اتصل
هاتف
+0086-371-86162511
عنوان
تشنغتشو ، الصين
iron ore ball mill pdf
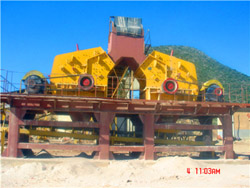
Optimization of Solids Concentration in Iron Ore
The paper demonstrates the application of this methodology to optimize solids concentration in ball milling of an iron ore Ball mill is the widely used comminution device for the size reduction of iron ore particles, yet the underlying mechan- isms of heat transfer and thermal breakage Advances in Mechanical Engineering 2021, Vol. 13(3) 1–9
احصل على السعر
(PDF) Optimization of Solids Concentration in Iron
The paper demonstrates the application of this methodology to optimize solids concentration in ball milling of an iron ore Objective: The dimensional properties of iron ore pellet feed including specific surface area and particle size distribution in the (PDF) Physicochemical Problems of Mineral
احصل على السعر
Mechanistic modeling and simulation of grinding iron ore
The present work analyzes the application of the UFRJ mechanistic ball mill model to grinding of iron ore pellet feed in an industrial grinding circuit. In order to An iron ore concentrate sample was ground separately in a pilot-scale HPGR mill in multiple passes and a dry open-circuit ball mill to increase the specific surface area of particles. Grinding iron ore concentrate by using HPGR and ball mills
احصل على السعر
Impact of ball filling rate and stirrer tip speed on milling iron ore
Xiao et al. [2] investigated the iron grade and recovery of fine grained magnetite ground by a stirred mill and ball mill. They found that the stirred mill was more Download PDF Abstract: Ball mills play a critical role in modern mining operations, making their bearing failures a significant concern due to the potential loss of [2311.13571] Ball Mill Fault Prediction Based on Deep
احصل على السعر
(PDF) Grinding in Ball Mills: Modeling and Process
PDF The paper presents an overview of the current methodology and practice in modeling and control of the grinding process in industrial ball mills. Find, read and cite all the...Ball mills are filled up to 40% with steel balls (with 30–80 mm diameter) which effectively grind the ore. The material to be ground fills the voids between the Comminution and classification technologies of iron ore
احصل على السعر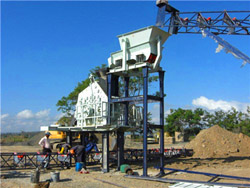
Investigation of iron ores based on the bond grindability test
The classification of different types of iron ore helps to run the plant scale ball mill by setting suitable operating parameters to the ball mill. Discover the world's research 25+ million membersThe feed samples of X, Y, and Z iron ores were ground in the BBM (ball mill refers to a BBM of size 300 mm × 300 mm with smooth liners) to identify the PSD, BWI, and RT of each ore. Grinding experiments were conducted according to Bond’s standard test procedure [].For each iron ore sample, the RT taken to produce 250% circulating Investigation on Iron Ore Grinding based on Particle Size Distribution
احصل على السعر
Optimization of Solids Concentration in Iron Ore
Important advances have been made in the last 60 years or so in the modeling of ball mills using mathematical formulas and models. One approach that has gained popularity is the population balance Ball Mills. The ore from the crushing section is delivered to the fine ore bin placed at the head of the grinding section, from which it is fed, together with water, Grinding Media & Ball Mill Liners. Balls are made of cast-iron, high-carbon, and chrome steel. Cast-iron balls are only used as a rule when they can be cheaply produced locallyBall Mills 911 Metallurgist
احصل على السعر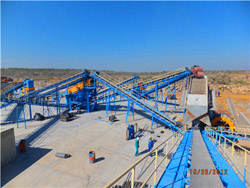
Friction and wear of liner and grinding ball in iron ore ball mill
Abstract. To understand the friction and wear of working mediums in iron ore ball mills, experiments were conducted using the ball cratering method under dry and wet milling conditions, whichThe motion of grinding media in a ball mill is essential since it has a grea t impact on the breakage of ore parti cles. When the mill speed increa ses, the charge motion changes from sliding to(PDF) Grinding Media in Ball Mills-A Review ResearchGate
احصل على السعر
Impact of ball filling rate and stirrer tip speed on milling iron ore
Xiao et al. [2] investigated the iron grade and recovery of fine grained magnetite ground by a stirred mill and ball mill. They found that the stirred mill was more beneficial for grinding P80 10–30 μm minerals to liberate more valuable minerals and the grade of iron concentrate was 5.2% higher than that of ball mill.2.2 Grinding Studies. Two kinds of mills, BBM and LBM, were used to achieve the desired P 80 passing percentage of 150 μm with an acceptable range of hematite liberation (> 75%) at optimum grinding time. The BBM is a standard ball mill having a length and diameter of 300 mm × 300 mm with smooth liner as shown in Fig. 2.A Estimation of Grinding Time for Desired Particle Size
احصل على السعر
Simulation of casting process: case study on the gating and
In this paper, the sand casting process was evaluated using ProCAST simulating software and practical experience for manufacturing of the high chromium stainless steel outlet diaphragms used in iron ore ball mill. In the simulation practice, the effects of feeding and gating designs on the liquid flow, heat transfer and solidification Product from the secondary ball mills is classified by cyclones and cyclone underflow is returned to ball mill feed and cyclone overflow reports to final product which has 80% passing 105 microns. After two stage of deslime cyclones, ore is sent for the reverse flotation to produce final product >65% iron for pallet production.Comminution and classification technologies of iron ore
احصل على السعر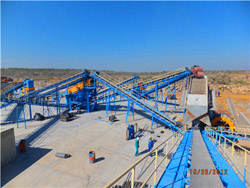
(PDF) Effect of wet ball milling on copper ore flotation by
If balls load is high (8710 gr), predominant comminution force turns to an abrasive force are resulted in fine and spherical particles due to an increase in the accumulation volume. When the ballMaterials were ground in a lab scale ball mill for 2hours with steel balls and size analysis of products were carried out using different size sieves (1, 0.5, 0.25, 0.15, 0.106 and 0.053mm). Microscopic Iron ore: Banded Hematite Jasper Iron Ore samples were col-lected from Odisha, India. Banded Iron Formations are chemicallyGrindability Studies of Mineral Materials of Different
احصل على السعر
KOBELCO Pelletizing Process
Iron ore must be shipped in bulk for maximum economy. 1.2 Pretreatment process In this process, the iron ore is ground into fines having qualities required for the subsequent balling process. The pretreatment includes concentrating, dewatering, grinding, drying and prewetting. In general, low-grade iron ore is ground into finesThe mill product, due to its physical properties, determines the efficiency of subsequent stages of classification, filtration and pelletizing, thus impacting the quality of iron ore pellets. The(PDF) Population balance model approach to ball mill
احصل على السعر
A Review of the Grinding Media in Ball Mills for Mineral
The ball mill is a rotating cylindrical vessel with grinding media inside, which is responsible for breaking the ore particles. Grinding media play an important role in the comminution of mineral ores in these mills. This work reviews the application of balls in mineral processing as a function of the materials used to manufacture them and the Effect of Slurry Density on Load Dynamic and Milling Performances in an Iron Ore Ball Mill -On-line Estimation of In-mill Slurry Density April 2012 DOI: 10.13140/2.1.4625.8561(PDF) Effect of Slurry Density on Load Dynamic and
احصل على السعر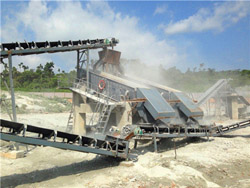
Optimization of Solids Concentration in Iron Ore Ball
The variable that can be more readily controlled in a wet ball mill in operation in industry is solids concentration, with selected studies having been conducted for iron ores. Martinovic et al. [18] measured the breakage rates at solids concentrations between 72 to 82% for an iron ore and found thatLoad behavior, iron ore particles, spher e-clump method, discr ete element method simula tion, ball mill Date received: 15 Nov ember 2016; accepted: 27 Mar ch 2017 Academic Editor: Filippo Berto(PDF) Discrete element method simulations of load
احصل على السعر
(PDF) Optimization of Solids Concentration in Iron Ore Ball
The paper demonstrates the application of this methodology to optimize solids concentration in ball milling of an iron ore from Brazil. The wet grinding experiments were conducted in bench (0.25 mThis result is typical for a feed that has some 4 × 6 mesh (oversized particles) iron ore: effective S value based on particles too large to be nipped by the ball size in the mill: 95% breakage at a grinding time of 8.1 min. of slurry, gives first-order kinetics of grinding and the same breakage parameters as dry grinding, except that the(PDF) Simulation of wet ball milling of iron ore at Carajas,
احصل على السعر- مصغرة آلة كسارة الحجر استئجار اسكتلندا
- خطة عمل معمل محجر المحاجر
- types of coal use in brick industry
- ماكينة طحن مخلفات النخل
- شركات تعدين الجبس في اليمن
- ارقام مغاسل سجاد توصيل للمنازل في خميس مشيط
- difference between hydraulic and cme cone crusher
- VSI سحق الرمال إنتاج
- صناعة كسارة الحجر في امريلي كمبوديا
- الرمال المعدنية آلة منفصلة
- slate stone powder production plant
- خط إنتاج معدات كسارة خام
- تعريف العلامة التجارية للمصنعين
- كسارة مخروطية متنقلة في جنوب أفريقيا كسارات مخروطية متنقلة
- benue cement production process