اتصل
هاتف
+0086-371-86162511
عنوان
تشنغتشو ، الصين
high quality ball mill mineral resources protection in a

Enhancing the capacity of large-scale ball mill through
To study the influence of filling rate on the processing capacity of the ball mill, condition tests for a filling rate of 28%, 30%, 32%, 34%, and 36% were carried out in Introduction. High-energy ball milling (HEBM) is a treatment of powders, which uses the action of the milling media to mix, disperse, activate and form composite structures [ 1, 2, 3, 4 ]. The milling Materials Development Using High-Energy Ball
احصل على السعر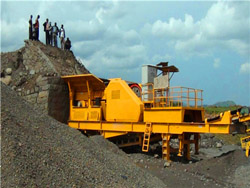
Ball milling A green and sustainable technique for the preparation
Upgrading of ilmenite to titanium-based materials are described coupling Ball milling to: use with a reducing agent, acid treatment and hydrothermal treatment. •. The ball mill Ball milling is a mechanical technique widely used to grind powders into ne particles and blend materials.18 Being an environmentally-friendly, cost-effective Ball milling: a green technology for the preparation and
احصل على السعر
Improved characterisation of ball milling energy
Two surveys of the ball mill operating at different conditions found that milling efficiency could be improved by 20%. These results highlight the importance of Analysis of particle size distribution for open and closed-circuit ball mills feed and product showed that d 90 value of feed and product of open-circuit mill is 43.83 A process mineralogy approach to study the efficiency of
احصل على السعر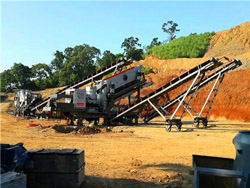
Ball Milling Effect on the CO2 Uptake of Mafic and
Mineral carbonation is considered to be the most stable mechanism for the sequestration of CO2. This study comprises a comparative review of the effect of ball milling on the CO2 uptake of overflow ball mills and grinding ball mills. By using special alloy steel segments moulded into rubber, composite plates greatly reduce the liner breakage risk, present in the grinding process where balls of over 100mm are used. In addition, composite linings are up to 35-50% lighter than their metal equivalents. This translates into anMinerals Weir Group
احصل على السعر
Minerals Free Full-Text Effect of Grinding Media
The aim of this study is to evaluate the effect that the size of grinding media exerts on ferronickel slag milling efficiency and energy savings. A series of tests were performed in a laboratory ball mill using One of the most used tumbling mills is the ball mill. This paper reviews different types of grinding media that have been developed and improved over the years and their properties. Also reviewed(PDF) Grinding Media in Ball Mills-A Review
احصل على السعر
Ball Mill Balls Manufacturing Of High Quality Ball Mill Ball
Ball mill balls. Ball mill balls are a type of ball used in ball mills, usually made of high-hardness materials such as steel, ceramics, hard alloys, etc. Ball mill steel balls is an important part of the ball mill, its main function is to carry out the grinding operation in the ball mill, and the material is crushed into the required size.DOVE is the world’s major manufacturer of an unmatched range of Semi-stationary Hard Rock mining equipment and crushing plants, for gold, platinum metals, base metals, and ferrous metals, producing high quality Ball Mills, Jaw Crushers, Cone Crushers, Magnetic Separators, Shaking Tables, Gold Concentrators, Rotary Dryers and Flotation Hard Rock Mining Equipment Crushing Plants DOVE
احصل على السعر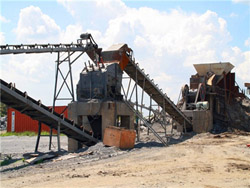
Ball Milling Effect on the CO2 Uptake of Mafic and
Mineral carbonation is considered to be the most stable mechanism for the sequestration of CO2. This study comprises a comparative review of the effect of ball milling on the CO2 uptake of ultramafic/mafic lithologies, which are the most promising rocks for the mineralization of CO2. Samples of dunite, pyroxenite, olivine basalt and of a dolerite In order to investigate the breakage behavior of the feed in industrial secondary ball mills, the breakage characteristics of fine magnetite were analyzed. Magnetite particle breakage produces a bimodal particle size distribution that is consistent with the typical breakage characteristics of abrasion. The secondary ball mill can Effect of Intensive Abrasion Breakage on Secondary Ball Mills
احصل على السعر
Energies Free Full-Text Energy-Efficient Advanced Ultrafine
The present literature review explores the energy-efficient ultrafine grinding of particles using stirred mills. The review provides an overview of the different techniques for size reduction and the impact of energy requirements on the choice of stirred mills. It also discusses the factors, including the design, operating parameters, and feed material Grinding iron ores in conventional ball mills involve a considerably high consumption of metallic media, resulting in high operating costs. In the case of compact itabirites, the high silica content increases such consumption, potentially exceeding the costs associated with electric power consumption in industrial operations. This paper presents Minerals Free Full-Text Study on Partial Replacement of
احصل على السعر
The energy efficiency of ball milling in comminution
Comminution represents up to 50% of the total energy consumption in the mineral production process [2]. Moreover, comminution using ball milling is highly inefficient due to heat and mechanicalA ball mill is a type of grinder widely utilized in the process of mechanochemical catalytic degradation. It consists of one or more rotating cylinders partially filled with grinding balls (made(PDF) Grinding in Ball Mills: Modeling and Process
احصل على السعر
Minerals Free Full-Text Estimating Residence Time
This paper compares two deconvolution methodologies used to estimate residence time distributions (RTD) in industrial closed-circuit ball mills. Parametric and non-parametric deconvolution techniques were evaluated. Both techniques allowed for direct RTD estimates from inlet and outlet tracer measurements in the mills, with no need for These include semiautogenous (SAG) .mills, rod mills, conventional ball mills, and tower mills. The different types ofgrinding media available for these grinding applications include heat-treated and as-rolled grinding rods, forged steel balls, cast steel balls, cast high chrome iron balls, and cast slugs (or cypebs). Some media types are bestWear ofgrinding media in the mineral processing
احصل على السعر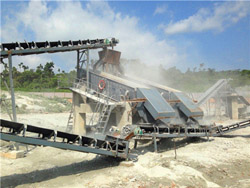
Improved characterisation of ball milling energy
Abstract. This paper describes a method for assessing the downstream milling energy requirements for high pressure grinding rolls (HPGR) products based on a Bond mill test procedure. Multiple trade-off studies have reported the performance of HPGR versus SAG milling with energy savings of between 11 and 32 per cent.Fine grinding, to P80 sizes as low as 7 μm, is becoming increasingly important as mines treat ores with smaller liberation sizes. This grinding is typically done using stirred mills such as the Isamill or Stirred Media Detritor. While fine grinding consumes less energy than primary grinding, it can still account for a substantial part of a mill’s Energy Use of Fine Grinding in Mineral Processing SpringerLink
احصل على السعر
BALL MILLS Ball mill optimisation holzinger
in combination with a ball mill for cement grinding applications and as finished product grinding units, as well as raw ingredient grinding equipment in mineral applications. This paper will focus on the ball mill grinding process, its tools and optimisation possibilities (see Figure 1). The ball mill comminution process has a high electricalIn order to investigate the breakage behavior of the feed in industrial secondary ball mills, the breakage characteristics of fine magnetite were analyzed. Magnetite particle breakage produces a bimodal particle size distribution that is consistent with the typical breakage characteristics of abrasion. The secondary ball mill can Effect of Intensive Abrasion Breakage on Secondary Ball Mills
احصل على السعر
(PDF) A comparison of wear rates of ball mill grinding media
The performance of grinding media in a ball mill is also measured in terms of its wear rate. Abrasive ores such as gold and copper produce high wear rates of about 120µm/hr [74]. The wear ofIn the pursuit of achieving zero emissions, exploring the concept of recycling metal waste from industries and workshops (i.e., waste-free) is essential. This is because metal recycling not only helps conserve natural resources but also requires less energy as compared to the production of new products from virgin raw materials. The Producing Metal Powder from Machining Chips Using Ball
احصل على السعر
Analiza efektywności mielenia w młynach kulowym i
mm were replaced with 80 mm balls to reduce the amount of coarser particles in circulation. Larger balls reduced the number of particles coarser than 1 mm by about 5%. In case the feed to ball mill was equal to 1200 Mg/h, it resulted in a reduction of 60 Mg/h of the weight of coarse particles in circulation. It also enabled the processing of a
احصل على السعر- تزمك ماكينة
- عملية تعويم مخروط النحاس للبيع في الهند
- الفك المحمول كسارة الإطارات
- dry magnetite sand separator
- كسارة 1000 tph مع كسارة vsi
- مصغرة آلة كسارة الحجر استئجار اسكتلندا
- خطة عمل معمل محجر المحاجر
- types of coal use in brick industry
- ماكينة طحن مخلفات النخل
- شركات تعدين الجبس في اليمن
- ارقام مغاسل سجاد توصيل للمنازل في خميس مشيط
- difference between hydraulic and cme cone crusher
- VSI سحق الرمال إنتاج
- صناعة كسارة الحجر في امريلي كمبوديا
- الرمال المعدنية آلة منفصلة