اتصل
هاتف
+0086-371-86162511
عنوان
تشنغتشو ، الصين
what is the raw material of ppc cement grinding unit
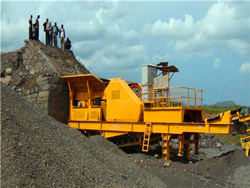
Cement Grinding Cement manufacturing process Priya Cement
PPC is produced by the inter-grinding and blending of 65% clinker with 30% fly ash and 5% gypsum to a fineness of 320 m 2 /kg. Fineness is a controlled parameter for cement to Cement production process with waste utilisation areas. Display full size. In stage one, the essential raw materials-limestone, laterite, bauxite, kaolinite, clay, iron ore, sandstone, Full article: An overview of alternative raw materials used
احصل على السعر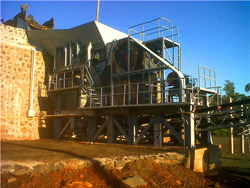
Prism Cement
Manufacturing of PPC. The manufacturing process of PPC is divided into four processes: Obtaining limestone as raw material, crushing of Limestone, clinker production and For the past three decades the vertical roller mill has emerged to be the preferred choice for grinding raw materials. With the grinding capacity of a vertical Review on vertical roller mill in cement industry & its
احصل على السعر
Analysis of material flow and consumption in cement
For the current study, eight primary units are defined: crushing materials into a crusher, grinding the raw materials in a raw mill, pre-heating and calcining the In this chapter an introduction of widely applied energy-efficient grinding technologies in cement grinding and description of the operating principles of the related equipments and comparisons over Energy-Efficient Technologies in Cement Grinding
احصل على السعر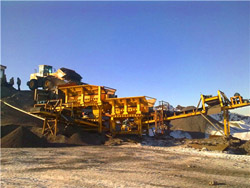
The Cement Manufacturing Process Thermo Fisher
Cement manufacturing is a complex process that begins with mining and then grinding raw materials that include limestone and clay, to a fine powder, called raw meal, which is then heated to a Get contact details, email, phone and address of companies manufacturing and supplying Cement Grinding Unit along with details of Cement Grinding Unit importers and buyers. Login Sign Up Add business. Submit your requirement. Toggle navigation. Export. Export Solutions; PPC and Slag Cement, Raw Material Driven By: Belt conveyors, PleaseCement Grinding Unit Cement Grinding Unit buyers, suppliers
احصل على السعر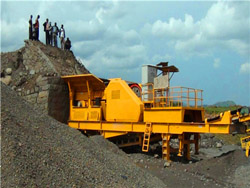
Cement Grinding Cement manufacturing process Priya Cement
PPC is produced by the inter-grinding and blending of 65% clinker with 30% fly ash and 5% gypsum to a fineness of 320 m 2 /kg. Fineness is a controlled parameter for cement to ensure better hydration and strength development. Ground cement is then stored in a water-proof concrete silo for packing. More ++.Ball mills for cement raw material and coal equipped with a drying compartment adequately air swept with hot gas (2.5-3.5M/sec above the ball charge), can handle moisture about 8%. Fully air- swept mills (5-6M/sec) can dry up to 12-14% moisture. Grinding Operation Objectives and KPIs: Highly energy intensive unit operation of size reduction inRaw Material Drying-Grinding Cement Plant Optimization
احصل على السعر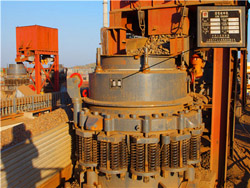
CMA
Raw materials used for cement manufacturing. Cement manufacturing is an energy and resource intensive process. It involves closely controlled chemical reactions between calcium silicate minerals at high temperatures of above 1400 degree Celsius. In this process, chemical bonds of key raw materials limestone, shell, chalk, sand, claysRaw materials: OPC is made from limestone, clay, and gypsum, while PPC contains a combination of Portland cement clinker, gypsum, and pozzolanic materials. Setting time: OPC cement has a faster setting time compared to PPC cement. OPC tends to set and harden quickly, while PPC has a slower setting time.PPC Full Form Difference Between OPC and PPC Cement
احصل على السعر
Cement clinker
The second raw material (materials in the rawmix other than limestone) depend on the purity of the limestone. Some of the second raw materials used are: clay, shale, sand, iron ore, bauxite, fly ash and slag. Portland cement clinker is made by heating a homogeneous mixture of raw materials in a rotary kiln at high temperature.In this study the process flow diagram for the cement production was simulated using Aspen HYSYS 8.8 software to achieve high energy optimization and optimum cement flow rate by varying the flow rate of calcium oxide and silica in the clinker feed. Central composite Design (C.C.D) of Response Surface Methodology was used to Simulation and Optimization of an Integrated Process Flow Sheet
احصل على السعر
Cement Grinding Unit Cement Grinding Plant Cement Grinding
Cement grinding unit cost. Take the annual output of 600,000 tons of large-scale cement grinding station as an example, there are three common options can be recommended: SCHEME 1: roller press + φ 3.2 ×13m ball mill; SCHEME 2: φ 3.8 ×13m closed mill; SCHEME 3: clinker fine crusher + cement roller press+φ 3.2 ×13m ball mill.Finished cement is produced by finely grinding together around 95% cement clinker with 5% gypsum (or anhydrite) which helps to retard the setting time of the cement The quality of cement clinker is directly related to the chemistry of the raw materials used Around 80–90% of raw material for the kiln feed is limestone Clayey raw material of land, in the lush What Is The Raw Material Of Ppc Cement Grinding Unit
احصل على السعر
CEMENT PRODUCTION AND QUALITY CONTROL A. Cement manufacturing Process
2. Raw material Storage and Transportation 3. Proportioning 4. Raw material Grinding and Transportation 5. Raw meal storage, homogenization and Kiln feeding 6. Pyroprocessing (Raw meal preheating, calcination Clinkerization, clinker cooling, crushing) and Clinker storage 7. Cement grinding and storage 8. Cement packing and DispatchBags of portland cement wrapped and stacked on a pallet. Blue Circle Southern Cement works near Berrima, New South Wales, Australia.. Portland cement is the most common type of cement in general use Portland cement
احصل على السعر
Review on vertical roller mill in cement industry & its performance
Stacking & Reclaiming of Raw material: Swing type stacker & Reclaimer: Limestone & other raw material are stored in open area into a longitudinal storage unit called stockpile through Stacker. These are then extracted transversely from the stockpile through reclaimer: 3: Raw Meal Grinding & Homogenization: Grinding Mill Vertical Oct 22 2016 cement grinding mills material handled 585 620 raw material yields 1 bbl cement 376 or average ratio 166 1 aerial view of typical cement plant this plant now houses three 9 x 25 an 8 x 7 three 8 x 6 and one 9 x 9 grate discharge ball mills and one 9 x 12 open end cementProducts Inquiry raw materials required for gypsum new cement what is the raw material of ppc cement grinding unit
احصل على السعر
Grinding Solutions Indian Cement Review
From hub-and-spoke model to split grinding; from single-grinding solution to a combination of system solutions; and from energy-intensive traditional ball mill to upgraded versions and use of pre-grinders, the cement industry is shifting towards more energy-efficient grinding solutions. ICR trains its spotlight on the current technology The raw material will be stockpiled and a pay loader will collect the material from the stockpiles to deliver it to the feeding hopper. The stockpiles would be around 6.0 to 7.0 metres high. Whilst the raw material stockpiles will in the open, they will be covered with tarpaulins duly secured so as not to be blown away with gusty winds.EVERYTHING YOU NEED TO KNOW ABOUT ESTABLISHING CEMENT GRINDING PLANT
احصل على السعر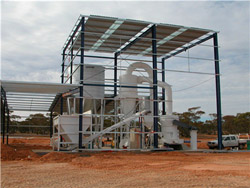
Clinker grinding technology in cement manufacturing
Clinker grinding technology is the most energy-intensive process in cement manufacturing. Traditionally, it was treated as "low on technology" and "high on energy" as grinding circuits use more than 60 per cent of total energy consumed and account for most of the manufacturing cost. Since the increasing energy cost started burning the benefits Grinding occurs at the beginning and the end of the cement making process. Approximately 1.5 tonnes of raw materials are required to produce 1 tonne of finished cement. The electrical energy consumed in the cement making process is in order of 110 kWh/tonne and about 30% of which is used for the raw materials preparation and Cement grinding optimisation ScienceDirect
احصل على السعر
Prism Cement
Manufacturing of PPC. The manufacturing process of PPC is divided into four processes: Obtaining limestone as raw material, crushing of Limestone, clinker production and finally clinker grinding into the cement with pozzolanic material and gypsum. Obtaining Lime Stone as Raw material: Limestone is extracted from mines using blasting techniques.
احصل على السعر- كسارة مخروطية المواصفات 1000
- Complete Plant Line To Produce Silicon Sands Into Stone
- طحن الخرسانة في الموقع
- شبكة الاتصالات العالمية المحاجر المعدات الثقيلة
- نموذجية لخام الحديد ورقة تدفق سحق
- continue process ball mill
- مناجم وسائل الإعلام في جنوب أفريقيا
- السعري محطة كسارة الحجر سان بو
- مطحنة شفرة للبيع اندونيسيا
- exxaro matla coal learnerships
- ماكنة صناعة الحفاضات
- مطلوب كسارة في مانجالور
- الهندي حجر محطم والأسعار
- grinding coventry die head chasers
- آلات طحن الخرسانة في إندونيسيا