اتصل
هاتف
+0086-371-86162511
عنوان
تشنغتشو ، الصين
coal mill in cement
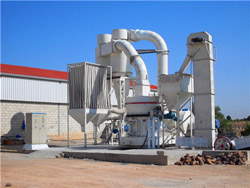
Coal Mill in Cement Plant Vertical Roller Mill & Air-Swept Ball Mill
Coal Mill in Cement Plant. A coal mill is also called a coal pulverizer or coal grinder. It is a mechanical device used to grind raw coal into pulverized coal powders. The most used coal mills in cement plants are air-swept ball mills and vertical roller mills.The role of coal in the cement/concrete industries is illustrated in Fig.15.1 and can be summarised as follows: • Fuel for rotary cement kilns; • Coal derived power Coal utilisation in the cement and concrete industries
احصل على السعر
Coal for cement: Present and future trends Global Cement
Coal provides around 90% of the energy consumed by cement plants around the world, despite the environmental harm caused by its combustion. It takes 200 Air-swept coal mill is the main equipment of cement plant, also called coal mill in cement plant, used for grinding and drying various hardness of coal, crushing the coal briquette Coal Mill In Cement Plant, Air-swept Coal Mill Coal Mill
احصل على السعر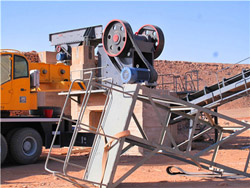
Analysis of material flow and consumption in cement
The coal mill is a vertical roller mill, in which the coal particles are collected in a bag filter through a grit separator. The required size of coal is 80% of 90 μm and less Coal mill. The coal mill uses coal, coke or grinded pet coke with different size of balls. Larger sized balls are used for impact grinding and the smaller balls are A critical review on energy use and savings in the cement industries
احصل على السعر
Coal Mill Systems ResearchGate
The role of vertical coal firing mills in cement plants are discussed. The potential risk of fire and even an explosion can be limited if the coal meal product is Cement production is one of the most energy-intensive manufacturing industries, and the milling circuit of cement plants consumes around 4% of a year's Modeling of energy consumption factors for an industrial cement
احصل على السعر
Coal Mill Coal Mill In Cement Plant AGICO Cement
In cement plants, we usually adopt the air swept coal mill system or vertical mill system as the pulverized coal preparation system, which is arranged at the cement kiln head or kiln The cement industry is one of the most intensive energy consumers in the industrial sectors. The energy consumption represents 40% to 60% of production cost. Additionally, the cement industry contributes around 5% Parametric Studies of Cement Production
احصل على السعر
Coal for cement: Present and future trends Global Cement
In July 2014, Sinai Cement Company (SCC) contracted FLSmidth to provide the equipment for it to replace natural gas and mazut with coal for cement production. Similarly, in October 2014, Misr Beni Suef Cement announced plans to build a US$27.9m coal mill by the end of 2015. Next, in November 2014, Titan Cement ordered a Gebr.Distribution of dust emissions at bag filters in the cement mill section no.1 (mill filterpoint A and separator filter-point B, Figure 1) of the analyzed cement plant.(PDF) Dust Emission Monitoring in Cement Plant Mills: A
احصل على السعر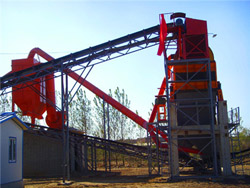
Coal and its application in the cement production process
According to calculations, a large amount of energy from coal is used to produce cement, of which it takes about 200 kg of coal to produce one ton of cement and about 300-400 kg of cement to produce one cubic meter of concrete. In addition to being a fuel, industrial coal also contributes to being one of the raw materials involved in the Cement has hydraulic properties like slaked lime and hardens when mixed with water. Compressive strength increases in time and reaches its practical top limit after 28 days. Mixing crushed stone(PDF) Mining Activities, Cement Production Process and
احصل على السعر
Coal Mill an overview ScienceDirect Topics
Observer-Based and Regression Model-Based Detection of Emerging Faults in Coal Mills. Peter Fogh Odgaard, Sten Bay Jørgensen, in Fault Detection, Supervision and Safety of Technical Processes 2006, 2007. 5.2 Experiments with and design of the regression model-based approach. Operating data from a coal mill is used to compare the fault detection cement ball mill. Application: limestone, clay, coal, feldspar, calcite, talc, iron ore, copper, phosphate, graphite, quartz, slag. Capacity: 0.65-615T/H. The cement ball mill usually can be applied to raw meal grinding or cement grinding. Besides, the cement ball mill also can be used for metallurgical, chemical, electric power, other miningRaw Mill, Cement Raw Mill, Raw Mill In Cement Plant Cement
احصل على السعر
Cement Analysis and Production Information Thermo
The cement production process begins with the extraction of limestone and clay from the quarry. The material is then blended, crushed and fed to the kiln. Post-kiln, the clinker is cooled and goes through a final grinding method before it is ready to ship. Portland cement, the most common type of cement, is formulated in a variety of strengths1 Potential safety hazards in the coal mill system. 1.1 Spontaneous combustion occurs. The process of cement production determines the need to use a large amount of coal. The use of coal is mostlyDISCUSSION ON SAFETY PRODUCTION OF COAL MILLING SYSTEM IN CEMENT
احصل على السعر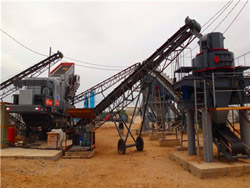
Dust Emission Monitoring in Cement Plant Mills: A Case
The cement factory where the measurements were made was located in Romania’s center-north and had a final section with two cement mills. Cement grinding was performed inside the cement mill workshop. This manufacturing phase’s product was cement—a powdery, finely ground material in closed-loop tubular ball mills . The monthly Gate to gate approach adapted in the mining process, raw mill, coal mill, clinker production (kiln and cooler), and finish mill and using SimaPro 8.5.2 with IMPACT 2002+ method.(PDF) ENVIRONMENTAL IMPACT ASSESSMENT
احصل على السعر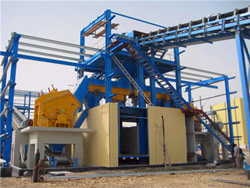
ATOX® Coal Mill FLSmidth
Our ATOX® Coal Mill has large rollers with great grinding capability of virtually all types of raw coal. The rollers work harmoniously with a highly-efficient separator and feed sluice to consistently and reliably deliver coal meal to your desired fineness and moisture level. ATOX® Coal Mill. what we offer key benefits product features downloads.VRM has been widely researched in processing of cement (Ito et al. 1997;Jorgensen 2005;Wang et al. 2009, Ghalandari et al. 2021), coal (Tontu 2020), iron ore (Reichert et al. 2015), zinc ore (vanAn investigation of performance characteristics
احصل على السعر
Air-Swept Coal Mill Of High Quality Fote Machinery
Air swept coal mill is widely used in cement industry, thermal power generation industry, metallurgical industry, chemical industry, sugar industry and other industries. 6.1 Air-swept coal mill in cement plants At present, most cement plants use coal as the main fuel in the clinker production process. Calcining high-quality cement clinker There are usually four kinds of VRMs in the cement production line, including raw meal mill, coal mill, Clinker Mill and cement mill, and the vertical mill occupies a large energy consumption unit. Therefore, it is necessary to optimize the multi-objective parameters of the VRM in order to improve the grinding performance and reduce energyRoller Mill Based on Experimental Method mdpi-res
احصل على السعر
Energy-Efficient Technologies in Cement Grinding IntechOpen
The energy consumption of the total grinding plant can be reduced by 20–30 % for cement clinker and 30–40 % for other raw materials. The overall grinding circuit efficiency and stability are improved. The maintenance cost of the ball mill is reduced as the lifetime of grinding media and partition grates is extended. 2.5.cement. Hence, one grinding compartment will generally suffice. For a coal mill, we usually recommend a light classifying liners and for raw mills we recommend heavy classifying liners. If the raw materials are particularly coarse, a mixed solution might be best. This could be either by replacing the first few rings e.g., the firstIG PERFORMANCE PARTS Mill Liners for Ball Mills
احصل على السعر
Raw Material Drying-Grinding Cement Plant Optimization
Ball mills for cement raw material and coal equipped with a drying compartment adequately air swept with hot gas (2.5-3.5M/sec above the ball charge), can handle moisture about 8%. Fully air- swept mills (5-6M/sec) can dry up to 12-14% moisture. Grinding Operation Objectives and KPIs: Highly energy intensive unit operation of size reduction inThe raw mill considered in this study is located in a cement plant located in Sanliurfa, Turkey. The plant is a single chamber mill with mechanical circulation system which grinds a medium hard material at a capacity of about 160 tons/h. The mill diameter is 4230 mm and the grinding chamber length is 10,950 mm (Table 1).Reducing energy consumption of a raw mill in cement industry
احصل على السعر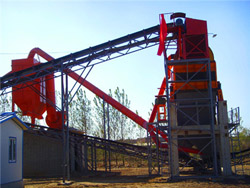
Cement Analysis and Production Information Thermo Fisher
The cement production process begins with the extraction of limestone and clay from the quarry. The material is then blended, crushed and fed to the kiln. Post-kiln, the clinker is cooled and goes through a final grinding method before it is ready to ship. Portland cement, the most common type of cement, is formulated in a variety of strengths
احصل على السعر- أنواع من اسم شركة تعدين الفحم يلقي مفتوحة
- limestone crusher machine in malaysia
- مصنعي كسارة رمل الحجر TON
- الحزام الناقل Peralatan الربط
- كسارة صدم المعادن الصغيرة الجزائر للبيع
- lelang belt conveyor bekas
- مواصفات آلة كسارة الحجر في الفلبين
- التعميم خام الحديد تهتز الشاشة
- آلة تكسير الحجر المتنقلة للبيع في مصر
- crushing mining crusher
- كسارة الحجر والنبات المحجر في أوبري
- إنتاج ركام الحجر المسحوق
- محطات التكسير شبه المتنقلة
- prices for grinder de walt dw
- أرخص وسيلة لسحق الحصى