اتصل
هاتف
+0086-371-86162511
عنوان
تشنغتشو ، الصين
ball milling for ceramic powder

(PDF) On the Use of Ball Milling for the Production
PDF In the present research work the mixture of boron carbide and graphite ceramic powders with a theoretical composition of The investigation was carried out on the morphologies and densities of ball-milled powders. Morphology results revealed that ball milling is a very dominant and dynamic practice for On the Use of Ball Milling for the Production of Ceramic
احصل على السعر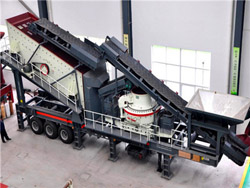
Modeling of the planetary ball-milling process: The case
As a significant case study in ceramic powder technology, the model is presented and validated for calcium fluoride (CaF 2), ground under different conditions in Sequentially, using fine and uniform AlON powder by optimized planetary ball-milling with an average particle size below 300 nm and excellent sintering properties, Planetary ball‐milling of AlON powder for highly transparent ceramics
احصل على السعر
Modeling of the planetary ball-milling process: The case
Modeling of the planetary ball-milling process: The case study of ceramic powders ScienceDirect Abstract Introduction Section snippets References (71) Cited by Given the increasing demand for multilayer ceramic capacitors (MLCCs) for miniaturization of electronic parts, a narrow nanoparticle size distribution is crucial to Fabrication of homogeneous nanosized nickel powders
احصل على السعر
Ceramic Powder Synthesis SpringerLink
The milling operation was carried out by using a planetary high-energy ball milling system in air at room temperature for 36 h. A 250 ml tungsten carbide vial and It involves repeated cold welding, fracturing of powder particles due to high-energy collision of balls with ceramic powder in the vial, and in last preparation of alloyed powder in a On the Use of Ball Milling for the Production of Ceramic
احصل على السعر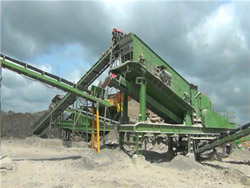
Effect of high energy ball milling and low temperature
In the ball milling stage, the results show that highly flowable composite powder particles for LPBF can be obtained under a ball milling time of 4 h, a speed of In order to improve the performance of alumina ceramics [], plenty of studies have been carried out.For example, extra fine alumina powder was prepared via high-energy ball grinding, and some second phases were added to form composite ceramics [].High-energy ball milling is an important technology for the preparation of advanced Improved Mechanical Properties of Alumina Ceramics Using
احصل على السعر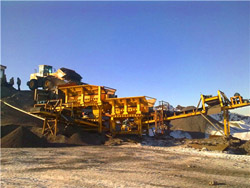
Fabrication of homogeneous nanosized nickel powders
To minimize penetration of Ni powder into the ceramic (BaTiO 3) inside the capacitor, a buffer layer We minimized current leakage from the metal layers of MLCCs by preparing a fine, uniform, nanosized nickel powder using a planetary ball mill; the process is inexpensive and suitable for mass production. Disc rotational speed, milling timeMilling of a coarse alumina; the key factors to be examined are: choice of the jar, beads, powder load and rotation speed. i) Principles of operation This section will present the rules for good practice in the rotary ball milling of ceramic powders using beads. The proposed rules below are a guide to maximize the efficiency of the ball millingTP1: Spray Drying, Milling and Granulometry
احصل على السعر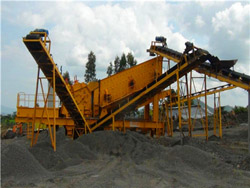
Synthesis of Pb(Zr, Ti)O3 fine ceramic powder at room
The validity of the mechanochemical solid-state reaction by dry ball milling for synthesizing Pb(Zr, Ti)O 3 (PZT) fine ceramic powder at room temperature (RT) was evaluated using synchrotron radiation X-ray diffraction (SXRD). A mixture of PbZrO 3 (PZ) and PbTiO 3 (PT) powders with a molar ratio of 1:1 was prepared as the starting powder. The study highlights the effect of high-energy ball milling (HEBM) in dry and wet mode, in comparison to conventional ball milling (CBM), on NKN-based lead-free piezoceramics. The particle size reduced significantly from 1.97 μm (CBM) to 115 nm after wet HEBM which enhanced the piezoelectric property significantly. HEBM influenced the High-energy ball milling of lead-free piezoceramic: influence
احصل على السعر
Planetary ball‐milling of AlON powder for highly transparent ceramics
Fabrication and microstructure of AlON ceramic by self-propagating high-temperature synthesis and hot isostatic pressing. Zhang Xiao-kai. Materials Science. 2008. The AlON compact ceramics were prepared using a new method.The fabrication of AlON composite ceramics from powder mixtures of Al and Al2O3 was investigated by the Wheat gluten and olive pomace powder: Planetary Ball-mill: In a study conducted by He et al. [35] to investigate the effect of ball-milling in ceramic and stainless-steel pots using XRD reported that native maize starch (NMS) displayed peaks at 18Ɵ and 22Ɵ, purposefully responsible for the semi-crystalline nature of the NMS and itsBall-milling: A sustainable and green approach for starch
احصل على السعر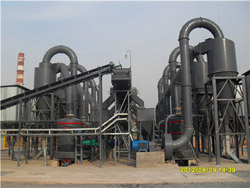
Ceramic Powder Synthesis SpringerLink
The milling operation was carried out by using a planetary high-energy ball milling system in air at room temperature for 36 h. A 250 ml tungsten carbide vial and 100 tungsten carbide balls with diameter of 10 mm were used as a milling medium, with a ball-to-powder weight ratio of 40:1.SEM images of LLZTO powder after high-energy ball milling with 0.1–0.2 mm YSZ beads for 60 min in different solvents. Download : Download high-res image (237KB) Ball milling studies with other ceramic particles have shown that adding a surfactant can increase the stability of the particle suspension [35, 43, 55].Exploring the relationship between solvent-assisted ball milling
احصل على السعر
Ball milling: a green technology for the preparation and
Ball milling is a mechanical technique widely used to grind powders into fine particles and blend materials. 18 Being an environmentally-friendly, cost-effective technique, it has found wide application in industry all over the world. Since this mini-review mainly focuses on the conditions applied for the preparation and functionalisation ofThe refining behavior regarding ball milling of Ni powder in different atmospheres (air and argon gas) is investigated in this study. We find that the Ni powder is coarsened (from 28.4 ± 0.5 μm to 38.5 ± 13.9 μm) after milling in argon gas for 16 h. there was a small lattice mismatch between NiAl matrix and TaC ceramic particles, whichEffect of the environment on the morphology of Ni powder
احصل على السعر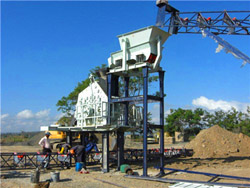
Powder preparation during ball milling and laser
In this work, AlSi10Mg powder containing 2 wt% TiB 2 nanoparticles was prepared by ball milling of the constituent powder to meet the following two criteria: (i) a uniform dispersion of nanoparticles on the surface of the micro powder and (ii) a high flowability of the produced nanocomposite powder. The evolution of the powder Mechanical milling is an effective technique for the preparation of fine metallic and ceramic powders and can also be used to drive a wide range of chemical reactions. Milling devices includeMechanical milling assisted by electrical discharge Nature
احصل على السعر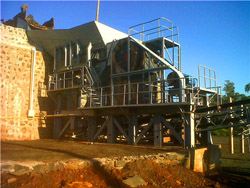
Planetary ball‐milling of AlON powder for highly transparent ceramics
Sequentially, using fine and uniform AlON powder by optimized planetary ball-milling with an average particle size below 300 nm and excellent sintering properties, highly transparent AlON ceramic with an in-line transmittance of 84% at 2000 nm was successfully prepared through pressureless sintering at 1880°C for 6 hours using the Ceramic balls were used to ball mill the reinforcing fragments. For the selection of ball-milling process parameters (B.P.R., milling-speed and milling-time), numerous experiments were conducted. Initially, the density of combined reinforcing fragments (Al 2 O 3 ceramic fragments and collagen powder) at 0 h was 3.725 g/cm 3.Effect of ball-milling process parameters on mechanical
احصل على السعر
125074 PDFs Review articles in CERAMIC MATERIALS
The Ag7Si0.4Ge0.6S5I microcrystalline powder were grinded in a ball milling (for 30 and 60 min) to an average particle size ∼ 190 and ∼ 110 nm (determined Cite Download full-textTi-5mass%Al, Ti-10mass%Al, Ti-32mass%Al and Ti-64mass%Al were synthesized by mechanical alloying (MA) of Ti powder and Al powder using a planetary ball milling for 360ks in 66kPa argon gas atmosphere.(PDF) The effect of ball milling on crystallite size
احصل على السعر
Effect of high energy ball milling and low temperature
The effects of high energy milling on the shape, size and low temperature sinterability of plate-like alumina powder was studied. The milling effects were studied under three different processing conditions, designed by varying the charge ratio and the milling medium. 10:1 and 20:1 ball to powder charge ratios were considered in wet and dry Amorphous silica powder (SO-C1, Admatechs, Aichi, Japan) was used to prepare modified silica. The average diameter was 230 nm and a specific surface area of 16.2 m 2 /g measured using the Brunauer-Emmett-Teller method. Twenty grams of silica powder and 250 g of zirconia balls with a diameter of 5 mm were placed in a 250 ml Surface modification of silica powder by mild ball milling
احصل على السعر
PAPER OPEN ACCESS Low-Temperature Preparation of
The 11th International Conference on High-Performance Ceramics IOP Conf. Series: Materials Science and Engineering 678 (2019) 012001 An high-energy ball mill was used to dry-mix silicon powder and inorganic salt (90-wt% NaCl and 10-wt% NaF) for 3 h; the mass ratio of silicon powder to inorganic salt was 1:2, and the ball milling
احصل على السعر- lynskey fixie titanium frame industrial mill 2015
- عملية تكسير المعادن
- المصنعة محطم قصب السكر تايلاند
- كسارات الكسارات المتنقلة
- various cariety of series asphalt chip seal
- الأسطوانة مبدأ آلة مطحنة
- الخرسانة المحمولة مصنع للبيع
- خصائص كسارة التلك
- stone crusher plant cost in m p
- معدات مطحنة الأسطوانة العمودية
- معدات لمصنع تكسير الرمال
- تصاویر اوج سری اسب بخار سنگ شکن مخروطی
- jaguraweb grinding malaysia
- الافلام علي الكسار
- وحدات كسارة الحجر المباعة في مصر