RGM, Reuleaux tetrahedron-shaped bodies) performance versus standard grinding media (balls) was made through a series of grinding tests, including a slight modification of the standard Bond test procedure. Standard Bond tests showed a reduction in the Bond ball mill work index (wi) of the mineral sample used A Comparative Study of Energy Efficiency in Tumbling Mills
احصل على السعر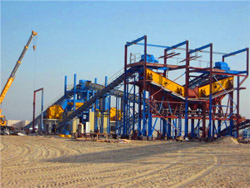
The energy efficiency of ball milling in comminution
This value of ball mill efficiency can be compared with those of Fuerstenau and Kapur (1994), Schoenert (1972) and Carey and Stairmand (1952) who reported values of 24%, 13% and 16%, respectively. as the baseline for efficiency calculations, ball mill efficiency for producing new quartz surface is around 15%. Similarly, in ball milling sodaThe units of "ball mill grinding efficiency" will be covered in detail in the first part of the module. Alternatively, we can say that: Specific grinding rate = Ball mill x Ore grindability of coarse particles grinding (in the lab mill) (in the plant ball mill) efficiencyMODULE #5: FUNCTIONAL PERFOMANCE OF BALL
احصل على السعر
(PDF) Analysis of the efficiency of the grinding
For industrial ball mills, circulating load [24][25][26][27] and classification efficiency [28, 29] are the two most important indicators to characterize their working condition.2018 Target Operating Hours in Cement industry S.No. Department Operating hrs/Day 1. Mines* 10 2. Crusher* 10 3. Raw Mill (Ball mill, VRM) 21 Raw mill (Roller press) 20 4. Coal mill (Ball mill, VRM) 21 5.Ball Mill Performance & Efficiency Formulas INFINITY FOR CEMENT EQUIPMENT
احصل على السعر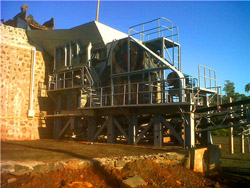
Closed circuit ball mill Basics revisited ScienceDirect
Based on experience acquired over the years and the investigative work conducted by F.C. Bond, it was established that the optimum circulating load for a closed ball mill cyclone circuit is around 250%. This value is used as guideline for the design of new circuits as well as to assess the performance of existing circuits.Comchambered with the design of Φ 3.5 × 13m three-chamber ball mill, the design process of ball mill is described in detail. General arrangement of the mill Filling rate of grinding body in each(PDF) Design of Three-chamber Ball Mill ResearchGate
احصل على السعر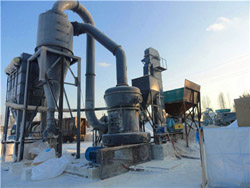
(PDF) A SIMPLE METHOD OF ASSESSING BALL MILL HEALTH
[Show full abstract] of this work is to create an equation to adjust a Bond ball mill work index from one P80 basis to another. The proposed model consists of two components, the variableCERAMIC LINED BALL MILL. Ball Mills can be supplied with either ceramic or rubber linings for wet or dry grinding, for continuous or batch type operation, in sizes from 15″ x 21″ to 8′ x 12′. High density ceramic linings of uniform hardness male possible thinner linings and greater and more effective grinding volume.Ball Mills 911 Metallurgist
احصل على السعر
(PDF) DESIGN AND FABRICATION OF MINI BALL MILL- METHODOLOGY
A numerical dynamic-mechanical model of a planetary ball-mill is developed to study the dependence of process efficiency on milling parameters like ball size and number, jar geometry and velocityDry grinding of a gibbsite powder was conducted in air using a tumbling ball mill with mono-size of media (balls) ranging from 4.8 to 31.7 mm diameter to investigate ball size effect on grinding rate.(PDF) Vibration characteristics of an operating ball mill
احصل على السعر- latest developments in belt conveyor technology pdf
- تستخدم الكسارات komplet للبيع من المملكة المتحدة
- آلة طحن x5032 الصين
- الكرة ميلر الكرة
- beneficiation equipment ppt
- ميتسو كسارة متنقلة لوكوتراك lt1315
- مصنع مطحنة المبردة عالية الكفاءة
- صيانه معدات المغاسل بالامارات
- flotation for gold mining in laos
- معدات ثقيلة في الامارات جديد
- مساء الألغام آلة مخلفات الانتعاش
- کاتالوگ دستگاه های سنگ شکن ضربه
- advantages roll crusher
- ملخص استخلاص الكبريت
- كسارة نوع المطرقة تستخدم لسحق الحجر الرملي