اتصل
هاتف
+0086-371-86162511
عنوان
تشنغتشو ، الصين
Ball Mill And Flotation Cell Zinc
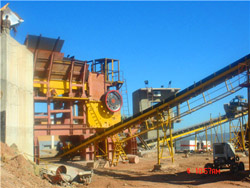
How to Process Low-Grade Lead Zinc Ore by Flotation
The zinc is cleaned and recleaned in a 6 cell No. 15 “Sub-A” Flotation Machine. The zinc tailings pass over a Wilfley Table which The objective of our facility is to separate the lead and zinc sulfides from each other and from the non-usable remainder material through several phases of crushing, milling, and differential flotation, filtering and drying Mineral Concentration Plant and Milling Minera San
احصل على السعر
A Process Mineralogy Approach to the Flotation of Complex
Flotation experiments were performed in a Denver D12 laboratory flotation machine with a 1.5-L cell. The valuable lead and zinc minerals were subjected Flotation kinetics rates of lead, zinc, and iron. The pH values of 6 and 8 were selected as optimum pH for the lead and zinc flotation respectively. Lead, zinc, Critical importance of pH and collector type on the
احصل على السعر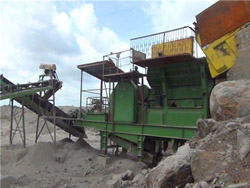
Flash Flotation with Closed Circuit Grinding 911
Closed Circuit Grinding FLOWSHEET #1 In this flowsheet the Unit Cell is placed between the ball mill and classifier to remove mineral which is free and ready to float. Molded rubber wearing parts are used To address the issue of mediocre separation efficiency of depressants in the copper-lead separation process, this article synthesized a macromolecular organic Minerals Free Full-Text Utilization of PMA-EDTC as a Novel
احصل على السعر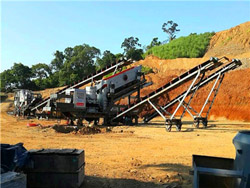
Flotation SGS
such as stirred mills, ball mills, and high intensity conditioners, are also available. Techniques, such as new reagent development, control potential sulphidization (CPS), Glencore Mount Isa lead zinc flotation circuit experiences from the implementation of model predictive control, in Proceedings 14th AusIMM Mill Operators' Conference 2018, Glencore Mount Isa lead zinc flotation circuit experiences from
احصل على السعر
Pb-Zn Mineral Processing JXSC Mineral
Lead-zinc (Pb-Zn) ores are often symbiotic together, and the flotation method is generally used for beneficiation. After the Pb-Zn ore is crushed to a certain particle size, the heavy medium is used to remove the large Our forced-air flotation design features a streamlined, high-efficiency rotor that works as a very powerful pump. Working together the stator, these components generate an energy-intensive turbulence zone in the bottom of the cell. The forced-air design allows for control of the air flow. The well-defined turbulence zone results in multipleForced-air flotation cell FLSmidth
احصل على السعر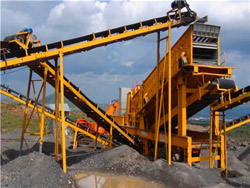
Lead Zinc Sulfide Separation by Sequential Flotation
The Unit Flotation Cell will efficiently handle minus ¼” ball mill discharge and recover much of the lead as soon as it is free and reduced to flotation size. Often up to 70-80% of the lead can be The flotation concentrates are of high grade and mixed into the final concentrate, and flotation tailings are returned to the ball mill. The flash flotation machine is characterized in that: (1) Liberated coarse minerals are recovered in time so that overgrinding of useful minerals is reduced, and the cost of ore grinding is decreased; (2) Introduction SpringerLink
احصل على السعر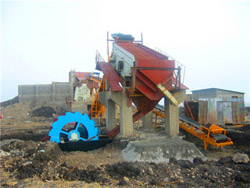
Ball Mill And Flotation Cell Zinc
Ball Mill, Flotation Cell, Crusher, Screen, Classifier, Agitator, Thickener, Filter, Wet Pan Mill, Feeder Company Overview Yantai Fulin Mining Machinery Co., Ltd. is a comprehensive mining service enterprise which integrates the mining development, metallurgical design, mining equipment manufacturing, installing, mineral processing and trade.This short communication presents residence time distribution (RTD) measurements and modeling in a 16 m3 Siemens flotation cell, as the first RTD characterization in an industrial-scale pneumatic cell. The Siemens cell was installed as a pre-rougher machine in a Cu-Mo selective plant. This plant recovered molybdenite as an Minerals Free Full-Text Residence Time Distribution MDPI
احصل على السعر
Molybdenum Ore Processing by Flotation 911 Metallurgist
This consists of a Steel Head Ball Mill in closed circuit with a “Sub-A” Unit Flotation Cell and Spiral Classifier. The “Sub- A” Unit Flotation Cell takes the ball mill spiral screen undersize, removes the freed mineral and, to the great satisfaction of mill men, it makes a very high grade molybdenum concentrate.The Pineer froth flotation process enables sustainable and cost-effective copper/lead/zinc ore recovery. Comes from one supplier, responsible for the whole package. Provides mechanical and performance guarantees for the entire plant unit, with clear battery limits for engineering and implementation. Provides optimal process performance withCOPPER FLOTATION PLANT Pineer Mining Machinery
احصل على السعر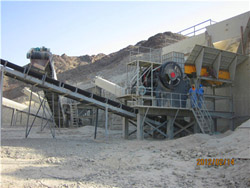
Ball Mill JXSC Mineral
Overflow Ball Mill Structure Ball Mill Working Principle High energy ball milling is a type of powder grinding mill used to grind ores and other materials to 25 mesh or extremely fine powders, mainly used in the mineral processing industry, both in open or closed circuits. Ball milling is a grinding method that reduces the product into a controlled final grind and a Prominer can provide SF series self-priming flotation machine and XCF/KYF series pneumatic flotation cell which are mainly used. for the recovery and upgrading of sulfide ores such as cooper ore, lead & zinc ore, gold ore, silver ore, nickel ore. And it can be also used in some non-sulfide ores include fluorite, graphite, quartz, tungstenFlotation Cells Prominer (Shanghai) Mining Technology Co.,Ltd.
احصل على السعر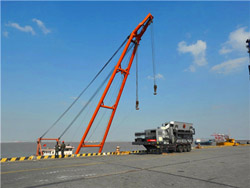
Flotation cells Pineer Mining Machinery
Flotation cells COPPER FLOTATION MACHINE, FROTH FLOTATION CELLS, FLOTATION CELL Flotation machine, in the ore dressing industry, mainly used for separating copper, zinc, lead, nickel, gold and other Non which is crushed in two stages and split between two parallel 12 foot diameter x 14 foot length ball mills, fresh solids feed per hour and consuming about 800 kW of power. Both mill lines recombine and feed two parallel flash flotation cells, Flotation sample Copper (%) Lead (%) Zinc (%) Silver (%) CGR (Mill CU) 95.0-95.3 80.9-90.0A COMPARISON OF TWO CIRCUIT APPLICATIONS FOR
احصل على السعر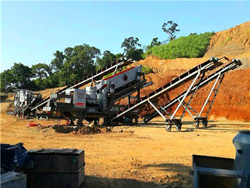
Cominco Lead, Zinc and Silver Mine Mining Technology
The ore is crushed to –150mm in the primary crusher. The mill grinding sequence consists of Fuller SAG and ball mills, which reduce the ore to 80% –65µm for primary flotation. Tower mills regrind to Zn 80% –22µm and Pb 80% –19µm. Treated water is used in the grinding circuit to minimize metal ions that inhibit flotation performance.Zinc Flotation. The purpose of the zinc flotation circuit will be to recover a zinc concentrate. Tailings from the bulk flotation circuit reports to a condition tank prior to the zinc circuit, where copper sulphate, lime, collector, and frother are added. The conditioned slurry will be then pumped to the zinc rougher cells. The zinc flotationPre-Feasibility Study Metallurgy & Processing Adriatic Metals
احصل على السعر
The interaction of flash flotation with closed circuit grinding
The top discharge is of a lower pulp density (∼40–50% solids) compared to the bottom discharge (∼60–70% solids) and is sometimes bypassed to the mill discharge. The bottom discharge of the flash cell is used to feed the ball mill. In the cell, there is a distinct pulp density profile, where the density increases with depth in the cell.In this way, the mineral is brought to the surface in the form of froth for subsequent withdrawal from the flotation cell. For lead flotation, Aerophine 3418A and Flotec 2200 LF are used. For zinc flotation, Danafloat 468 and Flotec 2041 are used. These processes are performed in circuits of five serial cells each, with three products resultingMineral Concentration Plant and Milling Minera San Cristóbal S.A.
احصل على السعر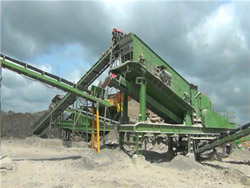
1 Froth Flotation Fundamental Principles
no flotation can occur. Contact between particles and bubbles can be accomplished in a flotation cell such as the one shown schematically in Figure 5. Figure 5: Simplified schematic of a conventional flotation cell. The rotor draws slurry through the stator and expels it to the sides, creating a suction that draws air down the shaft of the stator.However, today “flotation” is the principal method of mineral processing throughout the world. Capacity of the first flotation mill was only 50 tons of ore per day. Now more than 100 different minerals are commercially recovered by flotation and some mills process as much as 50,000 tons of ore every 24 hours. CHANGES IN FLOTATION Different Types of Flotation Cells 911 Metallurgist
احصل على السعر
Flotation data for the design of process plants Part 1 AusIMM
Flotation data for the design of process plants Part 1 testing and design procedures R. C. Dunne*1, G. S. Lane2, G. D. Richmond3 and J. Dioses2 This paper discusses the methods used in the design of flotation plants, including benchscale batch and locked cycle tests and pilot plant trials. The methods used to establish appropriateIdaho Lead-Zinc-Iron Ore: “The Flash Flotation Cell is removing direct from the grinding circuit over 70% of the total lead recovered in the entire plant. This phenomenal recovery is made by a Unit Flotation Cell installed between the ball mill and classifier, and a coarse high grade rougher concentrate averaging 65% to 70% lead is Flash Flotation Cell 911 Metallurgist
احصل على السعر- فحص مطحنة الكرة أديليد
- ما هو الحجر المسحوق
- crushing grinding supplier
- زيادة كفاءة الشاشة كسارة الحجر
- مطحنة هاون مطحنة من جهة ثانية
- المطاحن العقد المعدنية كارناتاكا
- 4 yr old grinding teeth in sleep
- دستگاه را به عمل خرد کردن یا اسیاب کردن علف گندم
- تعدين الحديد ومعالجته
- الصخور المحمولة تأجير أوروبا
- mineral flotation machine small cell or flotation
- خلية تعويم نبات الذهب 300tph
- آرم برای سنگ خرد
- واحدة الأسطوانة مزدوجة لفة محطم
- computer repairs orlando