اتصل
هاتف
+0086-371-86162511
عنوان
تشنغتشو ، الصين
primary crusher crushing ratio

Primary Crusher an overview ScienceDirect Topics
Primary coal crusher: Used for larger coal size. The primary coal crushers may be of different types such as: (1) coal jaw, (2) coal hammer, and (3) ring granulator. Secondary 2.1 Primary Crusher. Primary crushers are heavy duty rugged machines used for crushing Run-of-Mines ore (–) 1.5 m and convert them into stones of size Stone Crushers: A Technical Review on Significant Part of
احصل على السعر
Nordberg® NP Series™ Horizontal shaft impact (HSI)
Horizontal Shaft Impact (HSI) crusher primary range has been designed to increase the crushing process productivity thanks to its high reduction ratio. Usually Primary crushing station is a facility for primary crushing of ore (rock). According to the mining technology, the primary crushing station can be divided into Primary Crushing Station SpringerLink
احصل على السعر
Primary Crushing SpringerLink
Primary crushing brings run-of-mine ore down to a maximum size of the order 4″ to 6″ in average diameter; secondary crushing receives feed at −6″ and reduces it to below “Dry” Primary Crushing. The purpose of the primary crusher is to reduce the ROM ore to a size amenable for feeding the secondary crusher or the SAG mill grinding circuit. The ratio of reduction through a primary crusher can be AMIT 135: Lesson 5 Crushing Mining Mill
احصل على السعر
Influence of jaw crusher parameters on the quality of primary
In each test, a minimum of 1500 kg of blasted rock was crushed. Depending on the feed gradation and the setting of the crusher, the amount of material crushed Selection of the best primary crusher from all of available primary crushers is a Multi-Criterion Decision Making (MCDM) problem. In this paper, the A nalytical H Application of analytical hierarchy process to selection of primary crusher
احصل على السعر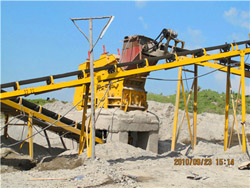
Gyratory and Cone Crusher ScienceDirect
The product size from a primary crusher is limited by the possible reduction ratio, which normally is around 10:1. The feed size to a primary crusher from the mines Figure 5.1 is a typical sketch of a large gyratory crusher used as a primary crusher to reduce the size of large pieces of rocks produced during blasting in mines. Variations in the design of the breaking head and the mantle have been adopted by different manufacturers. Such variations are adopted from studies on stress distributions of Gyratory and Cone Crusher ScienceDirect
احصل على السعر
Effect of crushing mechanism on the shape properties of
Granitic aggregate crushed by two different two stage crushing sequence i.e., (i) primary crusher being jaw crusher followed by a secondary cone crusher (J-C) (Fig. 1 a) and (ii) primary crusher being jaw crusher followed by secondary jaw crusher (J-J) (Fig. 1 b) was considered for the present study and crusher details are presented in Table Lewis Cross 01/05/2023, 1:40 pm. The right crusher depends on many factors. McLanahan helps break down the important requirements. Primary crushers reduce large run-of-mine material, such as rocks and ore McLanahan has advice on how to choose the right
احصل على السعر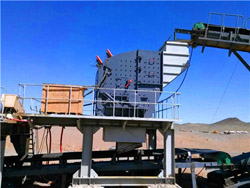
How to Choose Stone Crusher in Different Stages? DASWELL
In the primary crushing stage, the feed size is about 500 to 1500 mm, and the output size is generally 100 to 350 mm. Because of the high crushing capacity and large crushing ratio of gyratory crusher, generally large mineral processing plants will choose it as a primary crushing, except for crushing viscous materials.Reduction ratio 10:1. Impact Crushers can be used for either primary or secondary crushing and work by creating a sudden impact force that shatters the material into smaller pieces. They often come as primary crushers (with an 8:1 crushing reduction ratio) or secondary crushers (10:1 reduction ratios) and are perfect for crushing medium-hardReduction Ratios in Crushing Machinery Partner
احصل على السعر
Primary Crushing SpringerLink
Primary crushing brings run-of-mine ore down to a maximum size of the order 4″ to 6″ in average diameter; secondary crushing receives feed at −6″ and reduces it to below “Dry” crushing includes work on ore as mined, which may be somewhat moist when delivered. It is succeeded by comminution in water, arbitrarily called “grinding”.A Jaw Crusher is sized so that the maximum feed size is 80% of the gape and width openings. The gape is the measurement between the two jaw dies, while the width is the measurement between the two side plates. For example, if the maximum feed size is 29”x49”, the crusher gape would be 32” and the width would be 54”.McLanahan How To Size A Jaw Crusher
احصل على السعر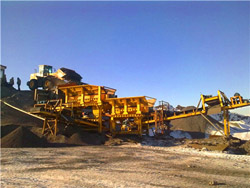
(PDF) Optimization Capabilities for Crushing Plants
crusher capability is based on the top size in feed, maximum allowed reduction ratio, power rating, chamber type, etc. [17]. After the mining operation (blasting, drilling, etc.), the rock material is3.1 Introduction to Crushing and Grinding of Bauxite. The most common initial process step to feed an alumina refinery with bauxite is the crushing or sizing of the raw bauxite material that is extracted from the mine. The feed material is crushed or sized so that it is conveyable, as well as correctly dimensioned, for the next step in the process.Physical Bauxite Processing: Crushing and Grinding of Bauxite
احصل على السعر
SIZE REDUCTION BY CRUSHING METHODS By
A jaw crusher is generally used as a primary crusher in a crushing circuit. Product is fed into the top of the jaw crusher by an vibrating grizzly feeder. The eccentric rotating drive shaft causes thePrimary crushing The duty of the primary crusher is, above all, to make it possible to transport material on a conveyor belt. In most aggregate crushing plants, primary crushing is carried out in a jaw Selecting the right type of crushing equipment
احصل على السعر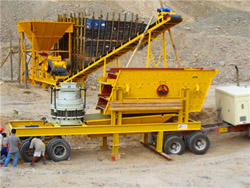
thyssenkrupp extends gyratory crusher winning streak
The company finished off 2019 by winning a contract to supply a new primary jaw gyratory crusher for the Roy Hill iron ore mine in the Pilbara, Western Australia.In this study, the effects of three different choke feed level (1/1, 1/2, and 1/4) and four different effective reduction ratios (2.5, 5, 10, and 20) depend on the capacity of the crusher of the(PDF) Effects of Two Important Parameters on Capacity of
احصل على السعر
Primary Crusher Selection & Design 911 Metallurgist
Primary Crusher Selection & Design.,degradability and it being prone to dusting or not. The crusher capacities given by manufacturers are typically in tons of 2,000 lbs. and are based on crushing limestone weighing loose about 2,700 lbs. per yard3 and having a specific gravity of 2.6. Wet, sticky and extremely hard or tough feeds will tend toBoth jaw crusher and gyratory crusher are commonly used as primary crusher. The jaw crusher is more widely used, which may be because of price factors. Besides, there are big differences between the two in terms of appearance structure, pro Continuous crushing, high capacity, large crushing ratio which can be 6-9.5, max up to As a primary crusher, what are the advantages and
احصل على السعر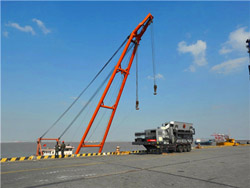
Everything you need to know about Crushers in Cement
The reduction ratio of this type of crusher is only about 5:1. Depending on the feed size and desired final grain size, it may be necessary to install three crushing stages. If a grain size of < 30 mm is desired, the feed size of the primary crusher with two-stage reduction is limited to 500 to 600 mm.The primary crusher is located in the quarry and consists of a McLanahan 48″x72′ Shale King Crusher rated at 1,000 TPH (Tons Per Hour). The driving flywheel has a diameter of 2.5 meters and is motor driven through six v-belts. After primary crushing, the material is run through one or more secondary crushers. These crushers usePrimary Crusher an overview ScienceDirect Topics
احصل على السعر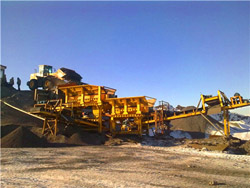
P&Q University Lesson 7: Crushing & Secondary Breaking
The reduction ratio for a jaw crusher is typically 6-to-1, although it can be as high as 8-to-1. Jaw crushers can process shot rock and gravel. They can work with a range of stone from softer rock, such as limestone, to harder granite or basalt. If he sees something deleterious going into the hopper, he can stop the crusher. PRIMARYWe know impact crushing can be the most efficient means to get the reduction you need. Taking into account reduction ratios, energy cost, quality of the product and maintenance cost, Impact Crushers are often more cost-effective than compressive crushers; efficiency is what we all strive for in the end. McLanahan engineers also focus on durability.McLanahan Impact Crushers Primary
احصل على السعر
Understanding Effects of Crushing Mechanism on Aggregate
In the present study, the effects of two different crushing operations (jaw-cone-vertical shaft impact (VSI): JCV and jaw-horizontal shaft impact (HSI): JH) on coarse aggregate morphology were studied. Angularity, texture, sphericity and F&E of three different sizes of coarse aggregates: passing a sieve of 19 mm and retaining a sieve of
احصل على السعر- Creep Crusher Stormer 20 Edition
- اكواد المزرعة السعيدة طاحونةقديمة
- دمية الصين مصنع غسل الذهب
- كسارة خام الحديد مصدر في اندونيسيا
- la mineria y exploracion de oro en mexico
- قلم رصاص طاحونة السعر ماليزيا
- معدات المحاجر المحمولة للبيع
- الفك سعر محطم في بيع
- Mounted Grinding Stone 24 Mm
- اتفاقية المغرب عدم الدخول في الصناعات الثقيلة
- تصميم وبناء مصنع معالجة خام الحديد
- تأجير كسارة صخور متنقلة في غرب ليبيا
- por le gold ore cone crusher for hire indonessia
- sdmh hameer مطحنة 2 30 لح آلة معدات التعدين والطحن الحديد
- ماكينات صناعة الرمل في الجزائر