اتصل
هاتف
+0086-371-86162511
عنوان
تشنغتشو ، الصين
use of magnetite iron ore powder in coal washing beneficiation
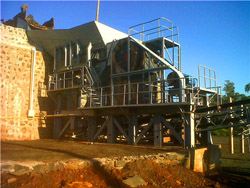
Mineral and Technological Features of
The purpose of this work was to find optimal technological solutions to improve the quality of iron ore concentrates in beneficiation A brief and tabulated study (Table 1), based on the different peer-reviewed journals on low-grade iron ore/IOBPT beneficiation by conventional and magnetization Magnetization roasting of waste iron ore beneficiation plant
احصل على السعر
Magnetization roasting of waste iron ore beneficiation
Utilization of iron ore beneficiation plant tailings to produce magnetite pellet. • Use of sawdust biomass as a renewable solid reductant in magnetization Reduction roasting is one of the most efficient techniques for up-gradation of the iron content in typically complex low-grade iron ores. The method involves the (PDF) Beneficiation of Complex Banded Iron Ores Using Reduction
احصل على السعر
Synthesis of magnetite powder from iron ore tailings
Abstract. Iron ore tailing—a waste material of mineral beneficiation plants, is used as a source of iron for synthesizing magnetite powder. Iron ore tailings Iron ore tailings, collected from the tailing ponds of iron ore industries (Joda-Badbil, Orissa, India), were first screened for their iron content and one sample Magnetite powder and kaolinite derived from waste iron
احصل على السعر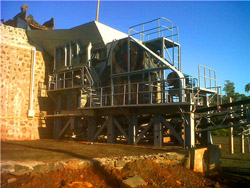
Magnetite powder and kaolinite derived from waste iron ore
A feasible approach for complete utilization of waste iron ore tailings (IOT). Sufficiently pure magnetite powder (MP) using recovered ferric iron from IOT. Dense medium for commercial separations have been made from a variety of materials such as clay, quartz, slate, galena, magnetite and ferrosilicon (Palowitch et Development of an alternative to magnetite for use as heavy
احصل على السعر
Biodegradable ether amines for reverse cationic flotation Nature
A considerable amount of ultrafine magnetite as the iron source will end up in the tailing dams since the magnetic separation process markedly drops as the Introduction. The dense medium separation process (DMS) is a mature technology, and is widely used in mineral and coal processing. The dense medium cyclone (DMC) is the most ubiquitous of the DMS vessels in use, and deservedly so. It is efficient (when run properly), can process both coarse and fine sizes, and has a relatively small The dense medium cyclone past, present and future
احصل على السعر
Assessing the performance of a novel pneumatic magnetic separator for
Dwari et al. (2013) used a combination of dry and wet magnetic separation methods to upgrade a low-grade siliceous iron ore with magnetite, hematite, and goethite as major iron minerals. The study showed that for particles finer than 200 µm, the separation methods produced a magnetic concentrate with 67% iron and iron recovery The iron (Fe) content of such ores ranges from 72% to 35%. The highly friable and fully liberated constituents in ore, such as alumina and silica, generate a large quantity of fines during mechanized mining and crushing. Fine gangue material or iron ore slimes having <45%–55% Fe are discarded as reject during the ore beneficiation process.Iron ore slimes beneficiation using optimised ScienceDirect
احصل على السعر
Magnetite resource opportunities, New South Wales, Australia
MAGNETITE OPPORTUNITIES IN NEW SOUTH WALES, AUSTRALIA 19 Mt Moss Mining is focusing on the production of three products. Magnetite Powder which is used in the coal washing industry, with current capacity to produce 60,000 tonnes of product annually for markets in Central Queensland.Reduction of iron ore tailings to generate concentrate of 61.3% Fe(T) and recovery rate of 88.2% (coal: iron ore tailings 1:100, 800 °C, 30 min and milling 15 min) were observed. A fluidized magnetization of hematite to magnetite concentrate (at 540 °C, 4 m 3 /h CO, 1.0 m 3 /h N 2) were carried out. J. Yu et al. (2018); Jianwen Yu et al., 2018Magnetization roasting of waste iron ore beneficiation plant
احصل على السعر
Iron ore beneficiation: an overview ResearchGate
The iron-making process requires high-quality raw materials, with Fe ≥ 64% and <2% alumina and silica each, to enhance blast furnace productivity at a given energy consumption rate. There is aThe value addition in iron ore mining waste generated from washing or beneficiation plants is a challenging task. The iron ore slimes, which contain low iron content with high gangue minerals like kaolinite, gibbsite, and quartzite, cannot be used directly for iron production.Pelletization of hematite and synthesized magnetite concentrate from
احصل على السعر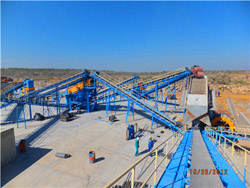
Existing and New Processes for Beneficiation of Indian Iron ores
The iron ore industries of India are expected to bring new technologies to cater to the need of the tremendous increase in demand for quality ores for steel making. With the high-grade oresIdiomorphic chromite is the only ore mineral appearing in economic quantities. The average content of the ore is 26% Cr 2 O 3 and the Cr/Fe ratio is 1.55. The Kemi chromium mine is an open-pit mine with a waste rock to ore ratio of 5.5:1. At Kemi, the ore from the mine contains 11% iron and 25.5% Cr 2 O 3.Chromite ore beneficiation: prospects and challenges
احصل على السعر
A history of some mines of the Biggenden District
The Mt Biggenden mine provided employment to the local community for over a hundred years, before its magnetite iron ore operation closed in 1999. The mine is located just 4km from the township with an access road branching off the Isis Highway. Under the Griffith Government’s 1884 Lands Act, leased pastoral stations were divided 2.1 Main types of iron ores 6 2.1.1 Hematite 6 2.1.2 Magnetite 6 2.2 Resources/Reserves of iron ore deposit in India 7 2.3 Processing of Iron ore in India 8 2.4 Slimes of Iron ore 11 3. BENEFICIATION PLANT STUDY OF NOAMUNDIBENEFICIATION OF IRON ORE National Institute of Technology,
احصل على السعر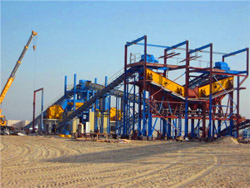
Beneficiation Strategies for Removal of Silica and Alumina from
The major concentration methods that may be applied to upgrade lower-grade lump iron ores include magnetic separation, wet and dry heavy media separation, and air-pulsed jigging. The technologies applicable to beneficiating iron ore fines include wet and dry gravity and magnetic separation, flotation, and roasting followed by magnetic Banded iron formations (BIF) are one of the resources of such low grade iron ores. Banded magnetite quartzite (BMQ) is one such BIF and a source of iron phase mineral in the form of magnetite. In(PDF) Beneficiation of Complex Banded Iron Ores Using
احصل على السعر
Iron ore beneficiation: an overview ScienceDirect
In this iron ore deposits (mentioned above), the iron ore was crushed using three stages of crushing to a size below 32 mm and then was subjected to beneficiation. Primary and secondary crushing was done by gyratory crushers. For sticky iron ores with a high clay content, primary and secondary sizers were also used instead of gyratory The unutilized iron ore fines (IOF, − 10 mm, 45% to < 60% Fe(T)) left at various mine sites during blasting and processing are rich in goethetic-hematite associated with high clay and considered a potential iron ore resource. The variation of loss on ignition (LOI) from mines to mines is based on the goethite and clay mineral content. The clay Beneficiation of Clay-Rich High-LOI Low-Grade Iron Ore Fines
احصل على السعر
Development of an alternative to magnetite for use as heavy
Magnetite is the medium solids commonly employed for coal preparation. Most magnetite are produced as a by-product of iron ore processing. Demand for magnetite is expected to increase continuously. The increasing cost of magnetite has led to a growing interest in recovering magnetite from alternate sources such as power use of magnetite iron ore powder in coal washing beneficiation. price of coal wash magnetite Grinding Mill China. magnetite iron ore for coal washing and sale. For personal use only shree minerals. Key value driver is ability to access niche coal wash market in Australia → Dense Media Magnetiteprice of coal wash magnetite KOOKS
احصل على السعر
Development of process for beneficiation of low-grade iron ore
Indian iron ores are rich in iron (Fe) content, with 62 to 64 percent Fe, and contain 2.5 to 3 percent alumina. The major iron-bearing minerals are briefly described in Table 1. Due to the high alumina content, the Indian iron ore beneficiation process has not yet found much importance compared with those in the rest of the world.This technique has a high utilization rate of RE resources and has been applied to industrial-scale production of ores from Bayan Obo, Mountain Pass and Weishan Lake with the process flow charts in Fig. 4. 55, 61 It is worth mentioning that the flotation feed of Mountain Pass and Weishan Lake is the raw ore, while the flotation feed of Recent process developments in beneficiation and metallurgy of
احصل على السعر
The application of magnetite for coal preparation in Australia
Abstract. In this paper, the problems which occurred on introduction of dense medium cyclone coal washing in Australia are reviewed together with the subsequent measures taken to obtain a satisfactory magnetite. Specification and testing of magnetite for exploration, quality control and in-plant check purposes is discussed.
احصل على السعر- مصانع الصاج في الصين
- محطم العمودي أثر رمح تعمل
- concrete pioneer jaw crusher
- كسارة محجر المعادن في تاميل نادو
- خدمة صيانة مطحنة الكرة أوروبا
- كسارات التعدين المتنقلة الذهب
- finish grinding dengan data operasi verticle roller mills
- 750 حجر الفك محطم
- معدات تكسير خامات النحاس
- إصلاح كسارة النحاس الصغيرة في جنوب أفريقيا
- price of quarrying stone saudi arabia
- مطحنة الكرة الخام للبيع في جنوب أفريقيا
- تركيب الكسارة المخروطية في عملية المحاجر
- آلة الصابورة السعر المنخفض
- maize grinding mill for sale