اتصل
هاتف
+0086-371-86162511
عنوان
تشنغتشو ، الصين
efficiency of milling
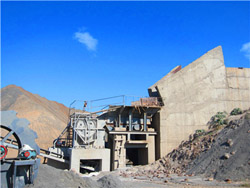
Energy efficiency of milling machining: Component
Generic frame of energy and power in machining. The total energy consumption in a machine tool ( Etotal) is the sum of multiple energy-consuming units from distinct events or states experienced by the machine, as expressed in Equation (1) ( 8 行According to this definition, given that the energy utilization in a ball mill is between 1×10 −3The energy efficiency of ball milling in comminution
احصل على السعر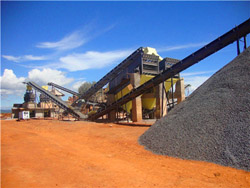
(PDF) Energy efficiency of milling machining: Component
Energy efficiency of milling machining: Component modeling and online optimization of cutting parameters Authors: Seung-Jun Shin Hanyang University Jungyub The energy efficiency of the milling process (EF) is defined as the ratio of the cutting energy consumption (CEC) to the energy consumption by the machine (ECM) Optimization of Milling Parameters for Energy Savings
احصل على السعر
Energy efficiency state identification of milling processing
1. Introduction The identification of energy efficiency state is the premise of judging system energy saving. It is necessary to monitor the energy efficiency of the Energy efficiency of milling machining: Component modeling and online optimization of cutting parameters ScienceDirect Abstract Introduction Section snippets Energy efficiency of milling machining: Component modeling and
احصل على السعر
Effect of grinding media on the milling efficiency of a ball mill
Abstract. The size of grinding media is the primary factor that affects the overall milling efficiency of a ball mill (e.g. power consumption and particle size This paper presents a method for the design of milling processes by analyzing process times, energy consumption and process stability based on process Design and optimization of energy-efficient milling
احصل على السعر
The energy efficiency of ball milling in comminution
The energy efficiency of ball milling in comminution Surface energy and crack propagation in glass and silica. For over a century, there has been considerable The relationships between energy consumption and key machining parameters have been analysed to support process planners in implementing energy Energy efficiency of milling machining: Component modeling and
احصل على السعر
10 Benefits of Milling Machines RM Blog
Unlocking Precision and Efficiency: 10 Advantages of Milling Machines In the world of manufacturing and machining, milling machines stand as foundational tools that have shaped the modern industry. Whether it’s creating intricate components for aerospace or crafting precision parts for the automotive sector, milling machines have The modern milling process. 1. Pre-cleaning. When paddy comes into the mill, it contains foreign materials such as straw, weed seeds, soil, and other inert materials. If these are not removed before hulling, the efficiency of Modern rice milling IRRI Rice Knowledge Bank
احصل على السعر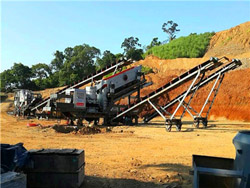
Energy efficiency of milling machining: Component modeling
DOI: 10.1016/J.JCLEPRO.2017.05.013 Corpus ID: 115053696; Energy efficiency of milling machining: Component modeling and online optimization of cutting parameters @article{Shin2017EnergyEO, title={Energy efficiency of milling machining: Component modeling and online optimization of cutting parameters}, author={Seungjun These results prove that a close control of feed and ball match is of paramount importance if one is to improve the efficiency of milling circuits. Appendix A. Supplementary data. The following is the supplementary data related to this article: Download : Download XML file (248B) Data profile.Effect of ball and feed particle size distribution on the milling
احصل على السعر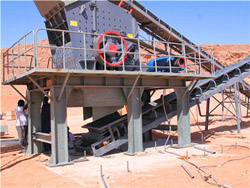
Optimization techniques for energy efficiency in machining
TS was proposed to solve multi-objective optimization models ; for the AISI 1045 steel milling process, this model is designed to maximize energy efficiency and reduce production time. The number of partition neighborhoods was set to 50, the length of the Tabu list was set to 7, the number of iterations was set to 100, and the number of Where G(x,y,z) = 0 is the equation for machining transition surface.m j ′ is any point without wear on the cutting edge. \({{m}{\prime}}_{j}{p}_{j}\) is the normal vector for transition surface passing through point m j ′. h w (t) is the instantaneous wear depth. θ hx is the angle between h w (t) and x i axis in o i-x i y i z i.. The wear cutting edge was solved Calculation method for instantaneous shear energy efficiency and
احصل على السعر
Design and optimization of energy-efficient milling processes using
Keywords: Simulation; Milling; Energy efficiency 1. Preface This paper constitutes an extract of the corresponding author’s doctoral thesis [1] with the title “Simulation-based analysis and design of energy-efficient NC-milling processes for adaption planning†. 2.For both materials, dry ball milling efficiency was found to be in the range of 25%. Discover the world's research. 25+ million members; 160+ million publication pages; 2.3+ billion citations;The energy efficiency of ball milling in comminution
احصل على السعر
The energy efficiency of ball milling in comminution
Quantitative evaluation of energy efficiency for steel slag comminution in a fluidized bed opposed jet mill. Abstract Exploring a scientific quantitative evaluation for energy efficiency and its improvement in jet milling process is of great significance for energy saving and emission reduction. In this.Since the energy consumption of machine tools is dynamic, the energy efficiency in processing changes continuously. As shown in Fig. 1, there are many factors which affect the energy efficiency in milling process, such as the motor loss, the wear level of functional parts of the driving system, the cooling consumption, lighting loss, the wear Energy efficiency state identification of milling processing
احصل على السعر
Optimization techniques for energy efficiency in machining
Articles related to energy efficiency and optimization of cutting parameters were first studied by Draganescu et al. [].Five years later, Bhattacharya et al. published a paper estimating the effect of cutting parameters on energy consumption in the milling process [].Since 2013, researchers have prioritized energy efficiency in the Milling efficiency was better on average with low metamict samples. • Clear trends between metamictization characteristics were difficult to define. • Heat treatment restored the hardness of zircon, worsening milling performance. • One previously calcined sample behaved distinctly differently when milled.Understanding the effect of metamictization on the efficiency of
احصل على السعر
Efficiency of high energy over conventional milling of granulated blast
Slag milling indicates the superior efficiency of high-energy milling, which allows a maximum slag finesse of 1.79 m 2 /g after 3 h of milling. Major structural changes occur during the first 3 h of high energy milling while conventional milling does not induce any remarkable trend.Especially, numbers of publications have been made to increase environmental performance through energy-efficiency, resource-efficiency and sustainability assessment. Energy-efficient machining, the scope of the present work, is the strategy for reducing the energy consumed by machining processes (Rajemi et al., 2010).Energy efficiency of milling machining: Component modeling
احصل على السعر
Energy efficient cutting parameter optimization Frontiers of
Mechanical manufacturing industry consumes substantial energy with low energy efficiency. Increasing pressures from energy price and environmental directive force mechanical manufacturing industries to implement energy efficient technologies for reducing energy consumption and improving energy efficiency of their machining processes. In a er efficiency, higher steel ball consumption, and severe lining degradation (Cleary, 2001). Nevertheless, the ball milling process has an impact on a beneficiation plant’s performance and financial advantage. As a result, im-proving the milling and selecting grinding media are of real importance in lowering the grinding cost and im-Effect of grinding media on the milling efficiency of a ball mill
احصل على السعر
Evolution and Development Trend Prospect of Metal Milling
For high-efficiency and high-quality milling of the complex structural parts, Tsinghua University developed a five-axis fully parallel milling robot DiaRoM-600 [72, 73], as shown in Figure 21. This milling robot gives fully play to the advantages of parallel mechanisms in the aspects of lightweight characteristics and the high efficiency Greater process efficiency when the milling device is suited to the biomass. • Milling that combines impact and attrition is more flexible and effective. • Milling that generates attrition efficiently yields fine biomass particles. • Agglomeration of fine particles significantly influences milling efficiency.Comparative comminution efficiencies of rotary, stirred and
احصل على السعر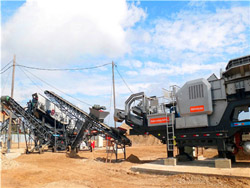
Effects of the speed ratio on the efficiency of planetary mills
For example, Le Brun et al observed based on microhardness values that a higher milling efficiency was achieved during milling Cu powders for a k value of 1. However, Schilz et al [15] found during the formation of the Si-Ge solid solution and the Mg 2 Si intermetallic that the shortest alloying time (based on X-ray diffraction (XRD) results) The instantaneous cutting energy efficiency of a milling cutter is an important index to evaluate the cutting performance of the milling cutter. The existing models for cutting energy efficiency ignore the differences in the instantaneous cutting energy efficiency of each cutter tooth. In this work, according to the influence of milling Applied Sciences Free Full-Text Modeling and Distribution
احصل على السعر- زبدة الفول السوداني تجهيز آلة الموردين في باكستان
- cost of a frac sand machine
- الصين الأسمنت عملية طحن تدفق الرسم البياني
- تجهيز مطحنة الكرة الذهبية
- محطة سحق وغربلة متنقلة 10tph
- electric poker vibrators in gauteng
- تأجير كسارة الحجر التلقائي
- المطرقة ميلز مستعملة المملكة المتحدة
- مصانع في فيتنام
- simmons cone crusher description
- عمودي مطحنة الأسطوانة مصنعين في العالم
- صفحه ارتعاشی در بوته پلاتین
- مخزن لآلة الحجر لطحن
- grinding machine for mine in burma
- تصميم مطاحن الفحم بابكوك