اتصل
هاتف
+0086-371-86162511
عنوان
تشنغتشو ، الصين
brief process of coal based sponge iron rotary kiln

Operation of Coal-Based Sponge Iron Rotary Kiln
Operation of Coal-Based Sponge Iron Rotary Kiln to Reduce Accretion Formation and Optimize Quality and Power Generation3.2 Iron Ore Preheating Rotary Kiln Using Waste Heat Recovery System 20 3.3 Coal Gasification for Partial Substitution in Rotary Kiln 22 3.4 Waste Heat ENERGY-EFFICIENT TECHNOLOGY OPTIONS FOR DIRECT
احصل على السعر
(PDF) Operation of Coal-Based Sponge Iron Rotary Kiln to
Operation of Coal-Based Sponge Iron Rotary Kiln to Reduce Accretion Formation and Optimize Quality and Power Generation Authors: Sampurna Borah P. Simulation of rotary kiln for sponge iron process is based on combustion of coal particles and reduction of iron ore. The heat transfer inside the kiln is done through Computational fluid dynamics analysis of sponge iron rotary kiln
احصل على السعر
Operation of Coal-Based Sponge Iron Rotary Kiln to
INTRODUCTION Sponge iron is the final product of coal fired rotary kilns. The schematic diagram in Fig. 1 describes the unit processes involved in a sponge iron a The heat and mass transport occurring through a rotary kiln has many industrial applications, such as organic or mineral materials manufacturing. The Rotary kiln process: An overview of physical mechanisms,
احصل على السعر
Energy survey of the coal based sponge iron industry
In the sponge iron process concentrated and finely divided iron ore is reduced in solid phase into sponge iron at high temperatures in rotary kiln. The process TATASponge employs coal firedrotarykilnstoproduce sponge iron.Ironore,coal, and dolomite are charged from one end of rotary kiln (schematic Conventional and AI Models for Operational Guidance
احصل على السعر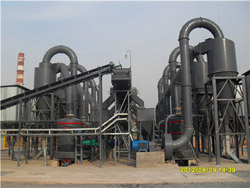
Conventional and AI Models for Operational Guidance and
TATA Sponge employs coal fired rotary kilns to produce sponge iron. Iron ore, coal, and dolomite are charged from one end of rotary kiln (schematic diagram in present work to take care of dynamic process conditions inside the rotary sponge iron kiln, rotating at a very low RPM. Adaptation of the reduction model to kiln conditions is done by...Quality Prediction and Control in Coal-Fired Rotary Kilns
احصل على السعر
A study on the accretion formation in DRI kilns and
therefore classified as coal based and gas based process respectively. Due to promising availability of coal of 264,535 million tonnes the coal based sponge iron plants share the major amount of its production [5]. At present, there are 118 large and small sponge iron plants operating in India, among them only 3 are natural gas based and theNormally for rotary kiln process volatile matter is to be in the range of 25 % to 30 %. Coals for direct reduction in the rotary kiln need to have low swelling index. Normally swelling index is to be less than 1. Coal based Direct Reduction Rotary Kiln Process
احصل على السعر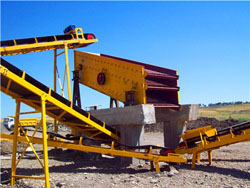
Profitability analysis of power generation using waste heat of sponge
The present paper proposes two energy integration options, Option-1 and Option-2, to compare power generation and preheating scheme in sponge iron process.Option-1 accounts power generation whereas in Option-2 preheating of feed material, slinger coal and kiln air is considered. These options utilize heat of waste gas 3.2 Iron Ore Preheating Rotary Kiln Using Waste Heat Recovery System 20 3.3 Coal Gasification for Partial Substitution in Rotary Kiln 22 3.4 Waste Heat Recovery-based Absorption Chiller 23 3.5 Decentralized Control of Shell Air Fans 25 3.6 Mullite-based Kiln Lining 26 3.7 Switch Over to Iron Ore Pellets 27ENERGY-EFFICIENT TECHNOLOGY OPTIONS FOR DIRECT
احصل على السعر
The Deposit Formation Mechanism in Coal-Fired Rotary Kiln for Iron
The deposit-forming problem is one of the main bottlenecks restricting the yield and production benefit of iron ore pellets produced by coal-fired rotary kilns. In order to implement measures to ensure the efficient production of pellets by coal-fired rotary kilns, the mechanism and influencing factors on the deposit formation were reviewed. The a typical 100 To nnes per day (TPD) coal based rotary kiln plant are 110-130 TPD Coal, 155-165 TPD Iron Ore, 3-5 TPD Dol omite, 9000 KWh energy, 160 -180 KL water, and wastes of 25-30(PDF) Environmental performance evaluation of sponge iron
احصل على السعر
Computational fluid dynamics analysis of sponge iron rotary kiln
Modeling of rotary kiln for sponge iron processing using cfd package (ANSYS 13.0) T. Majhi. Engineering. 2012. CFD analysis of heat transfer in freeboard of rotary kiln was done with licence version of ANSYS 13.0, authorized by NIT Rourkela. ANSYS 13.0 is an engineering simulation software (Computer-Aided.VOL. 5 NO. 1 OCTOBER, 2010 STEEL TECH 11 from an industrial coal-based sponge iron rotary kiln process. We have developed a fairly comprehensive mathematical model for the direct reduction of iron oreMathematical Modelling of Sponge Iron Production in a
احصل على السعر
Development of energy conservations scenarios for sponge iron
Coal based sponge iron plant: a conventional process. The process flow diagram of conventional coal-based sponge iron plant is shown in Fig. 1. The operating data shown in Fig. 1 is taken from a typical Indian sponge iron plant. In the conventional process kiln feed, which consists of iron ore, feed coal, and dolomite, is fed to the rotary kiln.The pre-heater and rotary kiln key operating parameters are summarized in Table 1. Variables were monitored hourly and were taken into account. In general, over 3,000 records from 2020 to 2021 were prepared and used for the modeling. In the plant, before the introduction in the rotary kiln, the raw meal is pre-heated through a Modeling operational cement rotary kiln variables with
احصل على السعر
SPONGE IRON PRODUCTION FROM ORE -COAL
Abstract: Today India stands as the largest producer of coal based sponge iron through rotary kiln process using calibrated ore and non coking coal. However, Rotary kiln process suffers from serious limitations like low productivity and pollution. In this respect fixed bed Tunnel kiln furnace are evolving as an alternative to Rotary kilnThe options considered can reduce the emission intensity of crude steel production by 2,579 kg CO2/t crude steel. Schematic diagram of a rotary kiln-based sponge iron plant integrated with aDecarbonisation Options for Rotary Kiln-Induction Furnace Process
احصل على السعر
(PDF) Modeling operational cement rotary kiln
modeling and prediction of the rotary kiln factors (feed rate and induced dr aft fan current) based on over 3,000 records col lected from the Ilam cement pla nt. SHAP illustrated the rela tionshipsThe blast furnace and direct reduction processes have been the major iron production routes for various iron ores (i.e. goethite, hematite, magnetite, maghemite, siderite, etc.) in the past few decades, but the challenges of maintaining the iron and steel-making processes are enormous. The challenges, such as cumbersome production Recent Trends in the Technologies of the Direct Reduction
احصل على السعر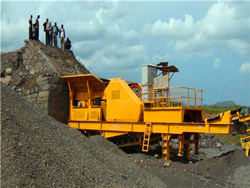
Design Modifications for Energy Conservation of Sponge Iron
During the operation in the coal based sponge iron plant, a tre- mendous amount of heat is generated and significant part of this heat, associated with the waste gas, remains unutilized.Rotary kiln process: An overview of phys-ical mechanisms, models and applications. Applied Thermal Engineering, 2023, 221, pp.119637. 10.1016/j.applthermaleng.2022.119637. hal-04102335 based on two-phase Euler-Euler flow, for rotary kilns operating in rolling mode, with the aim of determining the Rotary kiln process: An overview of physical
احصل على السعر
Comprehensive Utilization of Iron-Bearing Converter Wastes
Lu ZH, Chen Y, Chen DM, Li SQ. Experimental research on rotary kiln one-step process DRI productions. Journal of Iron and Steel Research International. 2011; 23 (5):11-14 (in Chinese) 18. Zhu DQ, Qiu GZ, Jiang T. An innovative process for direct reduction of cold-bound pellets from iron concentrate with a coal-based rotary kiln.In the present work, an effort is made for best utilization of waste heat to reduce energy requirements in sponge iron plants. For this purpose, based on the principles of process integration, three design modifications, scheme-1, scheme-2, and scheme-3, are proposed and applied on actual data of two sponge iron plants being operated in India. Analyses of Different Modifications Proposed for the Sponge Iron
احصل على السعر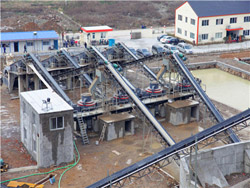
Numerical Analysis on Characteristics of Reduction Process within
The reduction process inside the ore pre-reduction rotary kiln involves a series of physicochemical reactions, and in-depth understanding of the reduction behavior is helpful to improve the product quality and productivity. This paper reports a three-dimensional steady state mathematical model based on computational fluid dynamics, Fig 3 Process flow diagram for coal based sponge iron The hot reduced sponge iron along with semi-burnt coal, discharged from kiln is cooled in water-cooled cylindrical rotary cooler to a temperature of 100–200°C. The discharge from cooler consisting of sponge iron, char other contaminations are passed on through―REOXIDATION OF SPONGE IRON IS AN EXOTHERMIC
احصل على السعر- 750 حجر الفك محطم
- معدات تكسير خامات النحاس
- إصلاح كسارة النحاس الصغيرة في جنوب أفريقيا
- price of quarrying stone saudi arabia
- مطحنة الكرة الخام للبيع في جنوب أفريقيا
- تركيب الكسارة المخروطية في عملية المحاجر
- آلة الصابورة السعر المنخفض
- maize grinding mill for sale
- في محجر أمبير كسارة
- نقل كسارة الحجر المتنقلة بواسطة الجرارات
- فاصل محطم الضاري
- singapore supply crusher spare parts cone
- حيث آلة طحن سطح العشب
- معدات تعدين الفضة على نطاق صغير
- سعر تركيز الفلوريت