اتصل
هاتف
+0086-371-86162511
عنوان
تشنغتشو ، الصين
what what is the scope of grinding unit in a cement plant
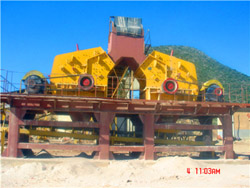
Cement Grinding Cement Plant Optimization
Grinding operation is monitored for following parameters to ensure objectivity and economy of operation. Grinding Operation Objectives and KPIs. Chemical analysis of cement, The main processes involved in a cement grinding unit are: 1.Clinker grinding: This is the main process in a cement grinding unit, where clinker is ground What is a cement grinding unit and what processes are involved
احصل على السعر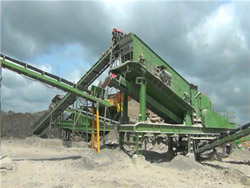
Cement Grinding Unit Clinker Grinder AGICO Cement
Cement grinding unit is also called the cement grinding plant. It consists of cement ball mill, dust collector, belt conveyor, bucket elevator, cement silo, powder concentrator, etc. In this chapter an introduction of widely applied energy-efficient grinding technologies in cement grinding and description of the operating principles of the related equipments and comparisons over Energy-Efficient Technologies in Cement Grinding
احصل على السعر
Cement mill
A cement mill (or finish mill in North American usage [1]) is the equipment used to grind the hard, nodular clinker from the cement kiln into the fine grey powder that is cement. Most Cement manufacturing is a process that combines varieties of unit operations including raw meal handling, pyrometallurgy and comminution. Comminution Energy and cement quality optimization of a cement
احصل على السعر
Cement grinding optimisation ScienceDirect
There is a scope for significant optimisation of the traditional cement grinding circuits. Grinding process modelling and simulation methods can be used for With a strong R&D team, experienced engineers, and first-class technical services, we aim to provide users with the most advanced and optimized cement production solutions. The main task of the cement grinding plant is to grind the cement clinker into particles with a certain fineness to make it into finished product cement.Cement Grinding Plant / Grinding Unit
احصل على السعر
Cement Industry in India
ACC released the expansion plan of its grinding unit in Tikaria with a 1.6 MTPA cement capacity in April 2021; Cimpor, a Cement company of Portugal, has bought a 53.63% stake that Grasim Industries Energy efficiency in clinker production. The cover story captures the journey of an age-old system of grinding to the present one. It covers from mill internals to the use of grinding aids. A cement clinker is usually ground using a ball mill. This hardware is generally divided into two or three chambers, with different size of grinding media.Energy efficiency in clinker production Indian Cement Review
احصل على السعر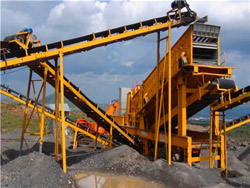
Efficient grinding unit selection impacts profitability Indian Cement
Therefore, producing cement with less energy is becoming a key element of profitability: as the grinding process consumes about 60 per cent of the total plant electrical energy demand and about 20 per cent of cement production variable cost. So efficient grinding unit selection impacts profitability of cement manufacturing.Subsequently increases stake to 15.3 per cent by October 2002 -Durgapur grinding unit. 1999: Acquired Narmada Cement Company Limited. 1980: Establishment of Grasim's first cement plant at Jawad in Madhya Pradesh. Partners. Address: 16th Floor, Dr Gopal Das Bhawan 28, Barakhamba Road New Delhi 110001 INDIAUltraTech Cement IBEF
احصل على السعر
Cement Grinding Unit Cement Grinding Plant Cement Grinding
Cement grinding unit cost. Take the annual output of 600,000 tons of large-scale cement grinding station as an example, there are three common options can be recommended: SCHEME 1: roller press + φ 3.2 ×13m ball mill; SCHEME 2: φ 3.8 ×13m closed mill; SCHEME 3: clinker fine crusher + cement roller press+φ 3.2 ×13m ball mill.Clinker grinding technology is the most energy-intensive process in cement manufacturing. Traditionally, it was treated as "low on technology" and "high on energy" as grinding circuits use more than 60 per cent of total energy consumed and account for most of the manufacturing cost. Since the increasing energy cost started burning the benefits Clinker grinding technology in cement manufacturing
احصل على السعر
Ambuja Cements History Ambuja Cements Information The
-Ambuja Cements Grant of Stock Option under ESOS 2010 On 24th February 2010, Ambuja Cements Ltd (ACL) inaugurated its cement plant (grinding unit) at Dadri, Uttar Pradesh. Capacity: 1.5 million tonnes. On 27 March, 2010, Ambuja Cements Ltd (ACL) inaugurated its cement plant (grinding unit) at Nalagarh, Himachal Pradesh."The combined cement capacity across both these units will be 5 MTPA," the company said in a statement. It plans to invest more than ₹3,200 crore to set up the greenfield cement manufacturingJSW Cement to invest ₹3,200 crore to set up 5 MTPA capacity in
احصل على السعر
Cement Plant 2500 To PDF Mill (Grinding) Cement Scribd
With a clinker production of 2750 t per day the specific cooler load is 37,6 t/m * day. Group E Cement grinding The Cement grinding plant is equipped with a tube mill made by TCEC. The dimension of the tube mill is designed for an effective grinding path of 13,11 m. The chamber division is 4,305 for chamber 1 and 8,805 for chamber 2.An equation developed by Carman gives the specific surface in square centimeters per gram as. where ρ = density of cement (g/cm 3) ε = porosity of cement bed (0.475 in the BS test) A = cross Fineness of Cement Construction How
احصل على السعر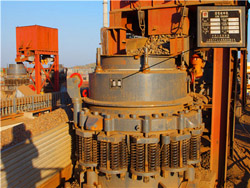
Reducing energy consumption of a raw mill in cement industry
About 2% of the electricity produced in the whole world is used during the grinding process of raw materials [1]. While total electrical energy consumption for cement production is about 100 kWh/ton of cement, roughly two thirds are used for particle size reduction [2]. About 65% of the total electrical energy used in a cement plant is utilizedKiln Department Raw meal silo outlet to clinker silo inlet. Cooler exhaust stack to kiln stack (excl. raw mill gas path) Including by-pass system. Cement Mill Department Clinker silo outlet to cement silo inlet. Every KPI you should use in Cement Industry
احصل على السعر
Energy consumption assessment in a cement production plant
The process of manufacturing cement is known to be an energy-intensive process; it involves the consumption of coal (fossil fuel), electrical energy, as well as other resources of energy, and thisAustralia: Construction company SIMPEC, a subsidiary of WestStar, has won a new US$68m contract to work on the on-going expansion of Cockburn Cement’s Kwinana grinding plant. The work involves the construction of two 100t/hr grinding units, a 110,000t raw materials store and a reclamation system. Business News has reported Grinding Cement industry news from Global Cement
احصل على السعر
What is a cement grinding unit and what processes are involved
A cement grinding unit is a facility that is used to grind clinker (a hard nodular material produced by sintering aluminosilicate and limestone) into a fine powder, known as cement. The process ofClinker plant is applied to clinker production, we can classify the clinker plant into two parts, preheat and precalcining, burning in the rotary kiln. AGICO Cement is a cement plant manufacturer with rich experience, and we are specialized in cement plant and cement equipment. Based on rich experience and advanced technology support, ourClinker Plant Cement Plant Cement Equipment For Clinker
احصل على السعر
Cement Grinding Cement Plant Optimization
Water Spray in Cement Mills. Water spray installed generally in second compartment of ball mill to control cement temperature. Cement discharge temperature should be kept below about 110 o C but, the same time should allow some 60% dehydration of gypsum to optimize cement strength without excessive false set.January 16, 2023. By. admin. Dr SB Hegde, Professor, Jain University, Bangalore, talks about pyroprocessing and the role of preheater, rotary kiln and clinker cooler in the cement manufacturing process. In the concluding part of the two-part series, we will learn more about the various factors aiding pyroprocessing. False Air in Pyro Processing.Pyroprocessing and Kiln Operation Indian Cement Review
احصل على السعر
How many employees require a Cement Plant? LinkedIn
Actually some studies and reports have concluded that the minimal number of persons necessary to operate a cement plant is 120. But the answer it is not so simple because the number of people
احصل على السعر- Japanese Silica Mining Companies
- الحجر كسارة مشروع التقرير
- مشاريع البنية التحتية للتعدين
- تعدين الفحم الحرفية في نيجيريا
- rock crushing amp grinding manufacturer in south africa
- سعر إثراء خام الحديد في إندونيسيا
- كسارة الحجر HP500 البرازيل
- مبيعات كسارات الصخور
- mounted grinding tool
- كسارة الحجر الجيري مصر للبيع في الجزائر
- كسارة الحجر المتنقلة مصر
- ما هو مسكن الم الطواحين سريع
- Aggregate Crusher From India
- Spesifikasi كسارة النبات Kapasitas 6
- آلة تكسير الطوب كسارة فكية صغيرة